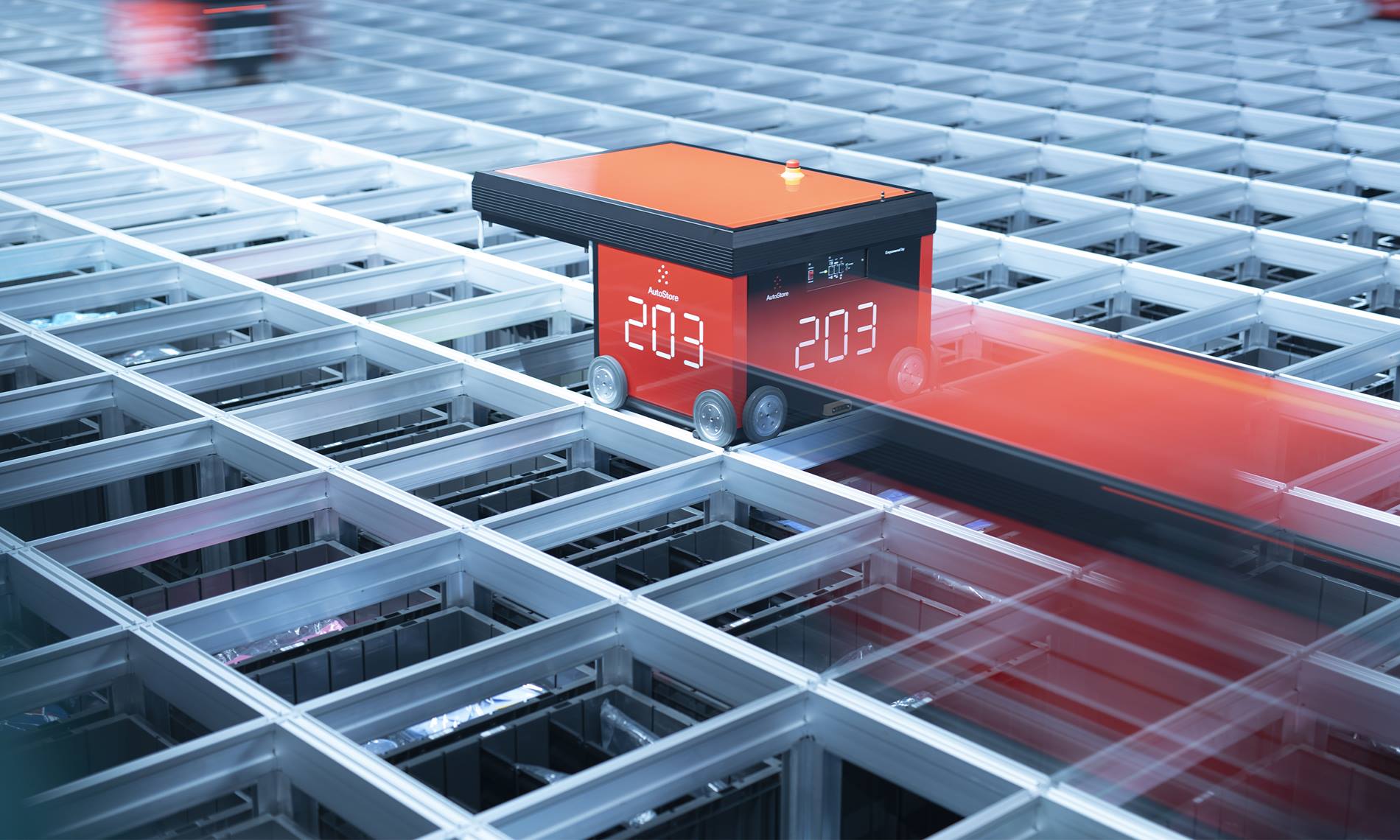
The Business Case for Automating Industrial Equipment Parts Management
February 22, 2019
OEM parts distribution has been slow to adopt material handling automation because their priorities are storage and item availability in an ever-growing, high-SKU environment. But a modern technology solution can cost-effectively manage huge inventories while increasing operational efficiency and adapting to future requirements.
Behind every industrial manufacturer there’s a spare parts organization that plays a critical role in keeping equipment running. But what is it that keeps the parts distribution operation running?
Today, it’s largely conventional manual processes that are being stretched to the breaking point by ever-expanding inventories and the need to juggle a range of order types. The resulting inefficiencies are overlooked due to the operation’s laser focus on keeping high-capital assets running and maintaining solid customer relationships.
