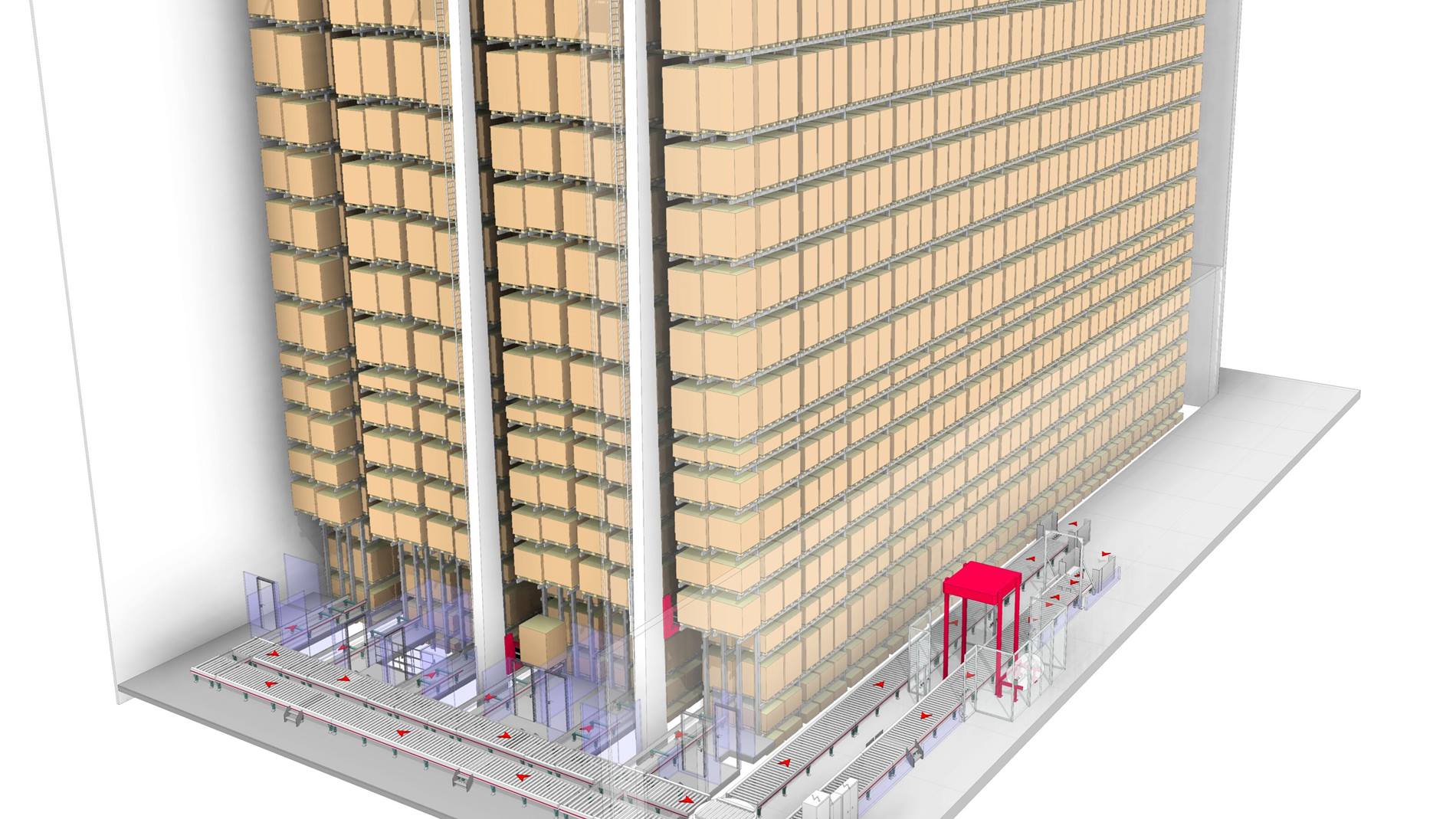
Die Herausforderungen bei automatischen Palettenlagern
Automatisierte Palettenlager werden zunehmend eingesetzt, um die Effizienz und Genauigkeit von Lagern zu verbessern. Die Integration von Paletten in diese Systeme kann in Branchen von der Pharma- bis zur Lebensmittelindustrie erhebliche Herausforderungen mit sich bringen.
