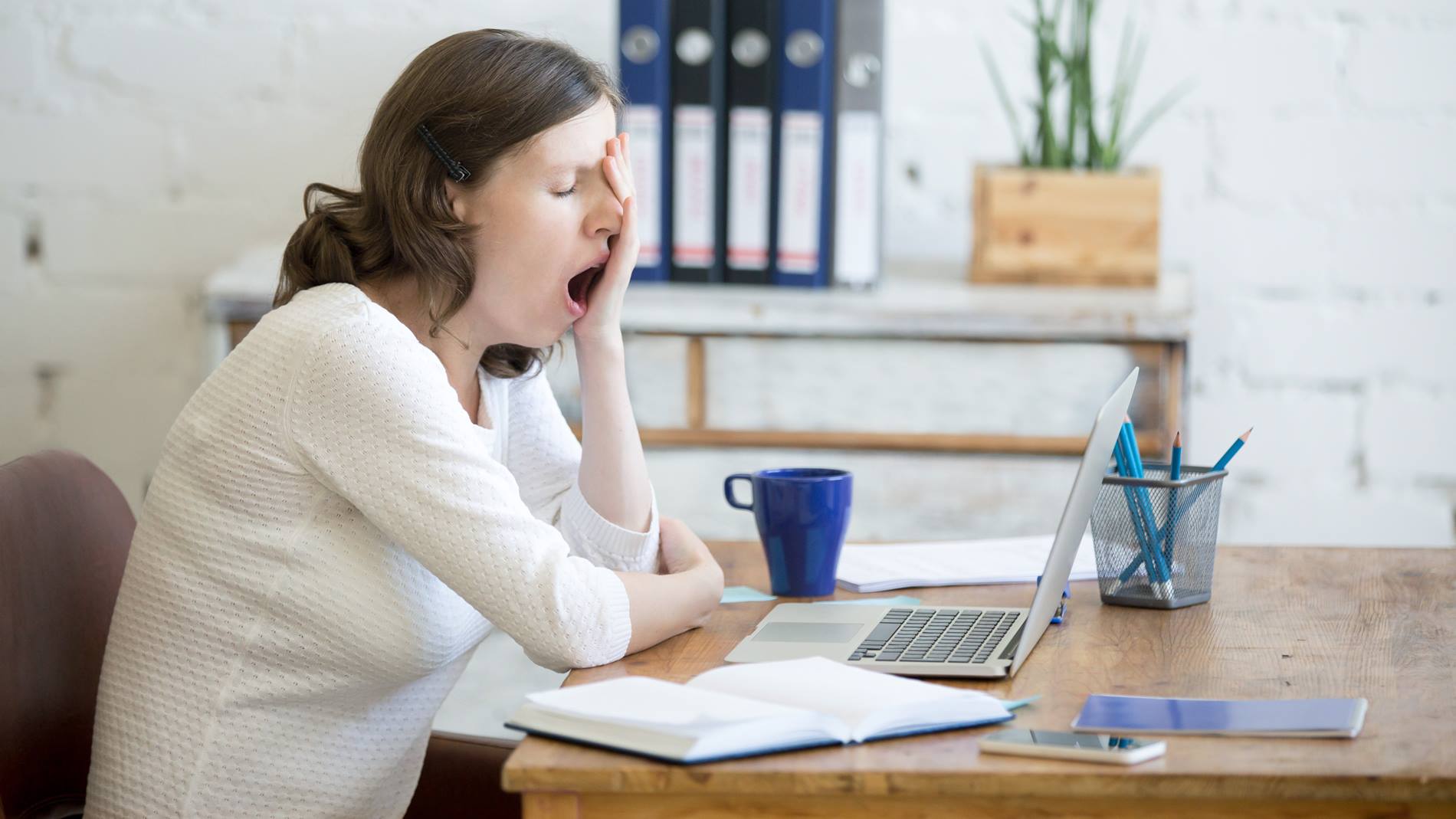
The Hidden Cost of Doing Nothing: Understand the Full Impact on Your DC
26 September, 2016
Companies carefully evaluate the often substantial costs associated with modernizing or optimizing an existing distribution center or building a new one. Yet they seldom scrutinize the real cost of the alternative – doing nothing.
