Using ASRS for order consolidation in retail fulfillment
Bob Hoffman
28 September 2021
Reading Time:
4 min.
The challenges of consolidating orders to meet customer pickup requirements have led more organizations to consider adding a buffer system to last-mile fulfillment centers.
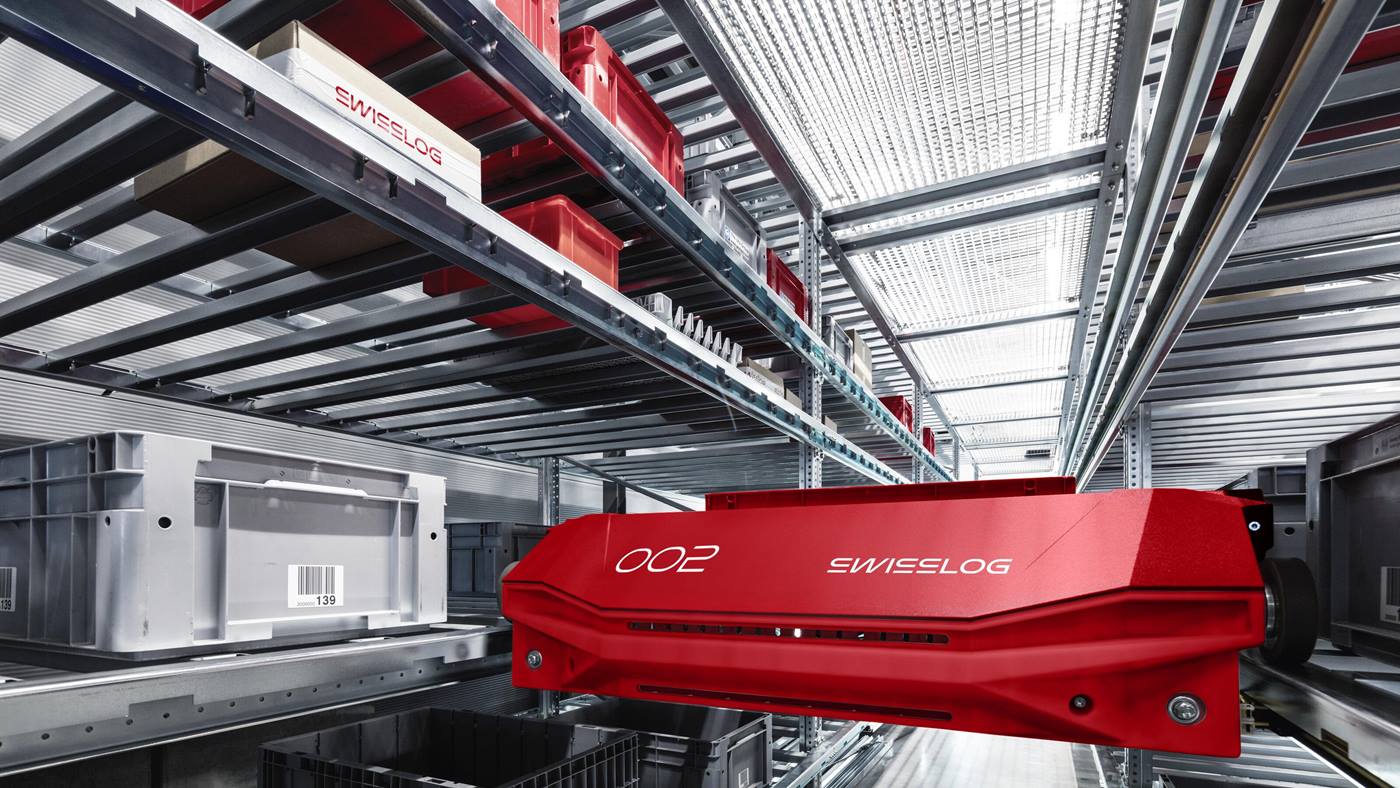
The retail order fulfillment landscape has changed dramatically in the last several years. Responding to consumer demands for speed and convenience, retailers are now enabling faster and more flexible e-commerce fulfillment by leveraging their retail locations to support pickup or delivery from the store. In the first quarter of 2021, for example, Target saw year-over-year e-commerce growth of 50.2%, and 75% of digital orders were filled from a retail store.
