5 benefits of Swisslog’s SynQ 3D Visualizer
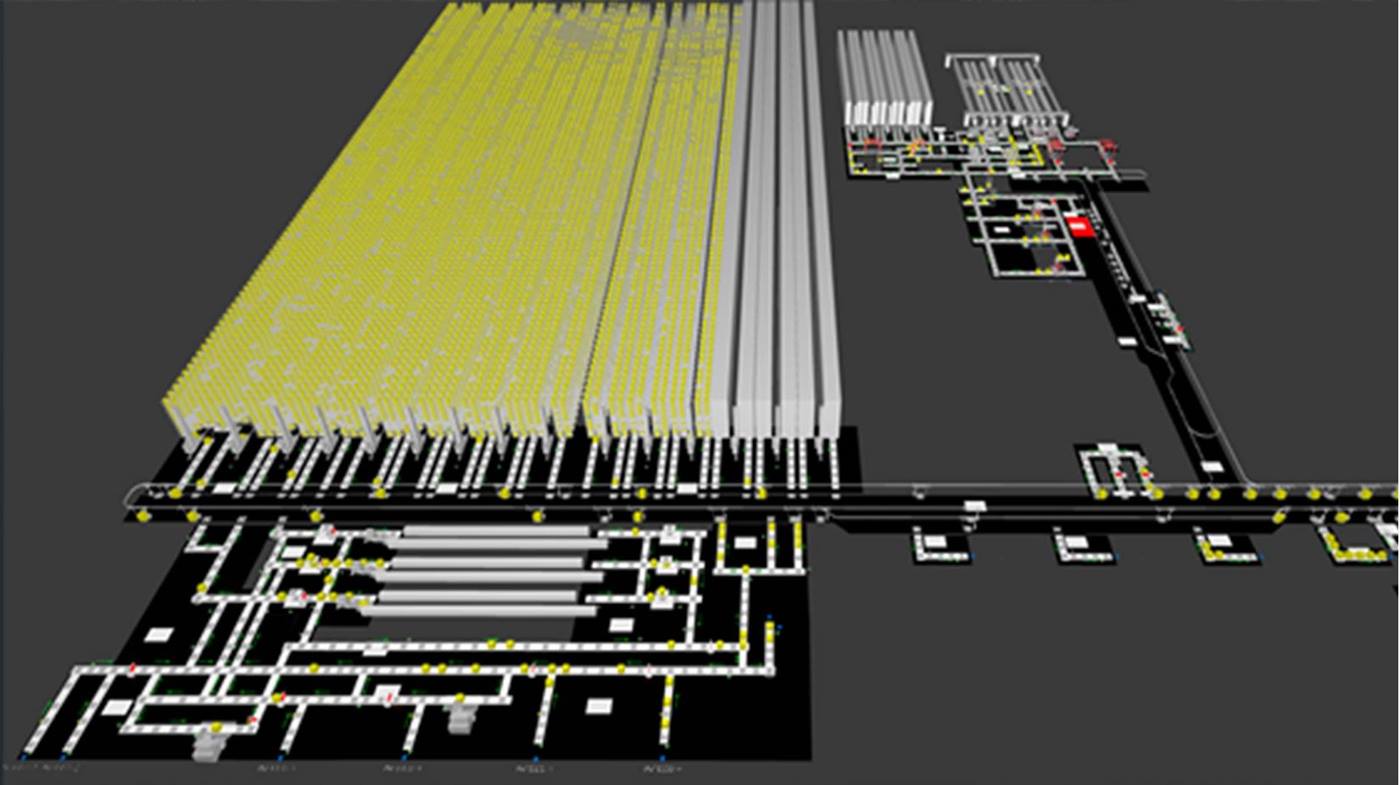
This is the second in a series of five blogs focused on the real-world benefits of Swisslog's modular WMS, SynQ. The first blog focused on the benefits SynQ is bringing to customer service teams in addressing the new challenges caused by COVID-19. This blog will now take a more in-depth look at SynQ's 3D automation viewer.
For companies with a high level of logistics automation, it is vital to be able to combine automated warehouse asset management with IT tools to enable remote management and monitoring of in-plant activities.
In this blog, we're going to outline 5 benefits the SynQ 3D Automation Visualizer is providing to Swisslog's customers who have adopted it and will provide to those who will adopt it in the near future.
