Selecting software for food and beverage warehouse automation
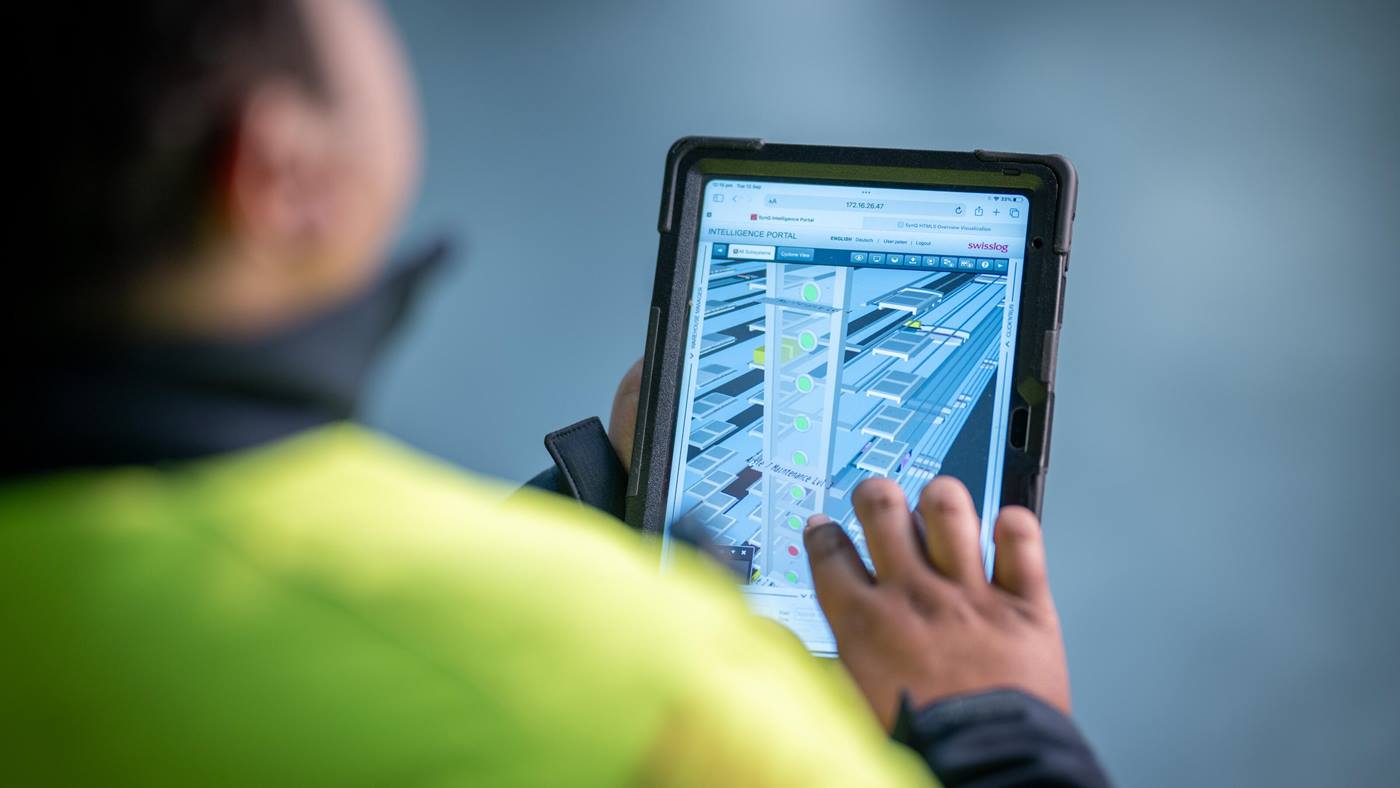
Food and beverage manufacturers generally understand that warehouse automation can increase storage density and reduce the labor required to fill orders. As a result, those factors tend to dominate the business case for automation. However, they don’t encompass the full value automation can deliver. Much of the added value that can be achieved is made possible by the software that controls the automation solution and seamlessly integrates the automation into the holistic warehouse processes and the supply chain and delivery processes.
