Reducing Labor Dependencies in E-grocery Fulfillment
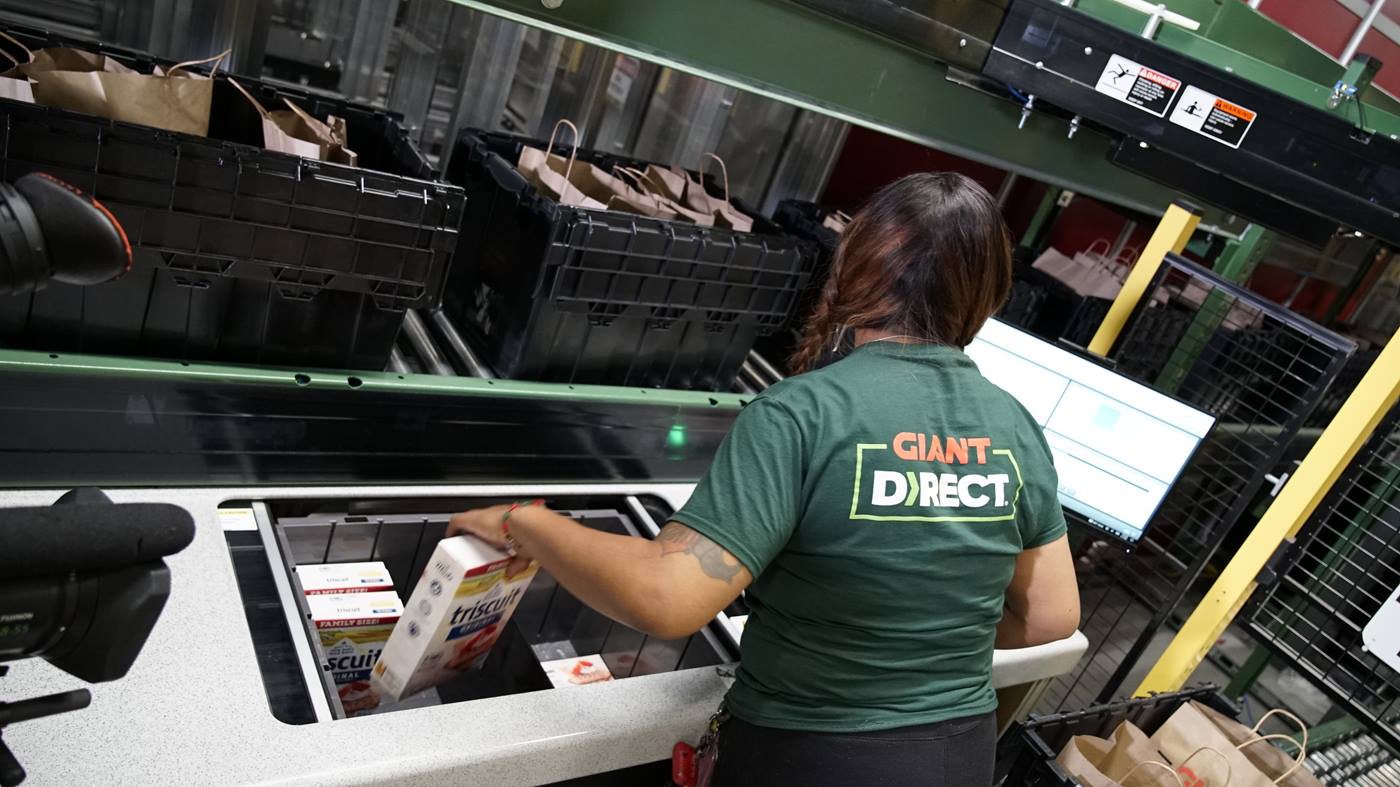
That’s a problem for two reasons. The first, of course, is costs. E-grocery shifts the burden of filling orders from the customer to the grocer and that cuts into already thin margins in grocery. Driving down labor costs is often the key to achieving e-grocery profitability. The other reason is the scarcity of labor in many markets. The more dependent grocers are on labor to fulfill orders, the more at risk they are of not being able to scale with growing demand or meet customer expectations.
Quantifying the Impact of Automation on Labor Requirements in E-grocery Fulfillment
The best measure of productivity in a fulfillment center environment is total units per hour (TUPH). TUPH quantifies the number of units processed per manhour across all operations from receiving through dispatch, including replenishing/decanting, picking, and consolidating and loading orders into customer vehicles or delivery vans.
At Swisslog, we created a model of an e-grocery fulfillment center to enable us to analyze the components of TUPH for three different fulfillment scenarios: fully manual operation, goods-to-person automation with all human pickers, and goods-to-person automation with 50% of order volume picked by robots.
It shouldn’t be a surprise that picking is by far the largest contributor to TUPH in the first scenario. Without automation, picking accounts for almost half (48%) of the manhours required to fulfill orders and prepare them for pickup or delivery. The next largest contributor to TUPH in this scenario is replenishing shelves at 27%.
By introducing goods-to-person automation into this environment and keeping the number of orders per hour constant, the manhours required to support picking are cut by 36% and productivity for the site improves 49% because the hours required to replenish inventory are also reduced. Most importantly, fulfillment costs as a percent of basket are reduced 41%.
It’s important to note that these productivity and cost improvements were achieved by automating a dense, dedicated e-grocery fulfillment center. It’s reasonable to assume that grocers currently fulfilling orders manually by picking from store shelves will see a much greater improvement.