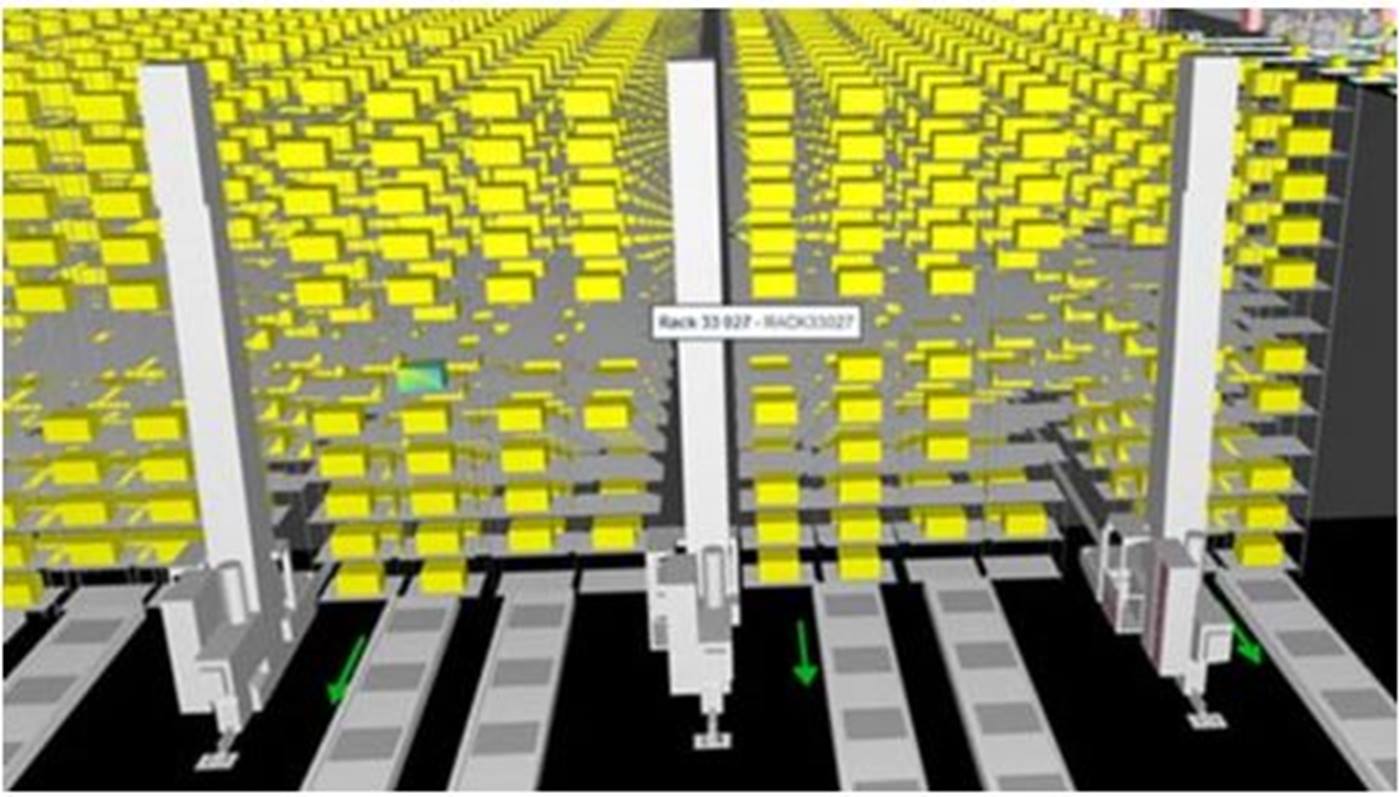
1. The best representation of reality in automated logistics
Today, the closest thing to reality in web-oriented technology is 3D visualization. Interacting with mechanical components and goods, and extracting information from the warehouse is just a mouse click away.
Being able to have a picture as close to reality as possible is an increasingly frequent request from our customers and our customer support. The visualizer must, as much as possible, give a real representation of the state of the machines and the conditions of the warehouse (occupation, movements in progress/waiting) in order to allow a human being a complete an effective analysis for the resolution of any problems or more simply for the extraction of information from the warehouse.
