Is Your Warehouse a Candidate for Automation?
Kenneth Hayer
20 September, 2021
Reading Time:
3 min.
Some operators with older warehouses may feel left behind by this new wave of warehouse technology.
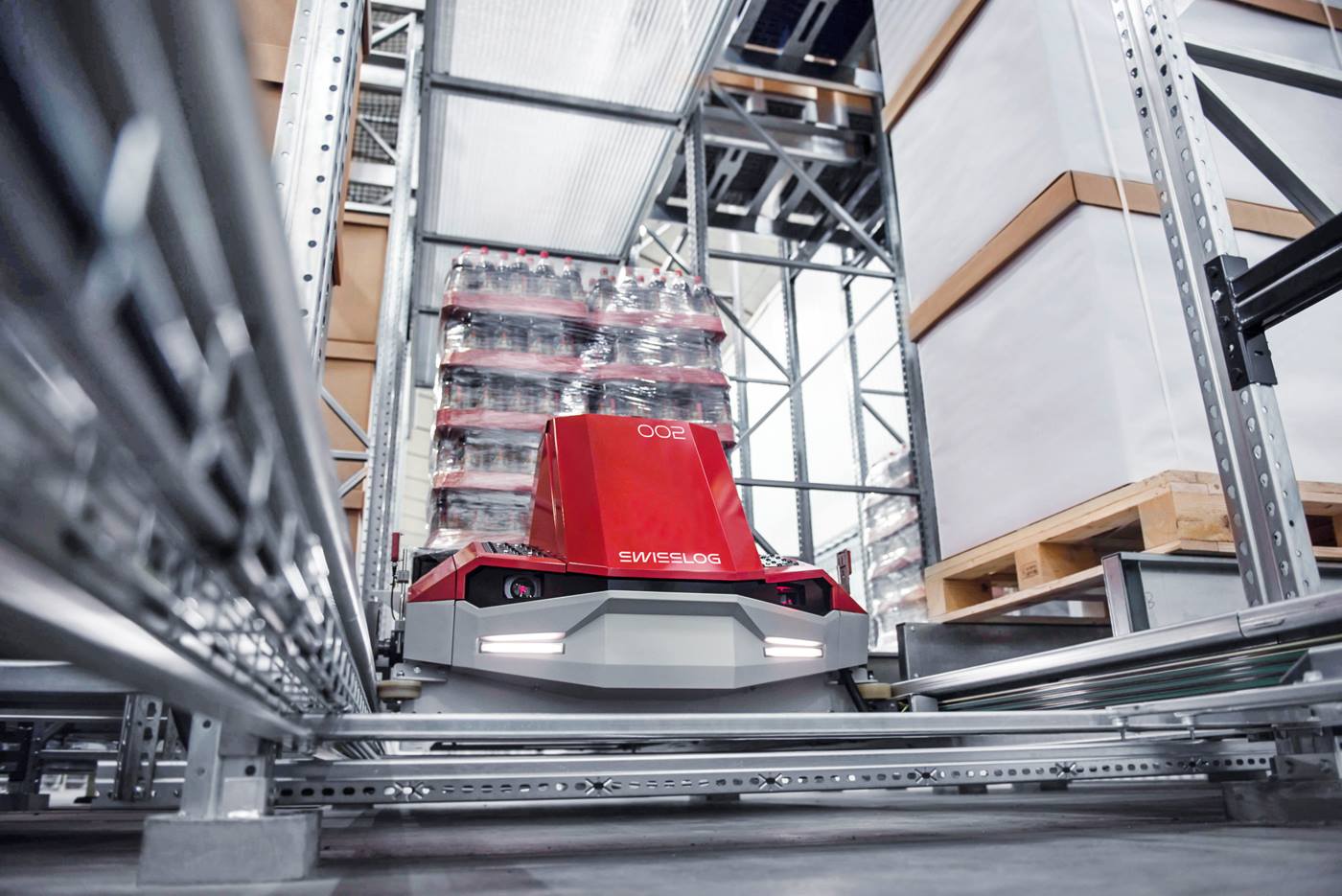
Robotic material handling systems, such as pallet shuttles and goods-to-person AS/RS systems, are proliferating because they are ideally suited to meet the needs of today’s warehouses. Offering exceptional storage density, high throughput, enhanced sustainability and improved accuracy and productivity, these systems are helping warehouse operators and supply chain managers deal with SKU growth, fluctuations in demand and changing customer expectations.
Some operators with older warehouses may feel left behind by this new wave of warehouse technology. They may believe they have no choice but to live with the limitations of their current processes and systems or may even be considering investing in a new build to address the challenges they face. Fortunately, there is a third alternative: adding automation to the existing facility.
