CycloneCarrier: Dynamic shuttle storage and retrieval system for small loads
Do you need a storage system for small loads with high throughput and storage capacity? CycloneCarrier helps you store small loads fast and efficiently.
Efficient storage, fast picking and order consolidation
CycloneCarrier is an automated shuttle system for storage of small loads. The shuttle system is designed for applications where high throughput and excellent availability are essential, for example in Retail & E-commerce for returns handling, replenishment or buffer for order consolidation. The shuttle offers double to quadruple deep storage of totes, trays and cartons. CycloneCarrier is suitable for deep-freeze storage environments. To reduce the number of aisles, the shuttle can be built up to 150 m long and 25 m high. Vehicles are available in two versions with load handling devices in either fixed or adjustable width to handle different product sizes.
A double-deck lift with two conveyor decks is available for applications that require the highest performance.
The shuttle can be used as a feeding engine for goods-to-person pick stations, a buffer system for order consolidation, or an intelligently designed combination of both. It forms the storage system for our automated case picking solution ACPaQ and can also be combined with our ItemPiQ robotic application to increase throughput even more.
Why go with Swisslog’s dynamic shuttle system CycloneCarrier?
- Shuttle with plug and play functionality reduces implementation time during operation, service and extension.
- Seamless integration into other subsystems, thanks to predefined standards, operating realization time and costs.
- Durable wear parts minimize running costs.
- Reduced failures thanks to a sophisticated load handling device. Clearance between cartons in depth is checked and telescopic arms can be adjusted independently, if necessary, to safely pick up cartons that are damaged or have moved out of position.
- Quick and easy access to the aisles for maintenance.
- Ability to shut down aisles by maintenance levels increases system uptime.
- CycloneCarrier’s standard software module gives access to a number of business intelligence tools that help optimize the shuttle’s performance.
- Future-proof: Increase performance by easily switching from a goods-to-person to a goods-to-robot system.
Imagine if you could increase throughput?That is exactly what Alnatura did.
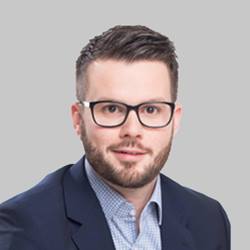
Swisslog has thoroughly planned our logistics center and implemented it quickly and reliably.
Learn in our complete case study why Alnatura chose CycloneCarrier.