How software enhances the business value of warehouse automation
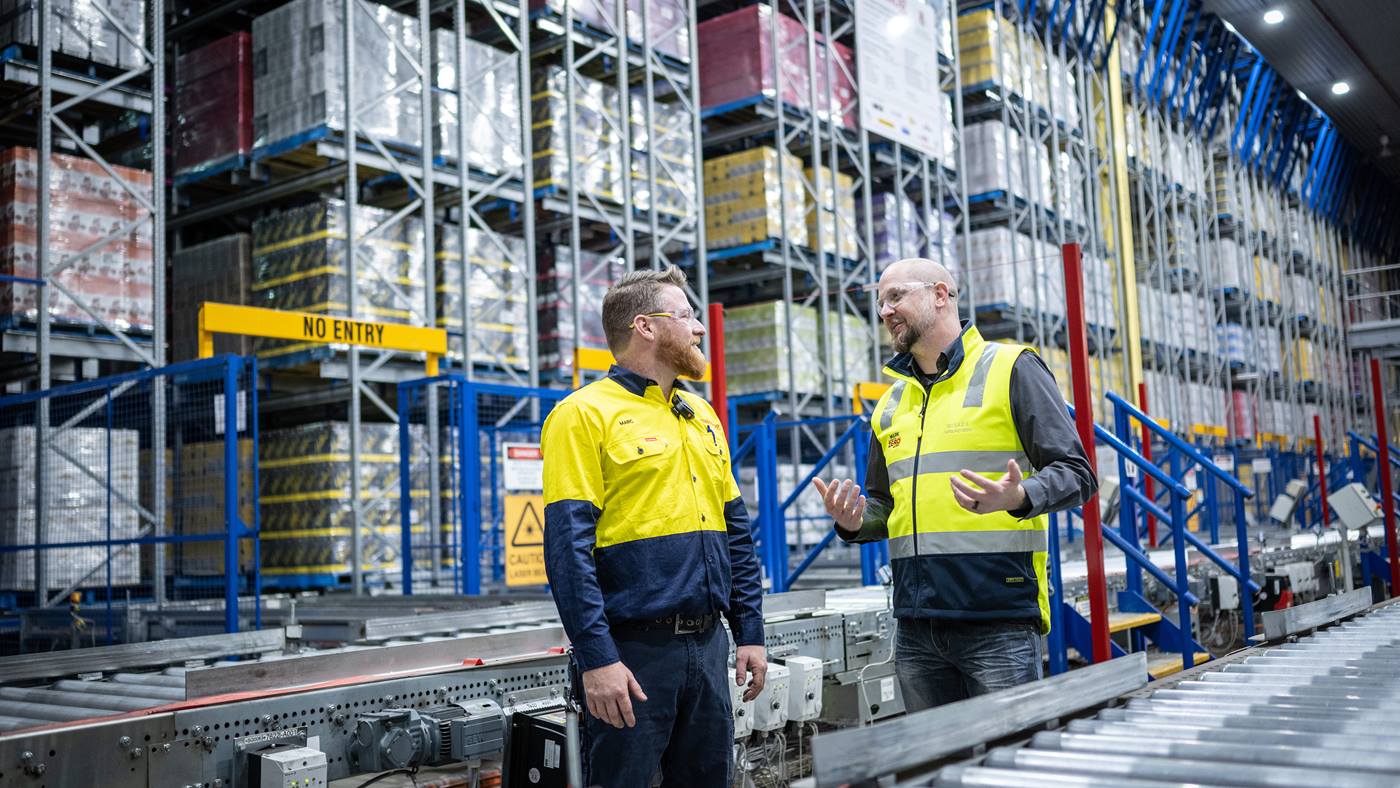
It starts with capabilities that reduce the investment in automation by eliminating the need to oversize systems due to inefficient management and sub-optimal performance. For example, Swisslog’s SynQ software uses algorithms that optimize ASRS management to reduce wait times and deliver pallets in the sequence required for efficient material flow. This allows right-sized solutions to deliver levels of speed and performance that meet or exceed an oversized solution.
