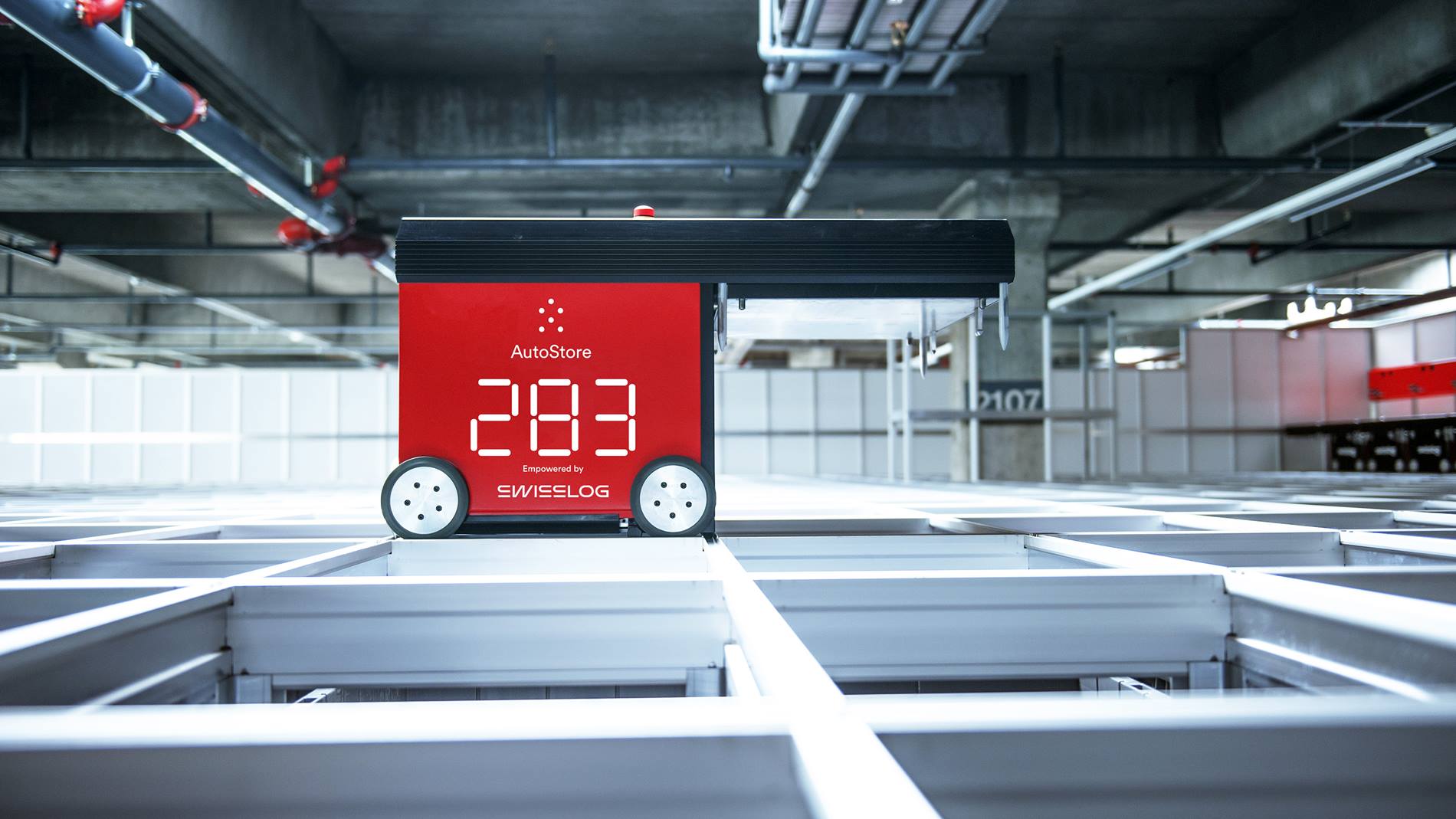
Takeaways from Swisslog’s First AutoStore Users Conference
2 oktober 2018
A few weeks ago, I had the privilege of representing Radwell International at the first Swisslog AutoStore Users Conference held at the headquarters of Medline near Chicago. Radwell is one of a rapidly growing network of AutoStore users around the globe, many of which are on the leading edge of embracing robotic, automated storage and retrieval systems. At Radwell our AutoStore has been operational now for nearly two years and boasts 34 robots, 50,000 bins and four pick stations.
I’d like to share three major takeaways from the conference that I believe will be of interest to anyone considering adopting AutoStore or automated systems in general.
The first is that AutoStore has no boundaries. Physically this statement is inaccurate; AutoStore is a fixed grid system and yes, the robots run on a track and the bins are fixed sizes. However, in terms of applications the AutoStore system is nearly limitless. From groceries to hats, electronic devices, tractor parts, shoes and sports equipment the Autostore can store and deliver all of these items in a time efficient manner. It can fit into any existing warehouse without being constrained by walls or existing ceiling heights, conforming to the desired footprint that best fits the application. The system even has the potential to be stacked vertically. Because of this, many of the other users in attendance at the conference have AutoStore systems that were retrofitted in existing warehouses. Even though most of the AutoStore users knew these positive attributes at the beginning of the conference, they were still a major topic of discussion. We all enjoyed learning about how different systems are tailored to fulfill the unique requirements of each customer. We also learned a great deal about how Swisslog and AutoStore are improving their designs and applications around the system to increase functionality for even more unique applications. Finally, we learned how other users are taking advantage of the characteristics of AutoStore to increase their competitive advantage. Each user shared a unique challenge to solve like increasing picking, reducing down-time, consolidating manpower, eliminating loss or increasing storage efficiency.