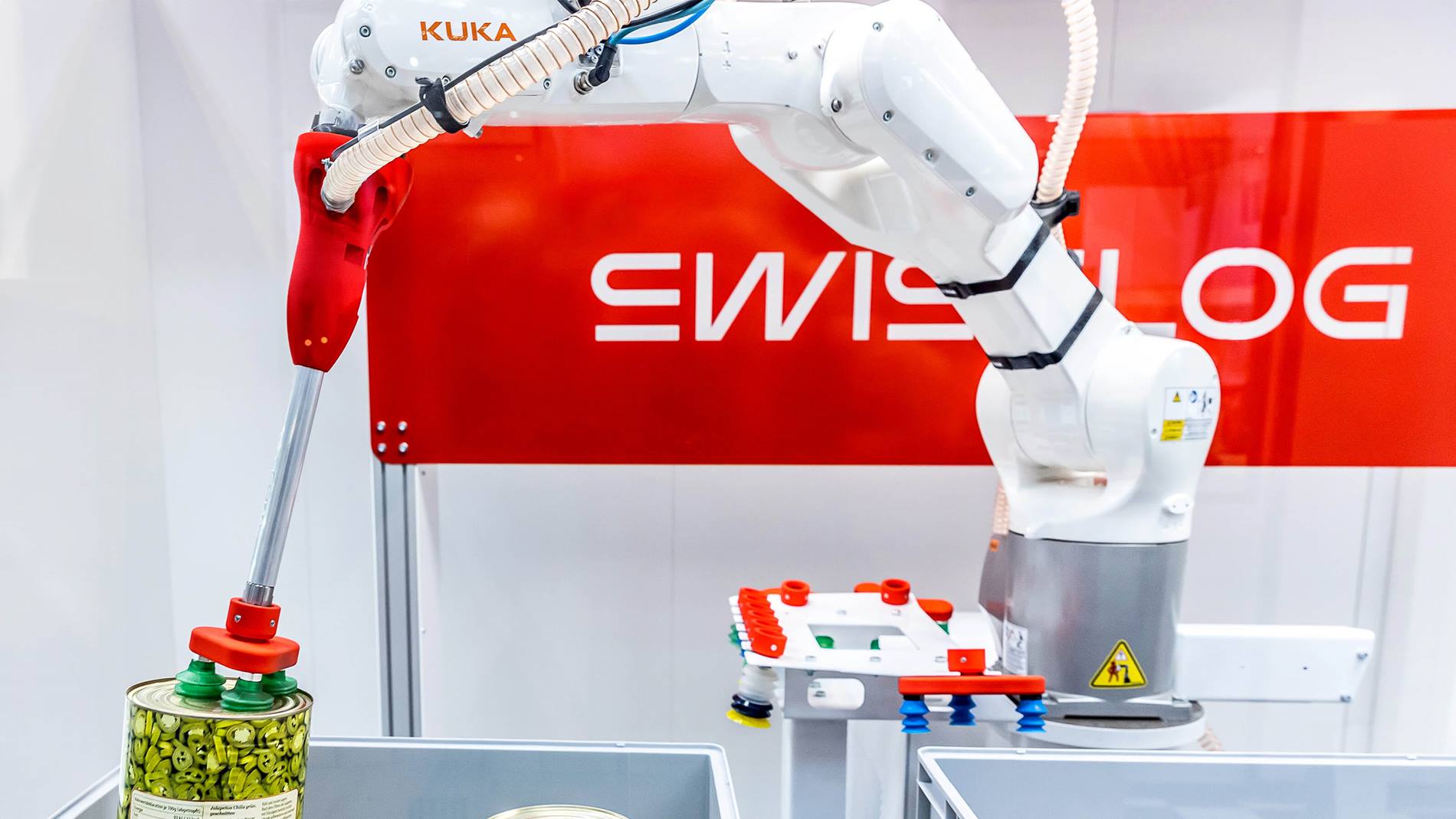
Adding Robotic Item Picking
Grocers considering automation today should also remember that goods-to-person automation can do more than improve productivity by eliminating the travel time associated with traditional picking. They also establish a platform that enables automation of the picking process itself.
The current generation of item-picking robots can pick about 50% of the items in a typical e-grocery basket and that creates the opportunity to drive further productivity improvements. Using the same fulfillment center and order volume, we analyzed the impact on costs and productivity if half of the volume required to fulfill orders was picked by robots.
Compared to fully manual operation, a goods-to-person automation system using a mix of human and robotic pickers creates a 156% improvement in productivity. Compared to goods-to-person automation with all picking performed by humans, productivity is improved by 55%.
And as the level of automation increases, the cost of fulfillment as a percent of basket decreases, dropping 41% with the introduction of goods-to-person automation and an additional 33% with the introduction of robotic item picking.
Planning for Profitability and Productivity
This is encouraging news for grocers considering the move to automation as it highlights the potential to dramatically cut their dependence on labor and drive down costs.
But it’s important to remember that robotic item pickers can’t do everything humans can do within the goods-to-person environment. In other words, you can’t simply place a robot in a pick station where a human has been working.
Pick stations supporting robots require extra infrastructure for tasks like bin handling and inserting bags into bins and that infrastructure should be considered in the planning of a goods-to-person automation system today as it can be challenging to add to an existing automated site. Even if you aren’t planning to deploy robotic item picking in the first phase of your automation, it may make sense to design pick stations to enable a smooth transition to robotic picking that maximizes your productivity and drives down fulfillment costs.
At Swisslog, we work with grocers at all stages of their e-grocery evolution, delivering solutions that meet or exceed projected results within weeks of startup while enabling continuous optimizations that unlock higher levels of performance. To learn more about how we are designing e-grocery automation to maximize productivity and lower fulfillment costs, contact us.