Choosing to maintain the status quo is always an alternative to significant capital investment; however, the real expenses and the opportunity costs of doing nothing often are overlooked. Such costs need to be included in the business case for all proposed improvements to your distribution operation. The reason? The cost of inaction can easily exceed the price of a modernization project.
Followoing are three scenarios you should consider as you think about the right approach for your business.
Do Nothing, but End Up Spending More
This is the true, do-nothing scenario. No additional warehouse automation or software is purchased to update the distribution center. Business leaders tell their warehouse managers to make do with what they have, believing they are avoiding new expenses and capital investments.
While avoiding or delaying investment in operational improvements may seem like a prudent course of action, or more properly inaction, it may quickly result in increased costs to the business. Even for companies that are static or slow growers, they still must meet customers' demands and match or outperform competitors. Doing so introduces the possibility of these incremental operational costs:
- Pick faces are condensed to make room for new SKUs; coupled with increased demand for existing SKUs, replenishment activity and labor increase.
- Picking is more frequently interrupted due to insufficient stock in the pick face.
- Reserve inventory no longer fits in the pallet racks, so it is stored on docks, in aisles, in trailers and in outside storage; accessing the inventory becomes more challenging and labor intensive.
- There are insufficient pack stations and the packing function becomes a major constraint.
When doing nothing, other unanticipated costs can arise from lost revenue from missed delivery dates or inaccurate or damaged orders. In more extreme cases, the distribution center fails to meet customer service level agreements or expectations, and customers are lost forever.
Don't Invest in Automation, but Hire More Workers
Incremental operational costs are typically viewed as less expensive than capital investments. Unfortunately, businesses that choose to not invest in warehouse modernization, but purchase more of the same non-automated equipment, end up adding labor in an attempt to handle growth, proliferation of SKUs and new multichannel requirements. The cost of incrementally purchasing additional equipment, just to try to maintain current productivity levels, is often ignored. As a result, this tactic could lead to the following scenarios:
- Pick faces and an expanded pick zone are needed as SKUs increase.
- Racks must be purchased to store increasing inventory.
- Pack stations are required.
The problem with this approach is that if your business doesn't invest to update and expand distribution center capabilities, overall productivity usually decreases. Every time new SKUs are added, new pick locations are needed; and the size of the overall pick zone expands, which means employees must travel farther to retrieve items. More people are needed to make up for the additional pick time required as SKUs increase.
Adding labor costs into an existing warehouse rarely is the best solution. More pickers increase congestion and delays as workers and forklifts wait for each other. Pick times are slowed as a result.
Add Automation and Save Long Term
Businesses in growing industries frequently choose to meet demands for more SKUs and multi-channel fulfillment by improving their distribution process through automation. That's a significant new level of investment in material handling equipment and warehouse software.
When is the investment in automation justified? When businesses scale a warehouse to a certain point, they face new challenges:
- They miss orders, or quality degrades to the point that the whole process of getting orders right and shipped on time becomes increasingly challenging.
- Businesses try to pick more items in a smaller footprint.
- They add more workers, leading to congestion in the pick zone or other areas that slows workflow.
- Businesses must adjust to changing customer requirements, and the cost of doing nothing risks existing business or escalates penalties for noncompliance.
Summary
What's the benefit of doing nothing instead of investing to expand distribution capabilities? A company can save on capital costs today, of course, but it's critical to understand what doing nothing is likely to eventually cost your company in other expenses plus missed business opportunities.
Many companies are willing to increase operational costs to avoid capital investments - often out of an erroneous belief that companies that invest in material handling equipment and software gain little increase in productivity and suffer significant disruptions to operations.
Nevertheless, constraints on capital are real, especially at growing companies because they're buying inventory at increasing rates. They have to choose between investing in the infrastructure for manufacturing and/or the infrastructure for marketing and sales before they would ever invest in the infrastructure for distribution. Investment in distribution modernization also competes for funding with building construction and rental and operational expenses.
Given all of these challenges, decisions about capital investment for distribution are fully informed only when the cost of doing nothing in the warehouse is weighed against the cost to automate and modernize. Doing nothing brings with it significant hidden costs. You want to make sure you identify them and include them in every business case.