Many parts operations don’t consider automation because their throughput is low compared to more prevalent retail distribution chains. But, the value of automation extends far beyond labor savings and increased throughputs. In fact, low throughput (<400 order lines/hour) operations, such as parts distribution, can be among the biggest beneficiaries of automation when they choose the right solution.
Consider the challenges parts distributors face today. They start with SKU proliferation. Retailers may think they have it tough when the number of SKUs grows into the tens of thousands, but parts manufacturers often deal with SKU counts in the millions. Each year that number grows as new models are introduced while legacy systems must continue to be supported—often beyond their 30-year service life.
And even more challenging from an inventory management perspective, their legacy system parts often become very slow moving. In fact, I’ve heard warehouse managers unaffectionately refer to these slow-movers as ‘dogs.’ Yet, they understand that, when needed, these dogs can be a key lynchpin for a multimillion dollar operating system.
As inventories expand, available storage space gets squeezed tighter and slow-moving parts get bounced around and often end up in some corner of the warehouse where they take longer to find. Each time they are moved they can get damaged and the longer they are in storage, the more dust and condensation they collect.
Parts distribution operations also typically deal with multiple order types, each with its own requirements. Equipment refurbishing programs, whether conducted internally or on-site, require complex orders with parts coming from multiple sources over a period of weeks. Staging orders can consume valuable warehouse space and parts may be moved two or three times as the order is assembled, increasing the likelihood of damage or error.
In addition to these complex orders, parts operations also support routine replenishment of their customers on-site parts inventory and extremely time-sensitive one-off orders. In our experience, it’s common for parts managers to have to stop everything they are working on to find a part—maybe one of their ‘dogs’—that their customer needs immediately.
Finally, there’s the challenge of managing returns. In some businesses that deal with seasonal demand, such as agriculture, the manufacturer may stock local distributors for the busiest season and then be forced to accept the return of unsold parts, which must be manually returned to inventory.
So, while throughputs may not be as high as applications typically targeted for automation, inventory management challenges can be even more difficult compared to other industries. These ‘dense-storage’ challenges can best be addressed through automation.
At Swisslog, we’ve helped parts operations automate to improve space utilization, minimize disruption of one-off orders and streamline the preparation of complex orders.
In our experience, the best solution for dense-storage parts distribution is often the AutoStore system. AutoStore consists of a three-dimensional grid of bins that are retrieved by robots traveling across the top of the grid. This solution has several unique advantages that directly address the challenges of parts distribution operations.
First, it offers extremely dense storage. Slow moving parts can be consolidated in the grid, reducing space required for inventory by up to 60 percent compared to racks of shelves. If you’re worried that you have too many SKUs for an automated system, consider that Swisslog customer Radwell International uses AutoStore to enhance the management of its inventory of more than 22 million parts.
Because of the way AutoStore robots retrieve bins from the top, slow-moving products naturally migrate to the lower levels of the grid where they are sealed from air and moisture by the bin above them. This ensures that parts that may only be accessed once or twice a year remain in pristine condition while in storage.
AutoStore also contributes to the efficiency and accuracy of handling complex, multi-source orders. We know that some refurbishment projects can require 400 or more parts with those parts coming from inventory, external suppliers and manufacturing. With AutoStore, parts from inventory can be consolidated in a single bin. Then, as parts are received from external suppliers or manufacturing, they can be added to the bin, which is retrieved on demand by the AutoStore robots, until the order is complete.
At any time, robots can quickly prioritize time-sensitive orders and then turn back to other orders once the critical order has been fulfilled. In the same way, AutoStore simplifies the management of returns.
Other benefits of the AutoStore system include its scalability and reliability. With the modular AutoStore system additional storage can be added without disrupting operations. AutoStore robots can reach any part of the grid at any time, so no single failure point prevents the system from pulling orders, allowing AutoStore to deliver excellent uptime and easily support 24x7 parts operations.
At Swisslog, we’ve deployed more than 130 AutoStore systems across a range of industries and the business case for dense-storage parts distribution is among the strongest. The system is very cost effective when throughputs aren’t high and inventory is large. You can start with an easy-to-implement standalone system that can later be integrated with other systems and processes—or continue to function as a stand-alone system.
With AutoStore, parts distributors can continue to expand their inventory while reducing pick times, increasing space utilization, improving quality and simplifying the processes associated with complex orders. To learn more about AutoStore, see how industrial parts distributor and refurbisher Radwell International is using the system.