Digitalization also brings greater intelligence to inventory and order management. By enabling the precise tracking of item locations and movements, the ACS can virtually eliminate human errors like misplacement or miscounting of items, reducing stockouts and overstock. Plus, digitalization enables more flexible and granular shelf-life management. Through intelligent inventory and order management, an ACS can calculate the remaining shelf life at delivery for each order, allowing product for a particular order to be retrieved based on expected delivery times and customer priority.
In addition, digitalization improves the speed and predictability of order fulfillment by optimizing picking and routing based on order priority, inventory availability, and resource capacity. The aim is not just to automate manual processes, but to design processes that work with automation and are therefore more efficient.
Through these capabilities, the right automation control software can strengthen the business case for automation by reducing the capital investment required to deploy automation, reducing inventory costs, improving order quality and accuracy, and enhancing customer service levels.
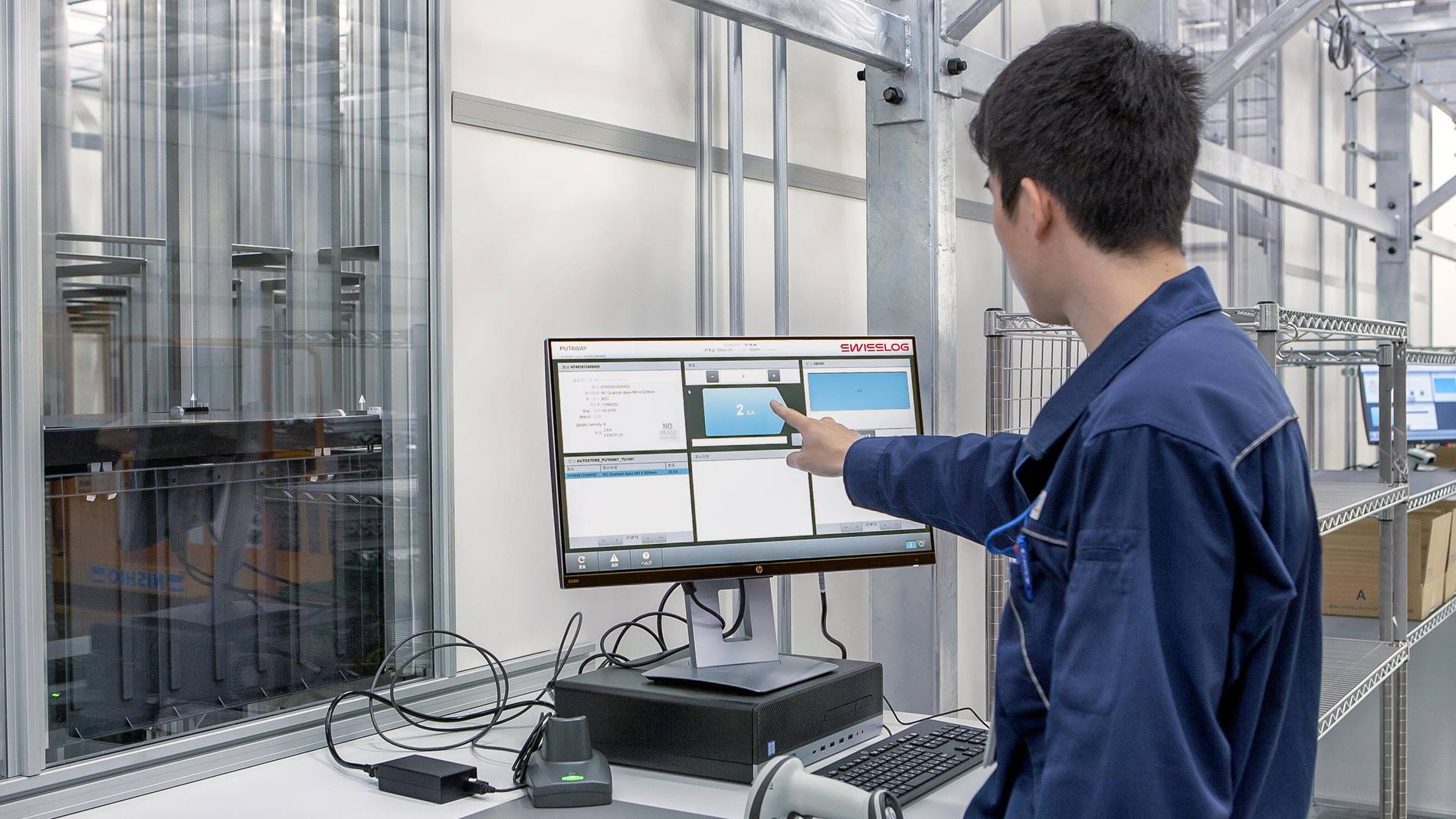
How software improves operations in automated warehouses
ACS software also delivers significant day-to-day operational value by efficiently managing demand variability, supporting better decision making, and streamlining the response to events like product recalls.