- Anpassung an Änderungen der Palettengrößen
- Verstellbare Palettenstapler und Handhabungssysteme
- Handhabungssysteme für gemischte Paletten
- Betriebsprozess
- Plattformstapler vs. Stand-in-Stapler
- Plattformstapler
- Stand-in-Stapler
- Die Hauptunterschiede zwischen Stand-in- und Plattformstaplern
- Palettenkompatibilität und Konsistenz
- Branchenspezifische Probleme: Herausforderungen in Bezug auf Temperatur und Material
- Gemischte Paletten und Herausforderungen bei der Lastpositionierung
- Langlebigkeit von Paletten und Sicherheit am Arbeitsplatz
- Verbesserung der Sicherheit und Hygiene am Arbeitsplatz
1 Anpassung an Änderungen der Palettengrößen
Eine der größten Herausforderungen in AS/RS-Lagern ist die Anpassung an veränderte Palettengrößen. Dies ist von entscheidender Bedeutung für Branchen, die mit unterschiedlichen Produkten umgehen oder in dynamischen Märkten tätig sind, wie z. B. die Lebensmittelindustrie, in der sich die Produktlinien häufig ändern. In automatischen Palettenlagern können flexible Automatisierungssysteme eingesetzt werden, darunter verstellbare Palettenstapler und Handhabungssysteme, die sich an unterschiedliche Palettengrößen anpassen lassen.
1.1 Verstellbare Palettenstapler und Handhabungssysteme
Verstellbare Stapler und Handhabungssysteme für gemischte Ladungsträger in automatisierten Hochregallagern bieten flexible Lösungen für die effiziente Ein- und Auslagerung unterschiedlichster Waren.
- Die Teleskopgabeln können aus- und eingefahren werden, um unterschiedliche Palettentiefen aufzunehmen. Dadurch sind sowohl einlagige also auch doppeltiefe Lagerkonfigurationen möglich.
- Variable Gabelverstellung ermöglicht die Anpassung der Gabelbreite an unterschiedliche Palettengrößen und erhöht so die Flexibilität im Lagerbetrieb.
- Sensoren und Wägezellen werden zur Erkennung von Palettenabmessungen und -gewicht eingesetzt, um eine sachgerechte Handhabung und Lagerung zu gewährleisten.
1.2 Handhabungssysteme für gemischte Paletten
Um gemischte Paletten in einem automatisierten Palettenlager effizient zu verwalten, werden verschiedene Technologien und Ansätze eingesetzt:
Intelligente Lastprofilerstellung: Moderne Sensoren und Kameras scannen eingehende Paletten, um ihre Abmessungen, ihr Gewicht und ihre Lastverteilung zu ermitteln. Diese Daten werden zur Optimierung von Lagerplätzen und Handhabungsverfahren verwendet.
- Dynamisches Lagerplatzzuweisung: Das Lagerverwaltungssystem (WMS) nutzt Echtzeitdaten, um auf der Grundlage von Paletteneigenschaften und Auslagerungshäufigkeit optimale Lagerplätze zuzuweisen. Dies maximiert die Raumnutzung und verbessert die Effizienz der Auslagerung.
- Mehrtiefe Lagerung: Die Systeme können einfachtiefe, doppelttiefe oder sogar mehrfachtiefe Lageroptionen enthalten, um die Raumnutzung für verschiedene Palettentypen zu optimieren.
- Automatisierte Laststabilisierung: Für instabile oder unregelmäßig geformte Lasten können automatische Wickel- oder Umreifungsstationen in das System integriert werden.
- Flexible Entnahmesysteme: Regalbediengeräte können mit verschiedenen Lastaufnahmemitteln wie Teleskopgabeln, Paletten Shuttles oder bordeigenen Förderern ausgestattet werden, um unterschiedliche Palettentypen und Lagertiefen aufzunehmen.
1.3 Betriebsprozess
Der Betriebsprozess in einem automatischen Palettenlager beginnt mit der Einlagerung von Mischpaletten in das System. Bei der Einlagerung wird jede Palette gescannt, um eine genaue Identifizierung und Profilierung zu gewährleisten. Dieser erste Schritt ist entscheidend für die Bestimmung der Merkmale der Palette, wie z. B. Abmessungen, Gewicht und Inhalt, die dann zur Optimierung der späteren Handhabung verwendet werden.
