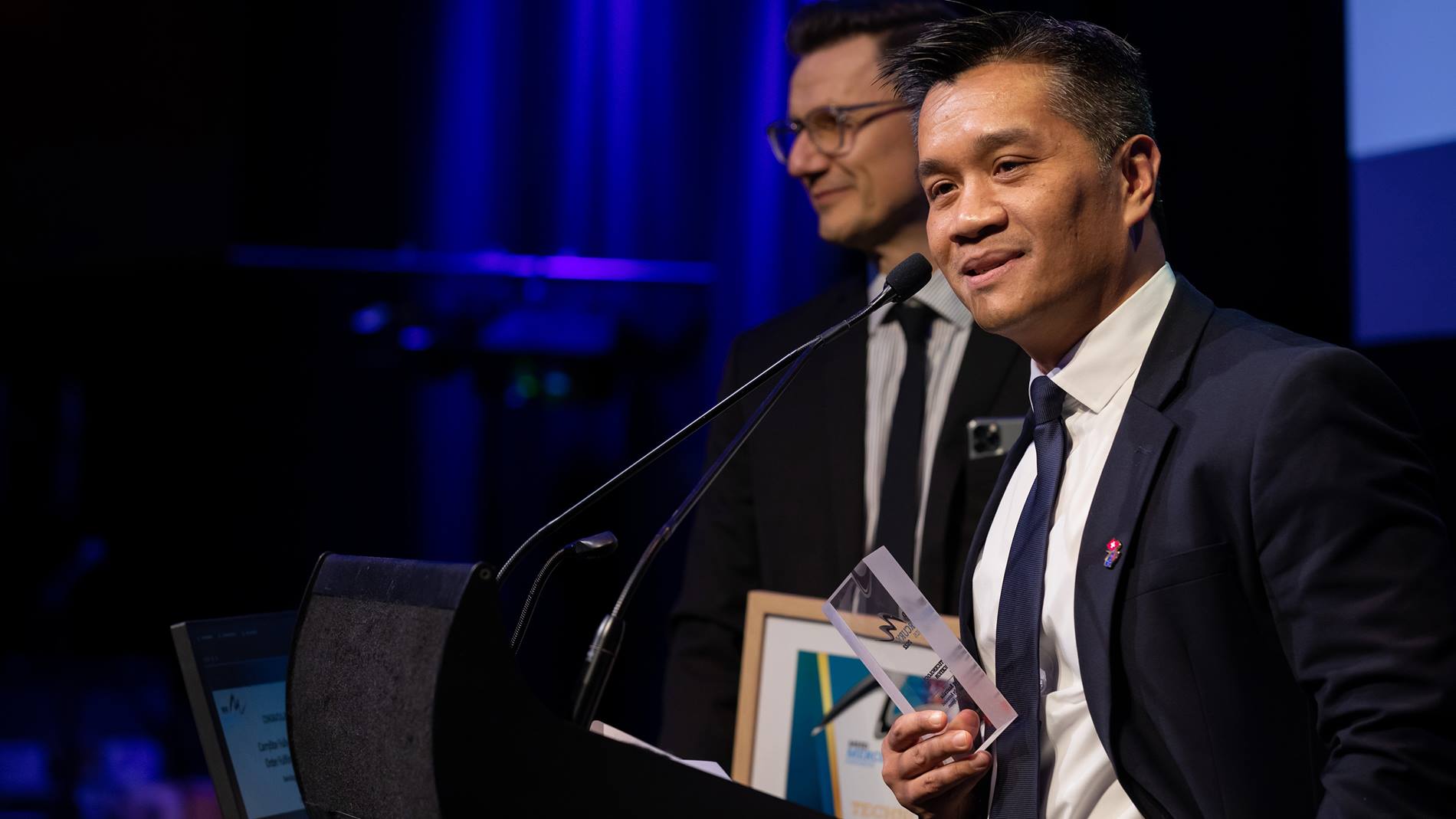
Swisslog’s innovative warehouse automation technology wins materials handling Mercury award
Swisslog’s innovative automated warehouse technology has won the “Best Technology Application” award at the 2022 MHD Materials Handling Mercury Awards
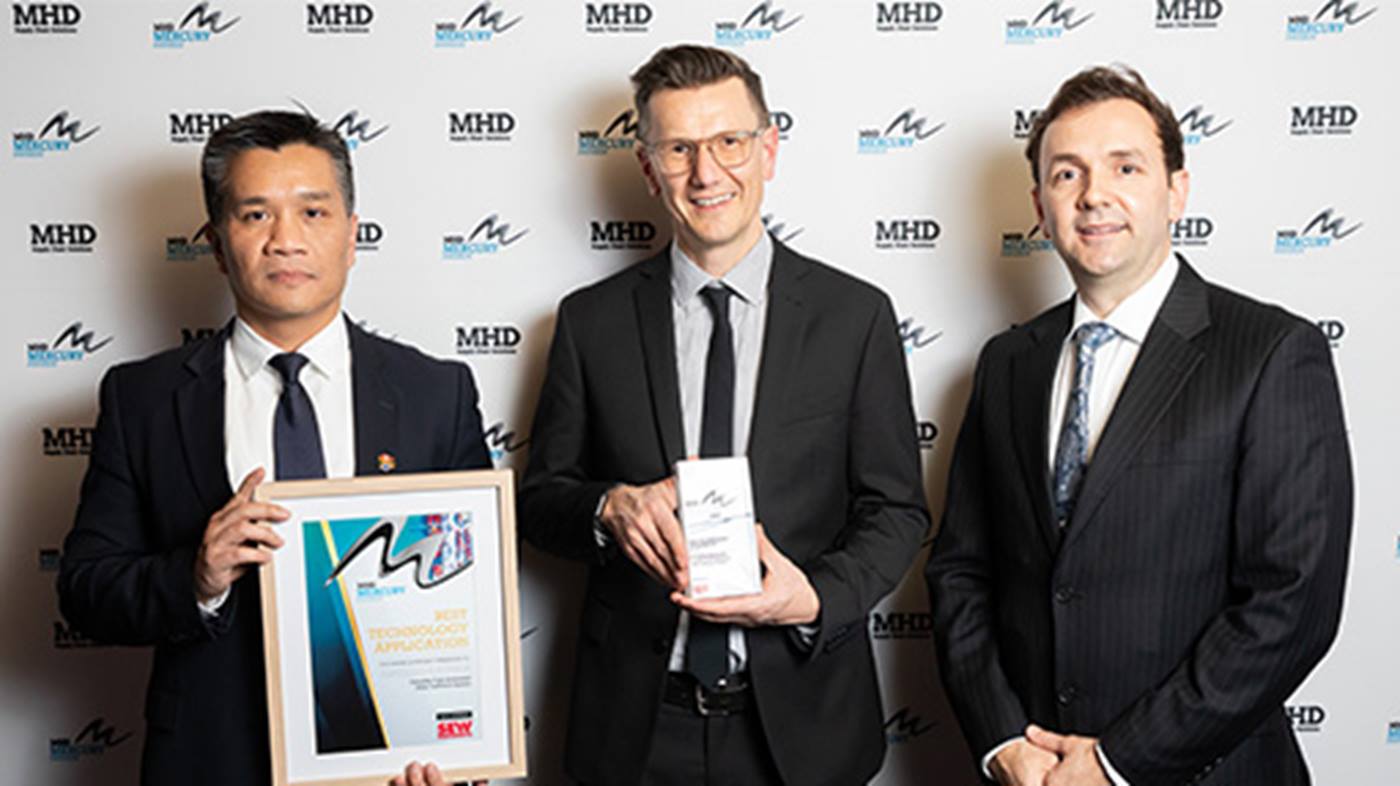
The technology that received the accolades in the award presentation in Melbourne involved Automatic Mobile Robots (AMRs), KUKA Robots, and the latest Swisslog SynQ Warehouse Management Software (WMS), which combined to deliver optimum efficiency, flexibility, reliability, and sustainability for order fulfilment.
“It’s a great honour to be recognised in the materials handling and supply chain industries, for our innovative solutions that are helping customers locally and globally,” said Dan Ulmamei, Managing Director, Swisslog Australia and New Zealand (ANZ).
“Globally, the industry is experiencing a range of new challenges, and it is through innovation, problem-solving, and collaboration, that we will be able to overcome these challenges together,” he said.
The technology involved in the award win complements Swisslog’s comprehensive range of warehouse automation and intralogistics solutions, including automatic storage and retrieval systems (ASRS), transport and conveyors, picking and palletising, and automation software.
The scalable and modular solution that won the Mercury Award was a fully-automated solution suitable for small, mid-size and large layer and stack picking operations. With minimal fixed infrastructure required, and the ability to grow as a business expands its operations, the innovative solution is ideally suited to food and beverage, grocery, FMCG, and pharmaceutical companies looking for a cost-effective, hygienic and efficient warehouse automation solution.
The solution from Swisslog also enhances productivity and sustainability through negative picking, which allows for the conversion of source pallets into order pallets to minimise wastage. The entire system is driven by Swisslog’s intelligent SynQ software, which not only manages the system, but collects valuable data and uses this to recommend further efficiencies.
“I’d like to thank the dedicated ANZ team for all their hard work in developing new solutions tailored to our customers’ needs,” said Dan.