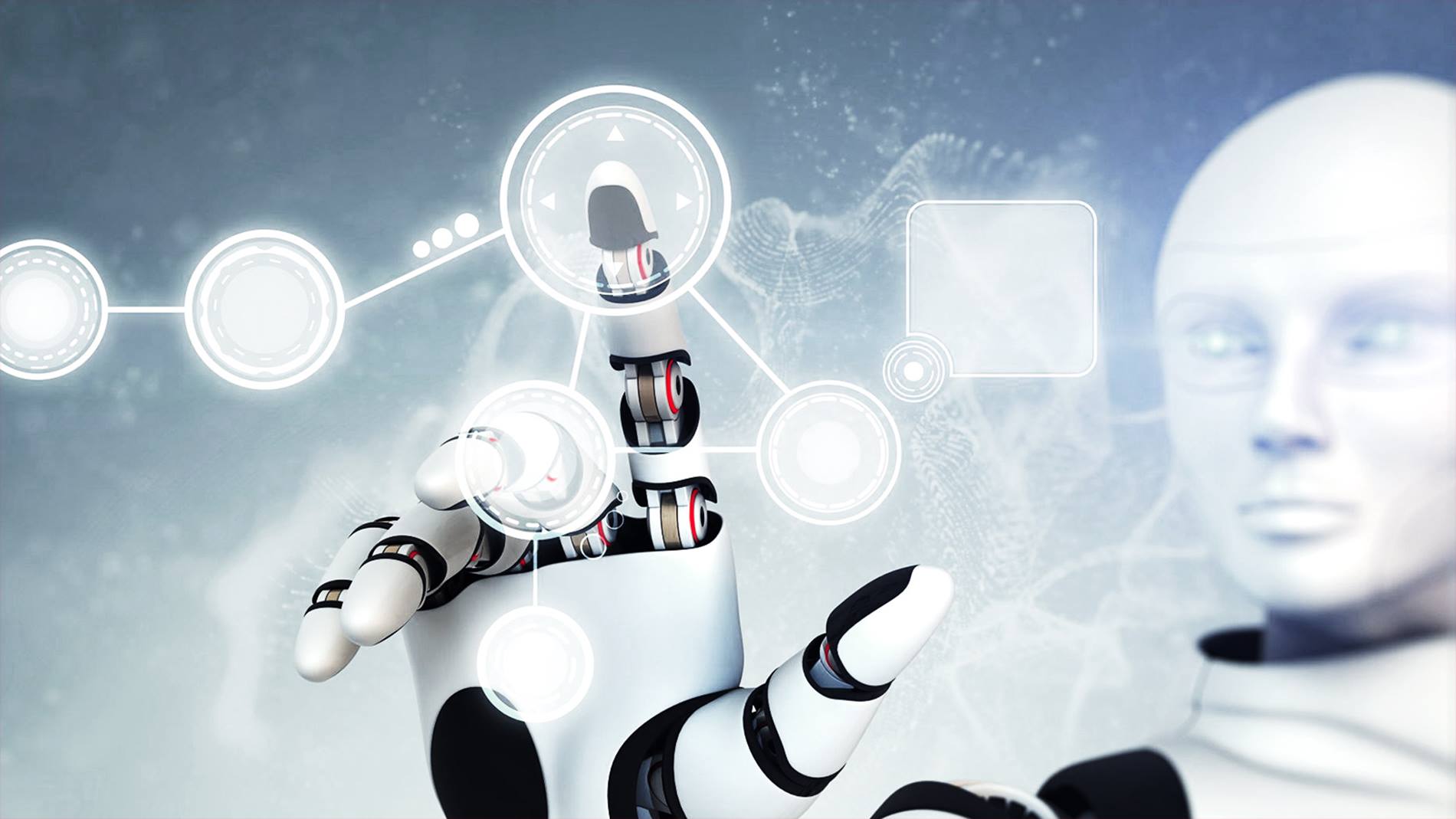
Our New Robot Partners
10 May 2016
Michiel Veenman, Director Solution Management Pharmaceutical Industry at Swisslog WDS considers how automation will improve validation.
In the not too distant past, people saw the moving robot as potentially dangerous, not malicious in the way science fiction might have us believe, but a potentially hazardous machine that required us to keep our distance.
Today, we’re much more comfortable with our new robot partners. A new generation of safer, human-collaborative robots are available at home and at work, raising the prospect of new collaborative processes within pharmaceutical factory logistics. But how might such an approach impact on process compliance and validation?
The pharma industry is driven by strict regulatory requirements. Stringent validation processes must assure that all process steps work as designed. In a way, this acts as a barrier against new technology.
Take the example of a packaging line: one order may require two drums of tablets, four boxes of blister packs, four boxes of secondary packaging, a box of inserts and a box of outer cartons. These materials are traditionally collected from the warehouse by hand, placed on one pallet and then taken to production. Larger companies may use automatic storage and bring the products to a goods-to-person workplace, but the human still does the actual picking.
The order preparation process is likely set out in the company’s Standard Operating Procedures (SOPs), and any IT systems and documentation involved have been tested during the validation process.
To completely change this process by replacing the human with a robot would require a new, possibly long, difficult and costly validation process. Using only robots here excludes human supervision and invalidates the use of the established SOPs.
But what if the robot and a human could work together?
Perhaps the robot could pick and place the boxes with the secondary packaging and the outer cartons. At the same time, the human picks and places the more odd-shaped drums of tablets and the blister packs. The human operator oversees the work of the robot, performing regular checks during and after the process. The worker is still following the established SOP but has a helping hand.
Without wanting to dent our human pride too much, the results should overcome some of our own frailties and be improved. The duty is still on the human partner to ultimately act as validator, in much the same way that self-driving cars can still fit in the established frameworks of legislation and accountability by still requiring a human driver behind the wheel.
Depending on the outcome of risk analysis, and the views of quality officers and inspecting agencies, the relative benefit to validation processes will ultimately be determined by ourselves.
My guess is that as more real life examples are being introduced, each going through the full validation process as they are implemented, experience will tell us if in this collaborative model we can still trust the established manual SOPs. Maybe one day allowing us to take a back seat, so long as we know the steering wheel is still within reach.
I am sure the prospect of human-robot collaboration intrigues many. The technology exists, and in case you want to see an example, just look at this video of a collaborative example in logistics.