Software capable of controlling all components of an automation solution – including the ASRS, conveyors, AGVs and palletizing systems – as well as manual processes can synchronize processes and dynamically balance workflows and resources to eliminate bottlenecks and keep materials moving during demand peaks. The visibility and analytics provided by the software can also simplify management and allow managers to effectively use warehouse data to monitor and improve operations.
Swisslog SynQ software, for example, allows managers to monitor key performance indicators through real-time display of KPIs. They can also use a 3D digital shadow of the warehouse and its operations to monitor processes and easily access detailed product and order information.
The software can also help mitigate the impact and reduce the costs of a recall. Again, using SynQ as an example, the system can quickly locate impacted products – including those already shipped – based on batch, best-by date, or other information and block and store affected products while issues are being resolved.
In summary, the software that supports automation provides managers and operators with the ability to improve operational efficiency and flexibility, and dynamically align resources and processes with demand.
Must-have capabilities for automation control software in food and beverage
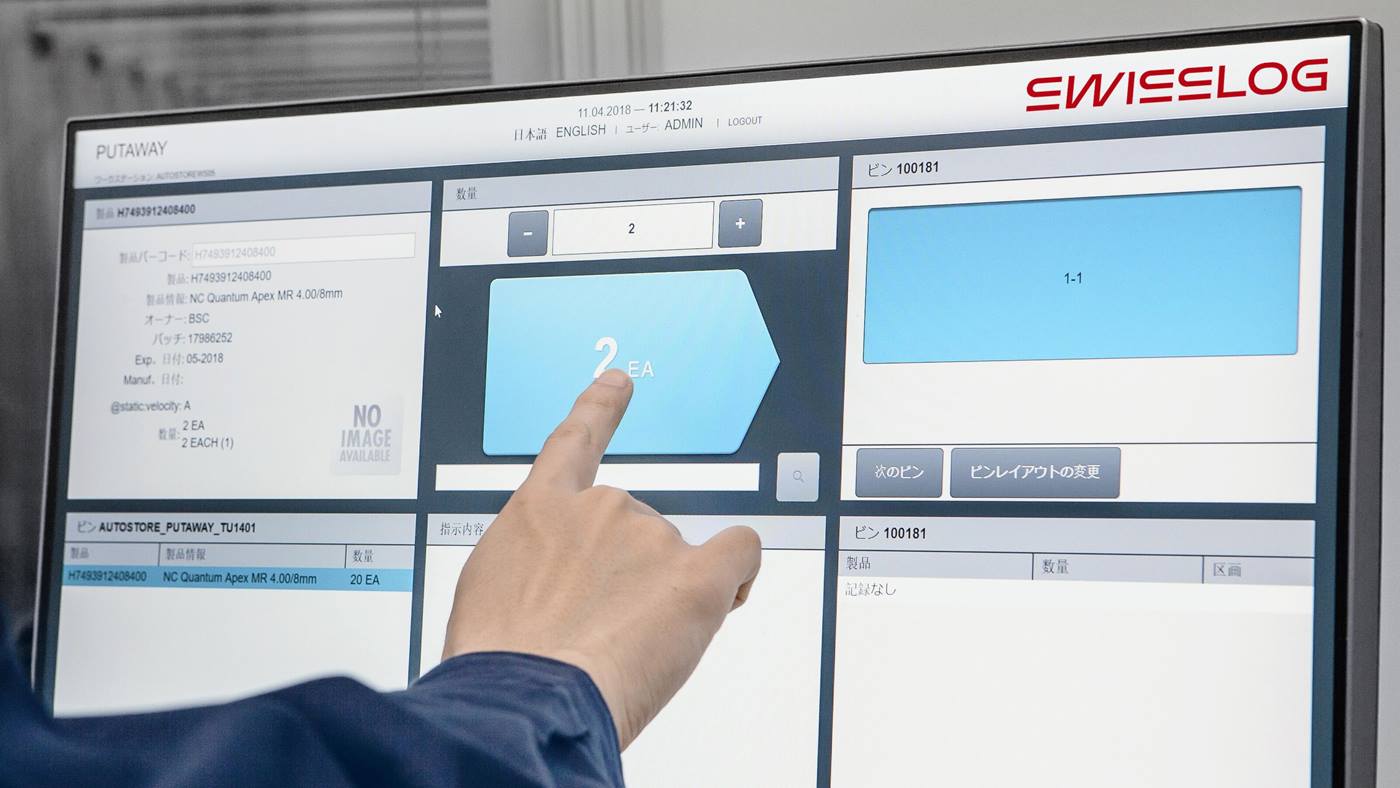
- Modular pre-configured platform architecture: To maximize the value of your solution, you’ll want a modular software platform that integrates automation control, warehouse execution and warehouse management capabilities. This allows you to leverage the capabilities of existing warehouse systems while closing the gaps in those systems that are limiting digitalization, preventing visibility into operations, and inhibiting process synchronization and resource orchestration. Industry and automation-specific pre-configurations reduce risk and project runtimes, enhancing the value of extensive food and beverage industry experience.
- Flexible, intelligent inventory and order management: Food and beverage manufacturers have different inventory management requirements than other industries, so make sure your software can support your specific requirements. Can it manage inventory based on batch, expiry date, best-by date or any other factors important to you and your customers? And can it intelligently integrate inventory and order management to meet customer expectations for product shelf life at delivery?
