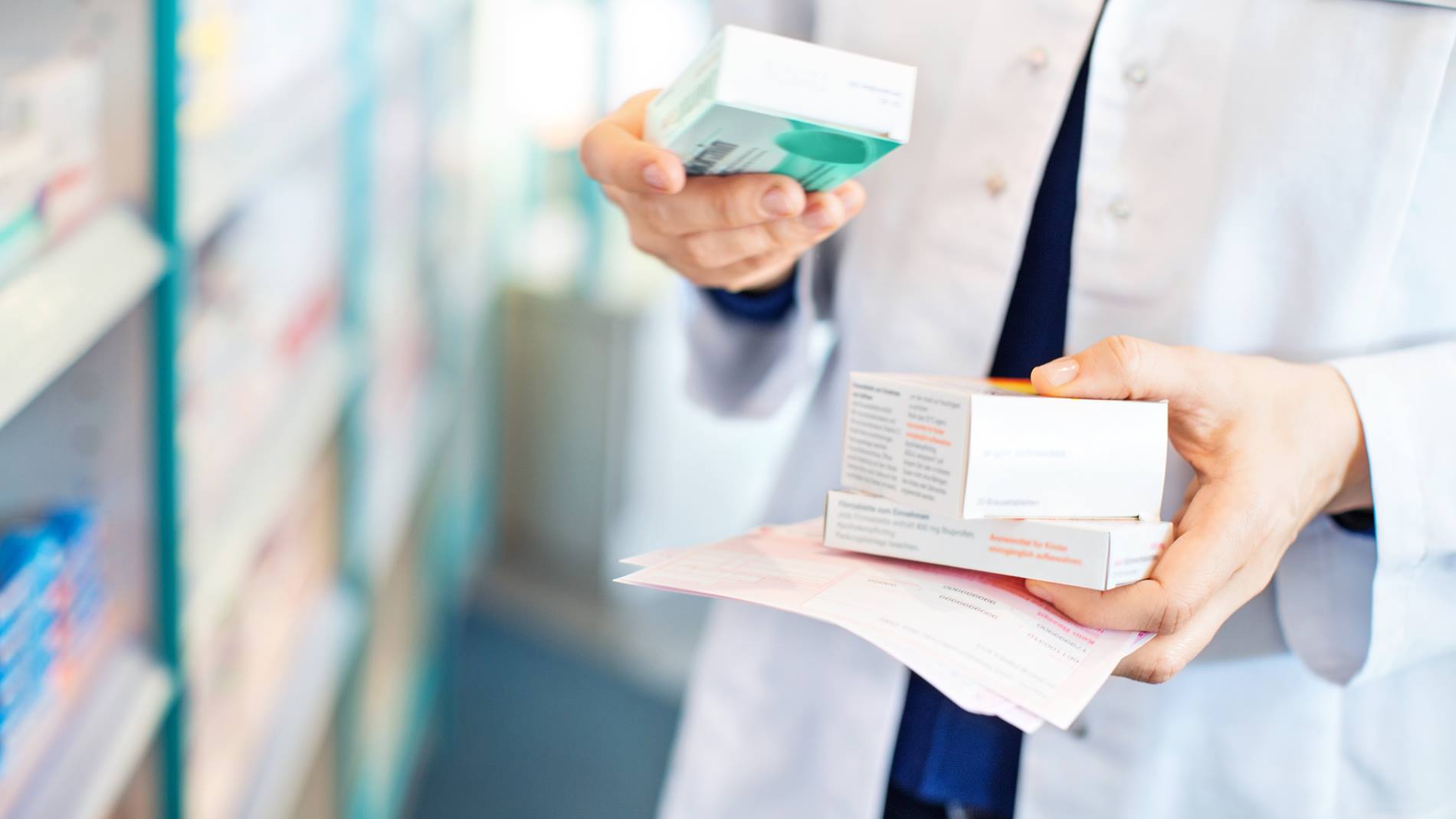
Serialization in the pharmaceutical industry: challenge and opportunity
22 December 2016
The pharmaceutical industry is on the right track. It continuously combats counterfeit drugs and theft by protecting them through serialization. But the assignment and control of serial numbers across the entire supply chain of finished products is difficult, especially in logistics and IT. Serialization does, however, have profitable side effects.
The pharmaceutical industry is on the right track in the continuing struggle to ward off counterfeit drugs. Experts believe that by the end of 2018 more than 40 countries will have enacted legislation to seamlessly track and trace each and every medical preparation. Serialization would then safeguard approximately 75 percent of the world’s prescription drugs against misuse.
Although it sounds so simple and advanced, serialization is difficult to execute – especially in logistics and IT. Yet what may seem like a necessary evil can protect you from potential damaging risks.
