Busting the Myths that Keep SMBs from Automating Warehouse Processes
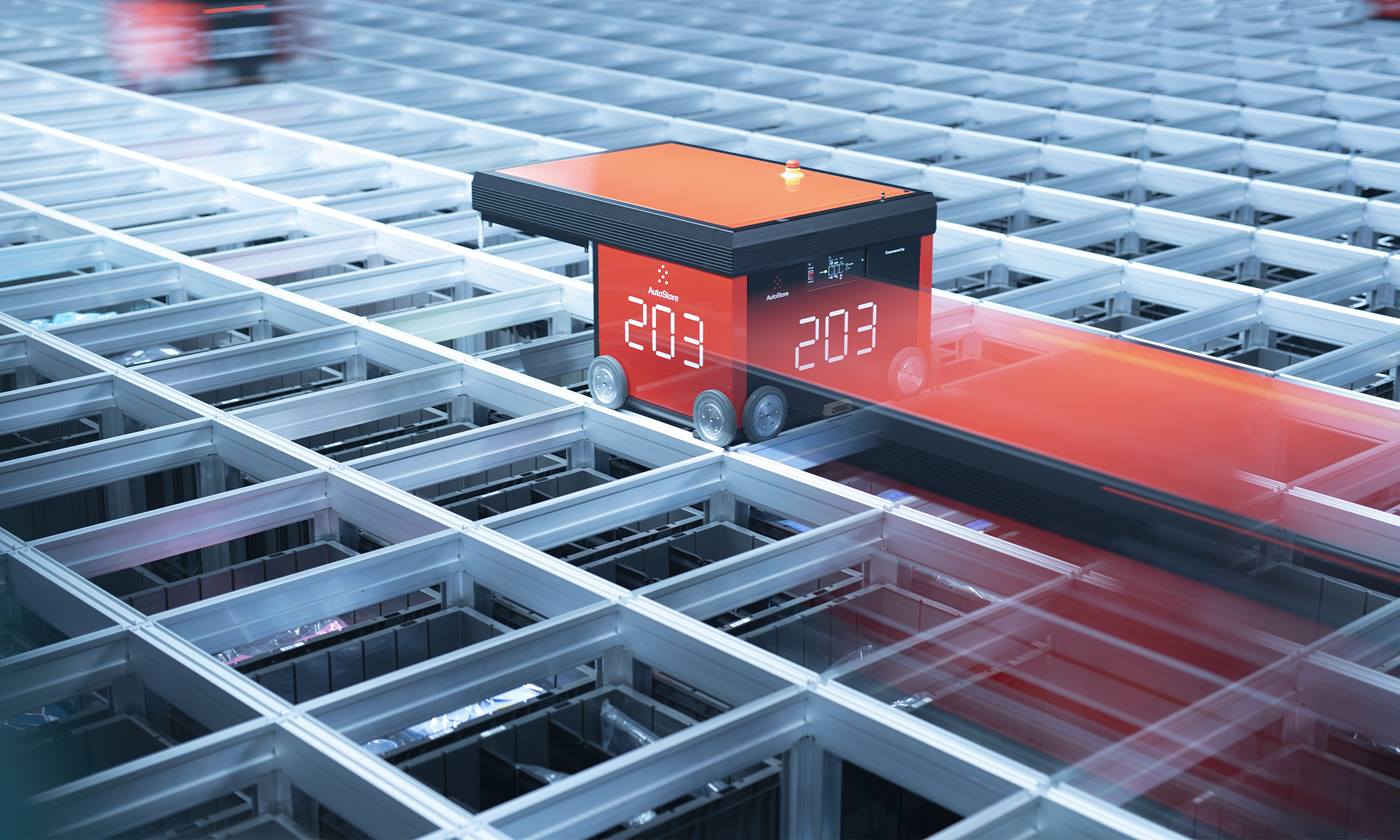
Goods-to-person automation technology has revolutionized item picking by allowing e-commerce companies to dramatically increase pick speeds, reduce their vulnerability to labor shortages, increase warehouse density and respond more efficiently to demand variability. Whether it is dealing with the extreme peaks associated with the holiday shopping season or the day-to-day and week-to-week variability that is common in e-commerce, today’s automation systems deliver the ability to scale throughput to demand while minimizing supplemental labor requirements.