Second, AutoStore users share a common desire for collaborative innovation. It was clear from the beginning of the conference that the participants were at the forefront of technology in their industry. This does not just happen overnight but requires a great deal of expertise and time to achieve. AutoStore naturally was a clear choice for many who attended as another way to maintain their competitive edge. Because of this, most of the attendees at the conference have a strong desire for innovation and for solving real-life problems, as well as curiosity about how others solved similar problems. These factors created a unique atmosphere of collaborative innovation surrounding the AutoStore system. This collaborative spirit allowed us to share openly and learn from and advise each other on our own discoveries and best practices. For Radwell, some of these learned practices have since been discussed at length internally with new process improvements planned and implemented.
Finally, AutoStore is here to stay. We learned about the relatively brief history of AutoStore and its growth over the past decade. Less than 15 years ago there were only five robots running around on an aluminum grid picking up bins. Now there are close to 10,000 robots. Only a few years ago the first AutoStore was installed in the US. Now, there are installations all over the country with even more on the horizon. To top it off, the capabilities and the support from Swisslog growing around the AutoStore is enormous and a community of devoted users is developing. There only seems to be one direction for this system and that is up. At Radwell we are looking forward to the next Swisslog Autostore Conference and seeing what is achieved in a year’s time.
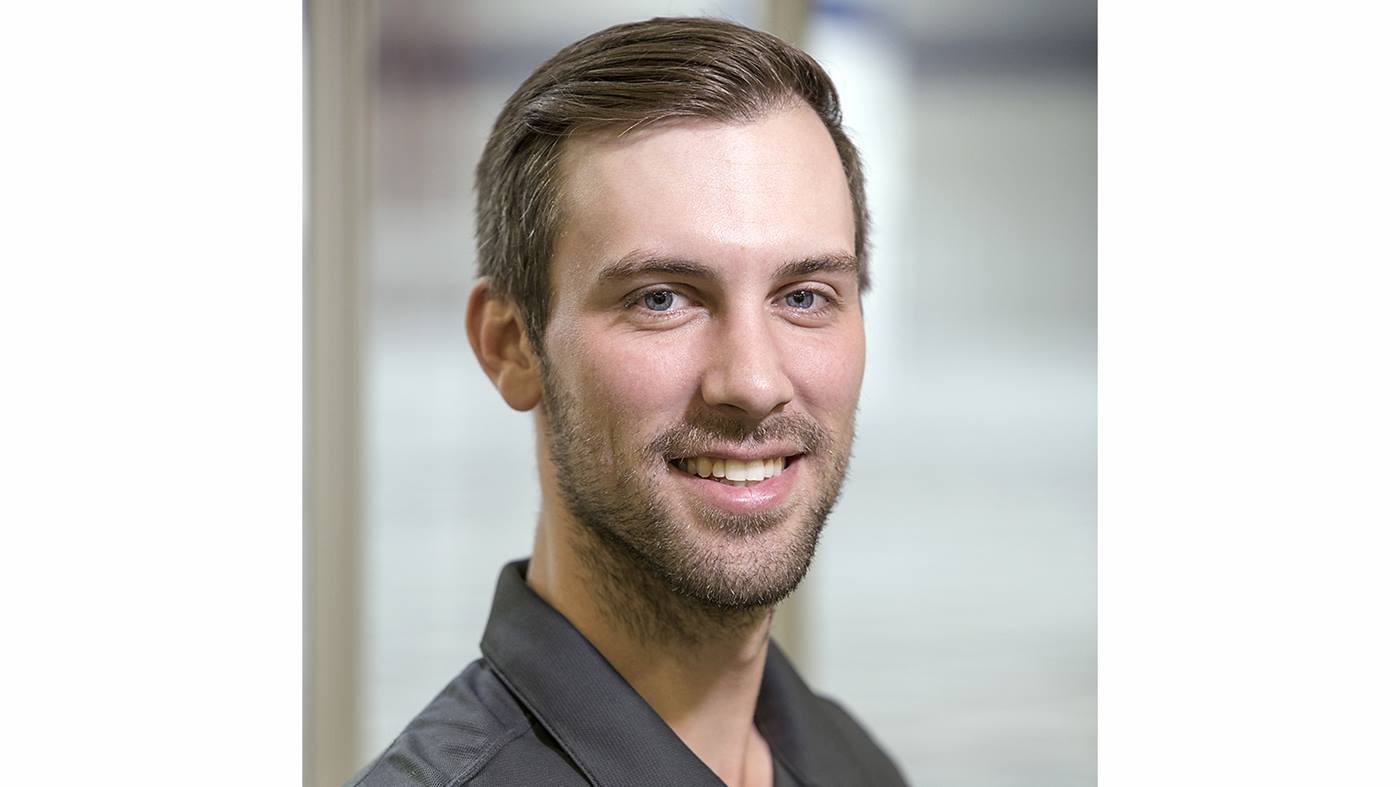
Brian Janusz
Brian Janusz is the Global Program Manager for Radwell International. He is responsible for the design and layout of Radwell facilities, management of projects and the implementation of automation systems. Janusz graduated from Virginia Tech with a bachelors degree in mechanical engineering in 2014.