Nach der Identifizierung weist das Lagerverwaltungssystem (WMS) die Palette einem optimalen Lagerplatz innerhalb der Einrichtung zu. Diese Zuordnung basiert auf einer Kombination aus den Merkmalen der Palette und vordefinierten Systemparametern wie Lagerdichte und Auslagerungspriorität, um sicherzustellen, dass die Palette so effizient wie möglich gelagert wird.
Die Palette wird dann von Regalbediengeräten oder anderen automatisierten Fahrzeugen an ihren vorgesehenen Lagerort transportiert. Diese Fahrzeuge sind speziell dafür ausgelegt, sich in der Lagerumgebung zurechtzufinden und die Palette mit Hilfe von präzisen, auf die spezifischen Anforderungen der Palette zugeschnittenen Handhabungsmechanismen an dem ihr zugewiesenen Platz zu platzieren.
Wenn eine Auslagerung erforderlich ist, ortet das System die Palette und wendet das geeignete Handhabungsverfahren an, das möglicherweise Anpassungen auf der Grundlage der zuvor gespeicherten Daten über die Palette beinhaltet. Auf diese Weise wird sichergestellt, dass der Auslagerungsprozess sowohl effizient als auch präzise ist und das Risiko von Fehlern oder Beschädigungen minimiert wird.
Abschließend werden die ausgelagerten Paletten je nach Bedarf an die Kommissionierstationen oder Ausgangsverarbeitungsbereiche geliefert. Dieser Schritt der Ausgangsverarbeitung stellt sicher, dass die Paletten für die weitere Verteilung oder Verwendung bereit sind, und fügt sich nahtlos in den gesamten Logistikbetrieb ein.
1.4 Plattformstapler vs. Stand-in-Stapler
Bei beiden handelt es sich um motorisierte Paletten-Handhabungsgeräte, die jedoch einige wichtige Unterschiede aufweisen:
1.4.1 Plattformstapler
Plattformstapler sind vielseitige Maschinen mit einer klappbaren Plattform an der Rückseite, auf der der Bediener steht. Diese Konstruktion bietet die Flexibilität, sowohl im Mitgänger- als auch im Mitfahrmodus zu arbeiten. Im Mitgängerbetrieb können die Plattform und die Seitenstangen hochgeklappt werden, so dass sie sich auch in engen Räumen leicht bewegen lassen. Im Mitfahrbetrieb bieten diese Stapler in der Regel höhere Fahrgeschwindigkeiten als Mitgängerstapler und eignen sich daher gut für längere und häufigere Pendelfahrten. Während Plattformstapler wendiger sind als Stand-in-Modelle, sind sie etwas weniger kompakt als Deichselstapler. Ihre Bauweise und Geschwindigkeit tragen jedoch zu einer höheren Produktivität bei, insbesondere bei Transportaufgaben über mittlere Entfernungen.
1.4.2 Stand-in-Stapler
Bei Stand-in-Staplern ist der Bediener vollständig von der Struktur des Staplers umschlossen, was ein hohes Maß an Schutz während des Betriebs bietet. Diese geschlossene Bauweise erhöht nicht nur die Sicherheit, sondern trägt auch zur Gesamteffizienz der Maschine bei, so dass sie sich besonders gut für intensive Einsätze und Aufgaben eignet, bei denen längere Strecken zurückgelegt werden. Standstapler haben oft eine kompaktere Grundfläche, so dass sie auch in schmaleren Gängen eingesetzt werden können und eine höhere Lagerdichte im Lager erreichen. In Bezug auf die Leistung sind sie im Allgemeinen schneller und leistungsfähiger als Plattformstapler und bieten eine höhere Geschwindigkeit und Leistung für anspruchsvolle Aufgaben. Darüber hinaus sind diese Stapler mit Blick auf den Bedienerkomfort entwickelt worden, so dass sie sich ideal für längere Schichten und häufigere Einsätze eignen und so die Gesamtproduktivität und die Zufriedenheit der Bediener verbessern.
1.4.3 Die Hauptunterschiede zwischen Stand-in- und Plattformstaplern
Der Hauptunterschied zwischen Stand-in-Staplern und Plattformstaplern liegt in ihrer Konstruktion. Stand-in-Stapler umschließen den Bediener vollständig und bieten somit eine geschütztere Umgebung, während Plattformstapler eine offene Konstruktion mit optionalen Seitengittern für zusätzliche Sicherheit aufweisen. Dieser Unterschied in der Konstruktion hat erhebliche Auswirkungen auf die Raumeffizienz und die betriebliche Flexibilität.