- Resource orchestration and process optimization: An automation control system that only controls the ASRS effectively silos the ASRS from other warehouse processes. Select software capable of controlling all components of your automation solution as well as manual processes.
- Traceability, visibility and analytics: Traceability is a must-have for food and beverage manufacturers so ensure your software supports detailed tracking of movements within the warehouse, both in terms of stock changes and physical location. You’ll also want a platform that simplifies data collection and analytics to ensure effective management of warehouse operations. Manufacturers that have deployed solutions that provide 3D visualization of warehouse operations have found this capability invaluable in day-to-day warehouse management.
- Intuitive, consistent user interface: How operators and managers interact with your solution can have a significant impact on productivity. Evaluate the user interface in terms of ease-of-use and consistency across the components of a solution. In many warehouses, the ability to support multiple languages and deliver information to operators in their preferred language can also be highly valuable.
- Maturity and security: Beyond functionality, take the time to learn how software is developed and managed as these “behind-the-scenes” processes can have a direct impact on operations over the life of your solution. Make sure your provider has a multi-year product roadmap, integrates security into design and implementation processes, and has a well-defined plan for technical upgrades. Also, find out if the same platform is used in all regions. A global platform enables software standardization across locations and also allows the provider to focus resources on advancing and supporting one platform rather than diluting resources and expertise across multiple systems.
Getting more from warehouse automation in food and beverage
Swisslog has decades of experience providing automation solutions for food and beverage manufacturers and that experience is captured in our modular and pre-configured SynQ software platform. SynQ delivers the functionality, intelligence and visibility food and beverage manufacturers need to maximize the business and operational value of warehouse automation.
To learn more, visit our website or contact us.

Learn how Swisslog enables pharmaceutical manufacturers to use material handling automation to maximizes space utilization, minimizes product touches, and streamlines regulatory compliance.