They offer both greater flexibility and reliability than previous generation systems and that opens new opportunities for SMBs to level the playing field with larger competitors who have already automated. Yet, some SMBs are still being held back by automation “myths“ that persist in the market. Here are five that I’ve encountered and the truth behind the myth.
1. SMBs can’t afford to automate.
Some businesses may overestimate the financial commitment required to automate picking processes and the return on investment that can be achieved from that investment. The ROI for today’s automation systems is generally much shorter than for previous generation systems and today’s modular systems are available with financing options that allow capital constrained SMBs to convert capital costs to operating costs. They are also less disruptive to implement than previous generation systems and software has matured to the point where many applications can be supported with minimal customizations. Finally, when automation costs are balanced against the risk to a business if it cannot attract and retain the labor required to serve customers through manual processes, automation no longer becomes an option but a necessity.
2. Business uncertainty makes it difficult to commit to automation.
Nowadays every business struggles with the challenge of uncertainty around future sales, competition and economic conditions. The reality is that uncertainty is always present, and automation helps organizations deal with uncertainty by enabling consistently high productivity. No matter which way the economic winds blow, higher productivity improves responsiveness and leads to a better bottom line. Plus, modular automation systems like CarryPick and AutoStore have the flexibility to adapt to changing business conditions. Both systems can be easily expanded without shutting down operations to accommodate increased storage or throughput requirements. CarryPick even provides the flexibility to easily move the entire system to a new warehouse if the business outgrows their existing warehouse.
3. SMBs don’t have the resources to support automation.
Few organizations that implement automation have resources sitting idle that can be easily deployed to support automation. So, in this regard SMBs are in the same position as their larger competitors. Integrators like Swisslog remove much of the burden on internal resources by assuming responsibility for designing and installing automation based on a detailed analysis of data and application requirements. There are also a range of services available to reduce the demand on internal resources following startup. IT Managed Services, for example, can provide complete management of the IT systems required to support automation. Resident engineers can also be engaged to train internal resources and provide on-site support during the first year of operation. This array of services allows an SMB to focus on what they do best, leveraging their core competencies and converting other aspects of new systems to operating costs, temporarily or permanently.
4. SMBs aren’t equipped to maintain automation.
Automation vendors have taken significant steps to overcome this objection by minimizing single points of failure, improving system reliability and reducing the technical skills required to maintain systems. That focus has resulted in solutions like AutoStore that can achieve uptime rates of 99.6% to 99.8%. The system is also designed so that if any robot is taken offline, other robots automatically adapt to resume continuous operations. Basic maintenance on this system does not require specialized skills and can often be handled by regular warehouse personnel or shift supervisors.
5. Selecting the wrong technology could cripple the business.
There are a number of warehouse automation technologies available today—and more coming in the future—and this can be overwhelming for organizations considering automation. But it also allows the technology to be precisely matched to the application. At Swisslog, we support a broad range of warehouse technologies and take a technology agnostic approach to each deployment. That means beginning each engagement with the data and letting the data dictate system selection. Plus, with the inherent flexibility of today’s automation systems, picking the wrong technology is harder than ever!
Automation may not make sense for every business, but the size of the business shouldn’t be the determining factor. At Swisslog we’ve counseled large organizations against automation if the application wasn’t right and completed successful automation projects for a number of smaller businesses. If you’re looking to protect your business from future risk or position for growth, automation may be essential to achieving those goals. To find out if automation is right for your business, contact us.

Learn how Swisslog enables pharmaceutical manufacturers to use material handling automation to maximizes space utilization, minimizes product touches, and streamlines regulatory compliance.