Warehouse Automation Evolves to Help Deal with Shifts in Demand from COVID-19
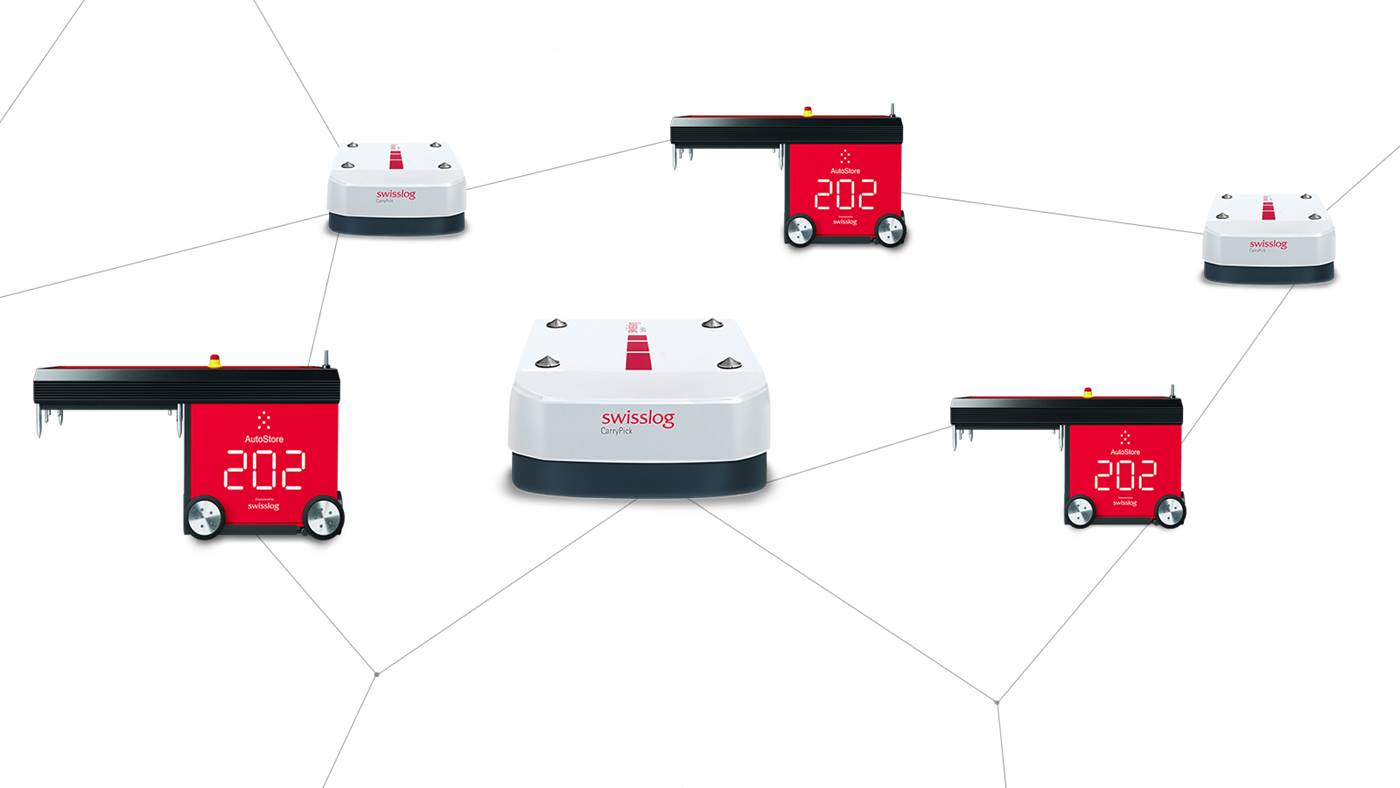
U.S. e-commerce sales grew from $169 billion in 2010 to $595.5 billion in 2019 and the pace of growth has yet to plateau. The 14.9% year-over-year growth rate between 2018 and 2019 was the second largest in the ten-year period.
And that was before the global pandemic spiked demand. According to digital analyst firm eMarketer, U.S. e-commerce sales are expected to grow 18% in 2020. The firm notes that while some of the extreme channel shifting that occurred during the early months of the pandemic will subside as reopening continues, the pandemic exposed many consumers to e-commerce for the first time and that will likely fuel increased growth in the coming years.
For brands and retailers to capitalize on this future growth they have to deliver on consumer expectations today. Yet the higher demand being experienced has stressed many fulfillment operations and made that more difficult, particularly for companies that haven’t yet automated or are still relying on rigid mechanized systems.
This has increased the urgency around automating fulfillment operations; however, organizations considering automation today face the challenges of implementing new technology during a period of high demand and economic uncertainty. They not only need to ensure the systems they deploy can adapt to whatever the future holds, they need to be able to move quickly enough to begin realizing the benefits of automation as soon as possible. Now more than ever, automation must deliver flexibility and short deployment times.
The Evolution of Warehouse Automation
Concerns about flexibility have been addressed through the current generation of robotic and data-driven goods-to-person automation solutions. Unlike the rigid mechanized automation systems of the past, robotic automation systems such as AutoStore and CarryPick provide the flexibility and scalability to meet changing demand while continuing to compress order cycle and delivery times. They deliver an ROI that is typically half that of mechanized automation systems and reduce the risk of obsolescence by being able to adapt to changes in demand, fulfillment processes and the products being supported.
With AutoStore, for example, you can add more robots at any time to support higher throughputs. You can also add more pick stations as demand grows or expand the modular storage cube to support more SKUs. CarryPick offers similar flexibility: you can add to your fleet of robots or put in more pick stations without disrupting operations. You can even pick up and move the entire system to a new warehouse if you outgrow your current space.
These systems also have the built-in intelligence that allows them to evolve as new technologies emerge, enabling integration of promising technologies such as robotic item picking and AI. They also naturally support socially distant work environments as pickers work within separate workstations that are fed products by the robotic systems.
Standardization Speeds Deployment
While mechanical systems could take years to plan and deploy, a customized robotic automation system can be deployed in 12-14 months, delivering a much faster return on investment and a longer useful life due to their ability to adapt to change.
But, just as with e-commerce delivery times, what seemed fast just a few years ago is no longer fast enough today. That’s why the next evolution in warehouse automation technology is focused on increased standardization to further reduce deployment times without compromising functionality. This is enabled by the combination of software maturity and the experience gained over years of implementations.
System design and software customization can add months to automation system implementations. As more automation systems are deployed, the need for customization is diminished. Many software capabilities that would have been considered “custom” several years ago are now integrated as standard features of our SynQ platform. In addition, the experience gained over almost 200 implementations has allowed Swisslog to develop standard hardware configurations that meet the needs of the majority of applications. We have reached the stage of maturity where standardization is practical and delivers significant benefits.
Swisslog is now offering standardized configurations of our AutoStore and CarryPick solutions that can go from contract completion to go-live in as little as six months. For both systems, three standardized configurations are available based on throughput requirements:
- A 400 order lines per hour configuration
- A 1,000 order lines per hour configuration
- A 2,000 order lines per hour configuration
Higher performance levels are available with a little engineering by our team of consultants, who have the experience of over 170 systems behind them.
While these systems feature a high degree of standardization, they provide the flexibility to tailor the number of robots, ports, racks and bins to specific application requirements. And, of course, both standardized and custom configurations have the ability to scale as needs change.
At Swisslog, we believe increased standardization represents the future of warehouse automation as it enables faster deployment times and shorter ROIs. For more information on our standardized AutoStore and CarryPick systems contact infona@swisslog.com.