The FDA1 (Food and Drug Administration) estimates that globally more than 10 percent of all medications are counterfeit. According to experts from the World Health Organization (WHO), as many as 50 percent of medications sold over the Internet are imitations2. Counterfeit products are a major international problem, which is why it is high time that security systems in the global health care system be drastically tightened – not only for the safety of the patient, but also to financially protect the manufacturers and distributors affected.
Producing, applying and securely processing vast quantities of data
The solution for preventing counterfeits is serialization: the assignment and control of serial numbers across the entire supply chain of finished products in the pharmaceutical market for the purpose of tracing every package sold – from the drug manufacturer to the end consumer. Consequently, every company and institution along the way is confronted with generating, applying and securely processing vast quantities of data. This procedure is a major challenge, both locally and globally.Varying processes from country to country
Existing laws make the process different from country to country. Requirements dictating the type of coding on a package differ. Some countries require a 2D or linear code, others a GTIN (Global Trade Identification Number), and still others an NTIN (National Trade Item Number). Standardization organizations include GS1, EDMC in China, and IUM in Brazil, to name just a few. GS1 is working towards standardizing codes by appending a serial number (S/N) to the Global Trade Identification Number: GTIN + S/N = unique identification packaging unit plus 2D barcode. In this system, only the combination of the product number and serial number have to be unique. The serial numbers alone can be used for different products.For its part, China decided on a 1D instead of a 2D barcode. Even the European Union is going its own way, specifying in EU Directive 2011/62/EU (Falsified Medicines Directive) the introduction of coded packages with a unique serial number for nearly all prescription medications.
Seamless tracking and tracing
The issuer of the serial number can be a company, or in the case of China, Argentina, and Turkey, the government or a central, government-authorized institution. Serial numbers themselves are generated either randomly or serially, and depending on where you are in the world, must be archived for the duration of one to six years after the medication’s expiration date. Notwithstanding all the country-specific differences, market participants are required by law to store serial numbers, append information each time the package changes hands or location, and seamlessly document its route until the medication is received by the patient. This begins with the packaging process and the subsequent storage and transport process, and extends from the drug manufacturer via the wholesaler to the physician, the pharmacy, or the hospital. Data is stored in a central database, except in the USA where the data “travels” with the product.Major accomplishment for any material flow expert
End-to-end track & trace is a major accomplishment for any material flow expert and requires powerful software and massive storage capacity in addition to extensive system knowledge.Serialization in the pharmaceutical industry also means close interaction with government institutions and all sales partners. It is embedded in the quality assurance processes of the production workflows and environment for the manufacture of medications and active ingredients and therefore complies with Good Manufacturing Practices (GMP). It also follows Good Storage Practices (GSP) and Good Distribution Practices (GDP), combined in China into Good Supply Practices. Regardless of how “GxP” is defined, logistics providers and IT professionals must be well-versed in these requirements and provide warehouse management platforms that support the required data collection and processing – differentiated according to target-country requirements for the end product.Product marking in the packaging process
In the packaging process, serialization begins with marking each and every sales package with a unique identifier. If the sales packages are combined in a larger container, such as a case or a pallet, these secondary packages must also have serial numbers. Marking follows the parent-child principle, creating a hierarchical relationship between a larger outer unit and all the units contained within it.Adapting IT systems in the supply chain
Tracking this marking information has a major impact on the supply chain process. Typically, the ERP system will not capture serial numbers, but it will continue to manage product information and batches. Nonetheless, IT systems and interfaces as well as hardware and software are affected by modifications, which does increase the complexity of material flows in production and the warehouse. A serialization manager is used as a software interface between the ERP and warehouse management system. A warehouse management system aligned with the new requirements can execute, control, and monitor the data collection process at every level. Suppliers who specialize in integrated intralogistics solutions for the pharmaceutical sector are able to evaluate all this data in real time and use condition monitoring to analyze trends with a view toward optimizing future workflows and boosting system efficiency. These functionalities are all part of the modern era of Industry 4.0.Very few countries well-prepared
Serialization takes a lot of work, and very few countries that have pledged to combat counterfeit medications are prepared to meet the challenge. Turkey has fully completed the introduction. China and Korea are well on their way, although there is still much to do in the rest of the world.
Big Data can protect you from risks
Serialization requires modifying processes and, at first glance, puts a strain on the value-creation chain in the pharmaceutical sector. On closer examination, however, several other benefits emerge that make good business sense besides vitally improving drug safety. The new process therefore helps not only to verify regulatory compliance, it also boosts brand reputation and delivery accuracy. Product recalls can be optimized. Inventory control is tightened. In addition, there is another positive side effect of which market participants are often unaware: The collection, reconciliation, and archiving of countless millions of pieces of data associated with serialization generates “big data”: a treasure trove for precise analyses and improvements in the flow of goods. Serialization, therefore, is anything but a necessary evil, it harbors the potential for profit.