Stand-in-Stapler ermöglichen in der Regel eine geringere Gangbreite, wodurch die Lagerdichte in einem Lager maximiert wird. Ihre kompakte Stellfläche und die geschlossene Position des Bedieners machen sie ideal für Umgebungen, in denen der Platz knapp ist. Im Gegensatz dazu bieten Plattformstapler eine größere betriebliche Flexibilität, da der Bediener je nach Situation zwischen Mitgänger- und Mitfahrbetrieb wechseln kann. Dies macht Plattformstapler besonders nützlich in Umgebungen, in denen die Fähigkeit, auf engem Raum zu manövrieren, entscheidend ist.
Wenn es um die Produktivität über lange Strecken geht, schneiden Stand-in-Stapler im Allgemeinen besser ab. Sie eignen sich besser für intensive Einsätze und längere Fahrstrecken, bieten höhere Geschwindigkeiten und einen besseren Fahrerkomfort. Die geschlossene Bauweise erhöht auch die Sicherheit, da sie den Bediener besser schützt, was ein sicheres und schnelleres Arbeiten ermöglicht, insbesondere in engen Gängen.
Bei der Wahl zwischen Stand-in- und Plattformstaplern sind Faktoren wie typische Fahrstrecken, Häufigkeit der Nutzung, Gangbreiten und der Bedarf an betrieblicher Flexibilität in ihrer spezifischen Lagerumgebung zu berücksichtigen.
2 Palettenkompatibilität und Konsistenz
Die Sicherstellung der Kompatibilität und Konsistenz von Paletten ist ein weiteres wichtiges Anliegen für Paletten-Hochregallager (HRL). Herkömmlichen Holzpaletten mangelt es oft an der für automatisierte Systeme erforderlichen Präzision und Einheitlichkeit, was zu Problemen wie System-Ungenauigkeiten, Gerätefehlfunktionen und möglichen Ausfallzeiten führt. Besonders akut ist dieses Problem in der Lebensmittelindustrie, bei der selbst geringfügige Abweichungen bei den Palettenabmessungen zu erheblichen Störungen führen können, insbesondere in Umgebungen, in denen ein hoher Durchsatz erforderlich ist.
Um diese Probleme zu entschärfen, gehen viele automatisierte Palettenlager dazu über, technische Kunststoffpaletten zu verwenden, die mehr Zuverlässigkeit und Konsistenz bieten. In Branchen wie der Pharmaindustrie, in denen aufgrund strenger gesetzlicher Vorschriften mehr auf dem Spiel steht, ist die Verwendung konsistenter, hochwertiger Paletten nicht verhandelbar.
3 Branchenspezifische Probleme: Herausforderungen in Bezug auf Temperatur und Material
Temperaturkontrollierte Umgebungen, wie z. B. Kühllager, die häufig in der Lebensmittel- und Pharmaindustrie verwendet werden, stellen besondere Anforderungen an Paletten. Holzpaletten zum Beispiel neigen dazu, Feuchtigkeit zu absorbieren und bei Minusgraden spröde zu werden, was zu Bruch oder Verformung führt. Dies beeinträchtigt nicht nur die strukturelle Integrität der Paletten, sondern birgt auch Risiken für die gelagerten Produkte.
Im Gegensatz dazu bieten Kunststoffpaletten aufgrund ihrer Widerstandsfähigkeit gegenüber Feuchtigkeit und Temperaturschwankungen eine bessere Leistung in solchen Umgebungen. Die Wahl des Palettenmaterials bleibt beim automatischen Palettenlager entscheidend. Kunststoffpaletten bieten zwar Konsistenz und Langlebigkeit, sind jedoch mit höheren Anschaffungskosten verbunden, was für Branchen mit knappen Gewinnmargen ein wichtiger Faktor sein kann.
4 Gemischte Paletten und Herausforderungen bei der Lastpositionierung
Gemischte Paletten, bei denen verschiedene Produkt- oder Palettentypen innerhalb desselben Systems verwendet werden, können für automatisierte Palettenlager eine besondere Herausforderung darstellen. Eine präzise Lastpositionierung ist in automatisierten Systemen unerlässlich, und jede Abweichung in den Palettenabmessungen oder -qualitäten kann zu Fehlausrichtungen und Betriebsstörungen führen. Dies ist besonders problematisch in Systemen mit tiefen Gassen, bei der die Qualität der Paletten für die Systemfunktionalität entscheidend ist.
