Optimizing management of warehouse events to increase speed to market
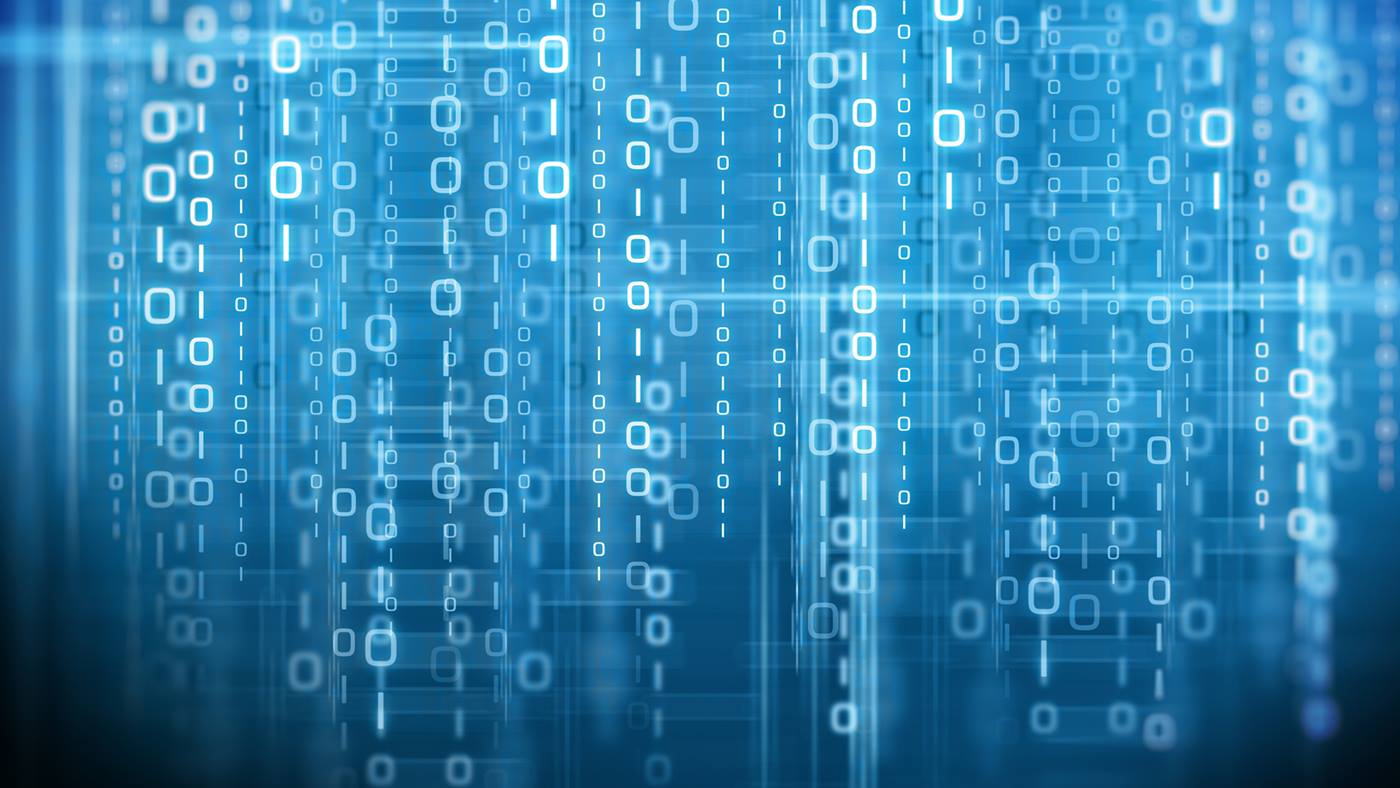
In today’s supply chain, data that was once considered marginal or of no practical use, can become a strategic asset through the integration of Industry 4.0 technologies. This requires eliminating the delays in data transfer typical with outdated software architectures.
Adopting Industry 4.0 doesn’t just mean using automated production and logistics systems. Equally important is ensuring the assets involved can share the information necessary for the functions dedicated to the development of corporate business and thus reduce the time to market for the goods produced, managed and sold by any company.
For example, knowing a certain product is moving toward a shelf and will soon be available or knowing how picking lines are being used in real time, allows the warehouse back office to organize loading equipment and staff more effectively to increase handling volumes from and to the warehouse.
We enable this capability through our SynQ software platform.
As you would expect, SynQ manages the machine movements in the plant, reducing the impact of software updates on other systems. But it also provides integral support for the ERP system, which initiates the implementation of corporate business processes in a warehouse environment. We call this the SynQ effect.
Key to SynQ’s ability to add value to the ERP system is the creation of “events.” A management event is created every time goods are handled, whether by machine or human. Events are captured in real time and transferred directly to the ERP system, which makes this information available to corporate production and commercial processes.
For example, when goods are physically placed on the warehouse shelf or in an automation system, this change in status is communicated in real time to update the ERP system’s “logical warehouse,” so the system knows that goods are ready to be used to fill final customer orders.
Considering the number of logistics processes running in a complex warehouse, it’s easy to imagine how all the events created can be stored and used for any purpose, including monitoring, statistics, and handling predictions.
Last, but not least, thanks to the events’ mechanism and the latest data exchange technologies for web services made available by SynQ, the whole (hardware and software) infrastructure can exploit the system’s technological potential to the fullest, reducing or even eliminating those typical delays in intermediate production processes introduced by pre-Industry 4.0 automation systems. It even creates the opportunity to use machine learning with event data to enhance the performance of automation systems.

Learn how Swisslog enables pharmaceutical manufacturers to use material handling automation to maximizes space utilization, minimizes product touches, and streamlines regulatory compliance.