Some operators with older warehouses may feel left behind by this new wave of warehouse technology. They may believe they have no choice but to live with the limitations of their current processes and systems or may even be considering investing in a new build to address the challenges they face. Fortunately, there is a third alternative: adding automation to the existing facility.
Retrofitting Brownfield Warehouses with Robotic Automation
Unlike older mechanized approaches to warehouse automation, today’s robotic-based systems are adaptable to their environment. Their flexible configuration options allow them to work in a variety of building shapes and sizes and even around obstructions such as columns. They also feature a modular design that enables a phased approach to implementation that can allow the warehouse to continue to serve customers while automation is deployed.
There are some challenges that may need to be addressed in older facilities, such as cracked or uneven floors. However, it’s much less expensive to repair or replace a cracked floor than to build a new facility. And lower capital costs are just one of the many benefits you can realize by adding automation to an existing warehouse.
AS/RS systems, such as Swisslog’s PowerStore pallet shuttle, can deliver up to 60% more storage capacity than existing shelfing or pallet storage, expanding warehouse capacity and freeing up space for other processes. In each-picking applications, goods-to-person AS/RS systems, such as AutoStore and CycloneCarrier, deliver productivity improvements of 200% to 300% with picking accuracy of 99% or better.
Automation can also reduce the environmental footprint of the facility by minimizing interplant and intra-plant transportation requirements, and the automation software delivers better visibility into product inventory, enhanced performance reporting and synchronization of manual and automated processes.
In short, you get the full benefits of today’s data-driven, robotic, and flexible automation technologies faster and at lower cost than you would by building a new automated warehouse.
There are some challenges that may need to be addressed in older facilities, such as cracked or uneven floors. However, it’s much less expensive to repair or replace a cracked floor than to build a new facility. And lower capital costs are just one of the many benefits you can realize by adding automation to an existing warehouse.
AS/RS systems, such as Swisslog’s PowerStore pallet shuttle, can deliver up to 60% more storage capacity than existing shelfing or pallet storage, expanding warehouse capacity and freeing up space for other processes. In each-picking applications, goods-to-person AS/RS systems, such as AutoStore and CycloneCarrier, deliver productivity improvements of 200% to 300% with picking accuracy of 99% or better.
Automation can also reduce the environmental footprint of the facility by minimizing interplant and intra-plant transportation requirements, and the automation software delivers better visibility into product inventory, enhanced performance reporting and synchronization of manual and automated processes.
In short, you get the full benefits of today’s data-driven, robotic, and flexible automation technologies faster and at lower cost than you would by building a new automated warehouse.
The Swisslog Retrofit Process
The first step in adding automation to an existing building is a site assessment. The Swisslog site assessment process is designed to help you determine the feasibility of your facility to accommodate automation and identify any limitations that must be addressed before automation can be deployed. One of the benefits of working with Swisslog is that we offer a full range of pallet-handling as well as case and each-picking technologies, allowing us to tailor solutions to specific structural requirements as well as density and throughput objectives.
Regardless of the automation system selected, implementation must be carefully managed to minimize disruption on current operations. Our process can often be accomplished while the facility continues to serve customers using established manual processes.
One approach that has been successful is to consolidate inventory in one area of the warehouse to free up space for the initial phase of the automation deployment. The first module of the automation system is then deployed and brought on-line as a pilot and the warehouse operates in hybrid manual-automated mode while the next module is deployed. Alternately, we’ve worked with customers who have been able to transfer some inventory to secondary locations to free up space for the first phase of implementation. Once the first module is deployed, inventory is transferred back to the facility and the increased storage density provided by the automation system can be leveraged to free up space for additional modules.
Regardless of the automation system selected, implementation must be carefully managed to minimize disruption on current operations. Our process can often be accomplished while the facility continues to serve customers using established manual processes.
One approach that has been successful is to consolidate inventory in one area of the warehouse to free up space for the initial phase of the automation deployment. The first module of the automation system is then deployed and brought on-line as a pilot and the warehouse operates in hybrid manual-automated mode while the next module is deployed. Alternately, we’ve worked with customers who have been able to transfer some inventory to secondary locations to free up space for the first phase of implementation. Once the first module is deployed, inventory is transferred back to the facility and the increased storage density provided by the automation system can be leveraged to free up space for additional modules.
Giving New Life to Older Warehouses
If you’re dealing with SKU proliferation, experiencing deteriorating service levels, struggling to maintain efficiency and productivity goals, or having trouble recruiting and retaining labor, a warehouse automation project can solve your operating problems while extending the life and value of your warehouse.
For more information on automating existing warehouses, read our white paper, Implementing Warehouse Automation in Brownfield Sites, or contact us to schedule a site assessment.
For more information on automating existing warehouses, read our white paper, Implementing Warehouse Automation in Brownfield Sites, or contact us to schedule a site assessment.