As the volume of e-commerce orders being fulfilled through stores continues to grow, retailers in high-volume sectors such as grocery, pet food and DIY are expanding their distribution network to enable automated fulfillment closer to customers. The grocery sector is leading the way in this evolution with leading grocers already deploying local distribution centers serving multiple stores in a hub-and-spoke arrangement, in-store micro fulfillment centers, and dark stores offering pick-up and delivery without in-store shopping.
Optimizing Order Fulfillment
The key to fast and efficient last-mile fulfillment is proving to be ASRS systems that enable goods-to-person picking. These systems deliver the dense storage space-challenged micro fulfillment centers require while increasing picking efficiency by 5-7 times compared to manual processes. They also eliminate the congestion in-store manual picking creates.
As we discussed in an earlier post, there is a science to determining which products should be fulfilled through automation and which should be fulfilled manually in a particular micro fulfillment center. There are, of course, physical size limitations to the products that can be stored in a goods-to-person system based on the size of the bin a particular automation system uses and how bins are stored.
A cube-based ASRS, for example, achieves high density by stacking bins on top of each other in a grid; however, this design limits the height of the products stored to the height of the bin. Shuttles, such as Swisslog’s CycloneCarrier, on the other hand, don’t deliver the same density as cube-based systems, but also do not store bins on top of each other and so have more flexibility in what can be stored in the bins. With CycloneCarrier, the option for increased bin size in all directions enables larger SKUs to be stored in the system.
Beyond size, there are other reasons products may not be stored in the AS/RS system, most notably high-volume items that can be more efficiently picked manually. In grocery applications, frozen food, and specialty items such as fresh meat and seafood will also generally be stored outside the automation system.
The result is that in almost every goods-to-person application, final orders are consolidated through a combination of manual and automated processes and timing for the two processes can vary, particularly during periods of high demand.
The right automation software can orchestrate manual and automated fulfillment, but order consolidation can still be a challenge in micro fulfillment centers where space is limited and there is the need to react to the customer’s timing when orders are picked up at the store. Hard sequencing can be added to the system software to create a solution that delivers the order bins from multiple areas just in time; however, this strategy has proven to be very complex and can have an adverse effect on the overall efficiency and throughput of the solution.
Order Consolidation Requirements
The challenges of consolidating orders to meet customer pickup requirements have led more organizations to consider adding a buffer system to last-mile fulfillment centers. In this application, the buffer enables synchronization of auto and manual processes in space-constrained fulfillment centers and allows the fulfillment center to better manage peaks in order pickups. Allowing the consolidation automation to gather the order from multiple pick zones, consolidate the order and then release it on demand enables the upstream system to work more dynamically and thus more efficiently.”
While the requirements of goods-to-person picking and buffering systems are similar, there are also important differences between the two that can limit the effectiveness of some goods-to-person technologies when used for order consolidation. Buffer systems don’t require the high-density storage that retailers need from their goods-to-person systems. Instead, the priority is delivering high throughput during peak periods. Automation systems that prioritize density over throughput may not be as well suited for order consolidation.
Integrating a Buffer in an MFC
While every MFC is different and requires a tailored solution, using a cube-based AS/RS for goods-to-person picking and a shuttle system for order consolidation is proving to be an ideal combination that leverages the strengths of each technology to optimize e-commerce fulfillment at the retail level. Doing this minimizes the number of touches as well. Once picked into, the order tote goes straight into the buffer and doesn’t require re-handling to move consumer-facing plastic or paper bags into buffer-ready totes.
In these environments, having a software platform that includes automation control modules for cube and shuttle systems, as is the case with Swisslog’s SynQ software, becomes a huge advantage. SynQ provides full inventory management capabilities and can orchestrate activities across the pick engine and buffer systems as well as manual picking operations to manage both picking and consolidation. Having a single platform controlling all order fulfillment activities also ensures a common user interface across systems and processes, reducing time-to-productivity for new hires and enhancing workforce flexibility.
Store-level fulfillment is becoming key to e-commerce success and, for high-volume retailers, automating store fulfillment is an important step in managing e-commerce growth. Swisslog is working with a number of retailers today to design last-mile fulfillment centers that integrate shuttle and cube-based technologies to enable faster and more efficient store-level fulfillment. For more information on Swisslog’s retail fulfillment experience, visit our website or contact us by clicking below.