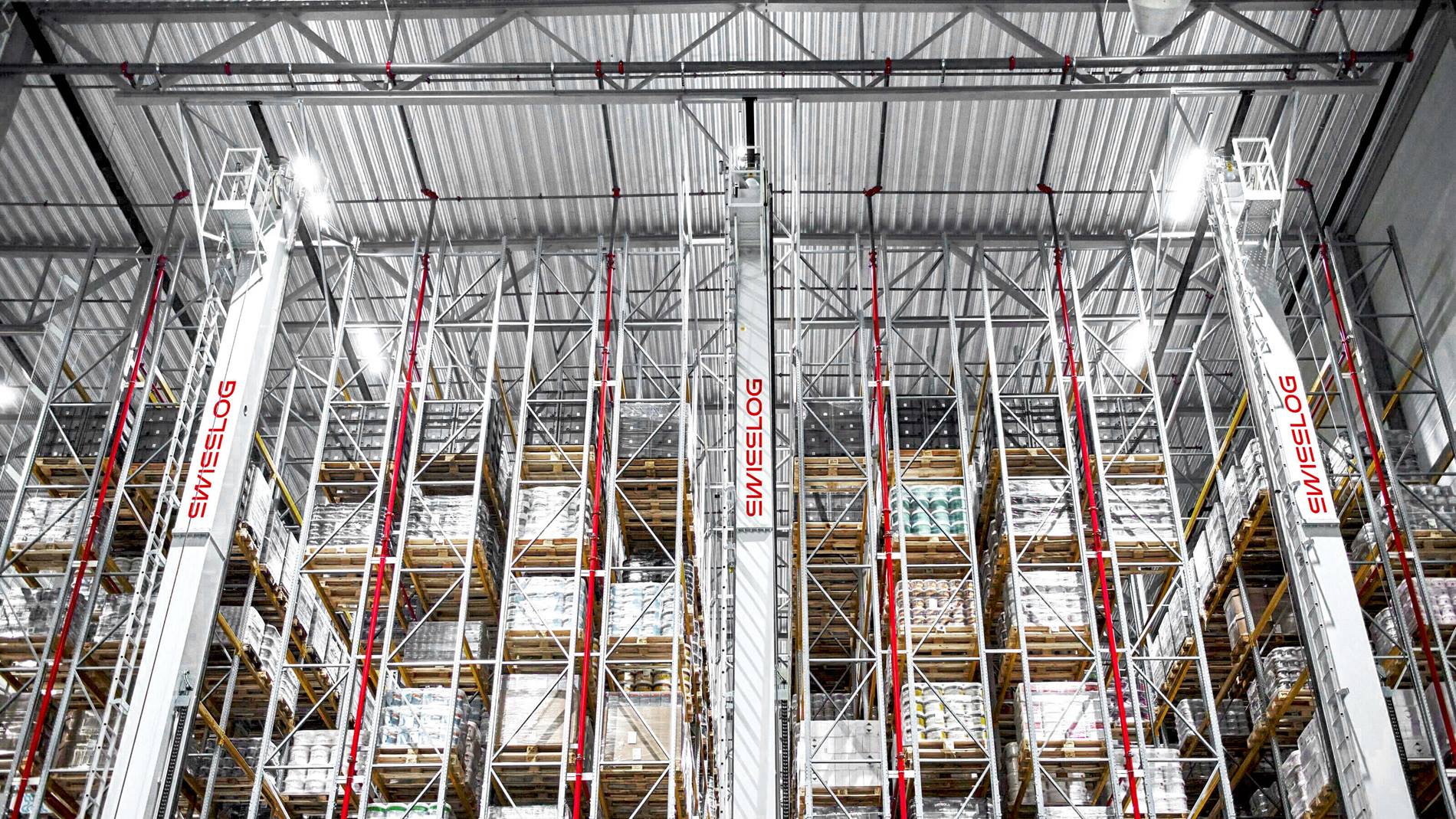
Three Ways ASRS Stacker Cranes Are Reducing Warehouse Energy Costs
5 September, 2019
This year marks the 50th anniversary of Swisslog’s Vectura stacker crane. In a previous post we outlined the story of how a manual crane evolved to become a top-selling ASRS solution.
In this post, we’ll focus on the innovations that have occurred during that evolution that have enabled greater energy efficiency in warehouses that rely on Vectura stacker cranes.
Energy costs associated with automation are more than offset by labor savings. Still, in today’s competitive market, warehouse operators look for savings wherever they can find them. As labor costs decrease, energy represents a higher percentage of total warehouse costs, particularly in cold storage facilities where energy represents the number two cost behind only labor. Often, energy savings translate directly into improved operating margins for warehouse operators.
Vectura has been continually refined to reduce overall energy consumption. Three developments in particular have contributed to Vectura’s outstanding efficiency today:
- Lighter Weight: Innovations in Vectura’s mast design, along with other enhancements that reduced weight, have cut the crane’s energy consumption by up to 20% compared to other pallet cranes. These reductions were accomplished without compromising strength, reach height or reliability. Vectura cranes operate at heights of up to 45 meters and are capable of handling large and unusual loads from car bodies to boats.
- Regenerative Energy: Vectura cranes can capture energy generated from the vertical axis downward motion of the crane’s carriage and redirect this energy to offset the energy draw from the horizontal motion of the crane and vice versa. This regenerative energy capability reduces total energy draw by up to 20%.
- Integrated Energy Management: Sophisticated energy management controls link the energy performance of the Vectura crane to the system’s actual real-time energy needs to share a power budget. This allows the crane’s controllers to continually look ahead and communicate what amount of energy each system and axis is producing or using. The controllers can then coordinate and optimize the sharing of harvested power from one system or axis to another or to the grid. They can also coordinate the delay and start functions of associated systems to optimize the use of harvested energy and all cranes can be controlled to minimize peaks in power draw caused by simultaneous machine starts.
In addition to these technological advances, Vectura cranes have enabled a shift in how cold storage warehouses are designed. Because the square footage of the roof is a factor in the overall energy consumption of a cold storage facility, warehouse designers have used Vectura’s ability to support high-bay storage to design taller warehouses with reduced roof square footage. These facilities are less expensive to build and can result in a 10% to 15% decrease in electrical power draw in the refrigeration system, reducing both the initial cost of the system and ongoing operating costs.
From lighter weight designs to regenerative power to intelligent power management, Vectura helps you reduce energy costs while delivering the reliability and flexibility you need to manage inventory as efficiently as possible. For more information, visit the Vectura product page.