In Branchen wie der Pharmaindustrie, in denen unterschiedliche Produktchargen unterschiedliche Handhabungsverfahren erfordern, kann die Verwendung gemischter Paletten den Lagerbetrieb erschweren. Um diese Herausforderungen zu bewältigen, verwenden einige Lagerhäuser speziell für AS/RS-Umgebungen entwickelte Kunststoffpaletten, die eine gleichbleibende Leistung gewährleisten und das Risiko von Systemausfällen verringern.
5 Langlebigkeit von Paletten und Sicherheit am Arbeitsplatz
Die Langlebigkeit von Paletten ist ein wichtiger Faktor in automatisierten Lagern, insbesondere in Branchen mit hohen Anforderungen an die Handhabung. Holzpaletten sind zwar traditionell, aber sie sind feuchtigkeitsempfindlich, schädlingsanfällig und weisen strukturelle Schwächen auf, was sie weniger haltbar und zuverlässig macht. Diese Probleme sind besonders in der Lebensmittelindustrie von Bedeutung, wo die Haltbarkeit der Paletten einen direkten Einfluss auf die Produktsicherheit und -qualität hat.
Kunststoffpaletten hingegen bieten erhebliche Vorteile in Bezug auf Feuchtigkeitsresistenz, Chemikalienbeständigkeit und Schlagfestigkeit, was sie zu einer langlebigeren Option macht. Ihre Langlebigkeit, die oft mehr als 10 Jahre beträgt, macht sie auf Dauer auch zu einer kosteneffizienten Wahl. In Branchen wie der Pharmaindustrie, in denen die Aufrechterhaltung einer sterilen und sicheren Umgebung von entscheidender Bedeutung ist, sind die Vorteile von Kunststoffpaletten in Bezug auf Haltbarkeit und Hygiene besonders wertvoll.
6 Verbesserte Sicherheit und Hygiene am Arbeitsplatz
Kunststoffpaletten tragen auch zu einer verbesserten Sicherheit und Hygiene am Arbeitsplatz bei, was in Branchen wie der Lebensmittel- und Pharmaindustrie von entscheidender Bedeutung ist. Im Gegensatz zu Holzpaletten sind Kunststoffpaletten frei von Gefahrenquellen wie Nägeln, Splittern und abgebrochenen Brettern, wodurch das Risiko von Arbeitsunfällen verringert wird. Ihr geringeres Gewicht und die glatteren Oberflächen minimieren das Risiko von Zerrungen, Verstauchungen und anderen Verletzungen und machen sie für die manuelle Handhabung sicherer.
Im Hinblick auf die Hygiene bieten Kunststoffpaletten aufgrund ihrer porenfreien Oberflächen, ihrer Resistenz gegen Bakterien und Schimmel sowie ihrer einfachen Reinigung und Desinfektion hervorragende Vorteile. Diese Eigenschaften sind besonders wichtig in pharmazeutischen und lebensmittelverarbeitenden Umgebungen, wo die Einhaltung hoher Hygienestandards entscheidend ist. Die Widerstandsfähigkeit von Kunststoffpaletten gegenüber Feuchtigkeit und chemischer Absorption verringert das Kontaminationsrisiko zusätzlich und gewährleistet, dass die Produkte sicher bleiben und den Branchenvorschriften entsprechen.
Die Integration von automatischen Palettenlager in die Intralogistik stellt zahlreiche Herausforderungen dar, die je nach Branche unterschiedlich sind. Während traditionell Holzpaletten verwendet wurden, setzt sich die Verwendung von Kunststoffpaletten aufgrund ihrer Langlebigkeit, Konsistenz und Hygienevorteile immer mehr durch. In Branchen wie der Pharma- und Lebensmittelindustrie, in denen in denen strenge Sicherheits- und Qualitätsstandards eingehalten werden müssen, sind Kunststoffpaletten aufgrund ihrer Vorteile die ideale Wahl. Mit der Weiterentwicklung der AS/RS-Technologien werden die Auswahl und das Management von Paletten ein entscheidender Faktor bei der Optimierung von Lagerabläufen und der Gewährleistung eines sicheren, effizienten Warenumschlags bleiben.