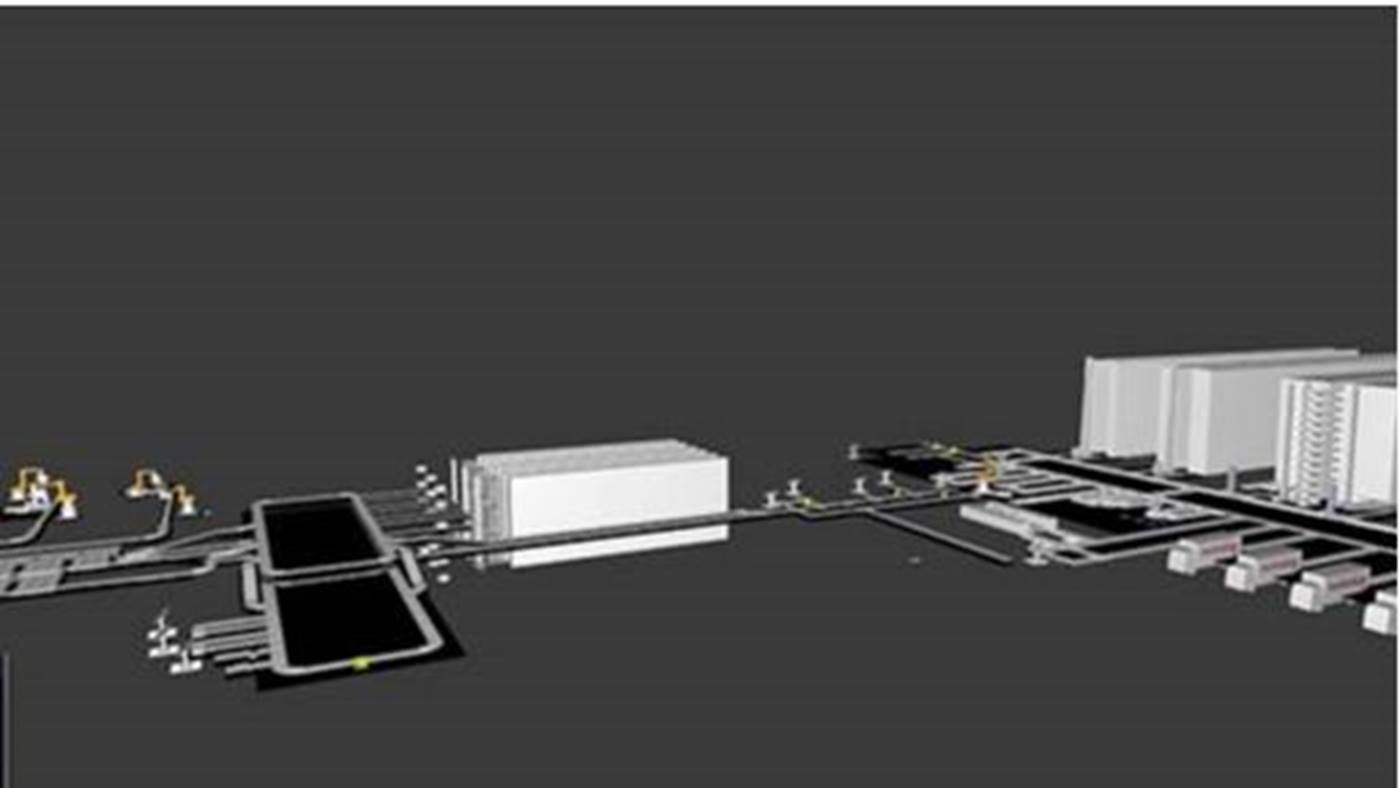
2. Remote management and supervision of logistics plants with high surface areas
In plants with a large surface area, it can be difficult to identify the areas of the warehouse that need improvement in terms of the use of logistics flows. Warehouse logistics managers often realize that the warehouse has the potential to operate more efficiently, but the lack of data and tools hinders them from identifying where this potential can be developed.
The global vision given by the 3D representation of the automatic system, together with the ease of navigation (mouse and keyboard) reduces inefficiencies in the identification of intervention areas, minimizing delays in the application of corrective actions of recovery after a technical malfunction or production accident.
With a click of the mouse, the user is able to see all the information about the goods in transit on the machines located hundreds of meters away.
The global vision provided by the 3D viewer allows warehouse managers to optimize load flows and improve peak work management, increasing the flow of goods and warehouse productivity. The analysis of the flows in the warehouse areas subject to a high traffic of goods allows, therefore, to apply corrective measures in order to reduce the inefficiencies deriving from them.
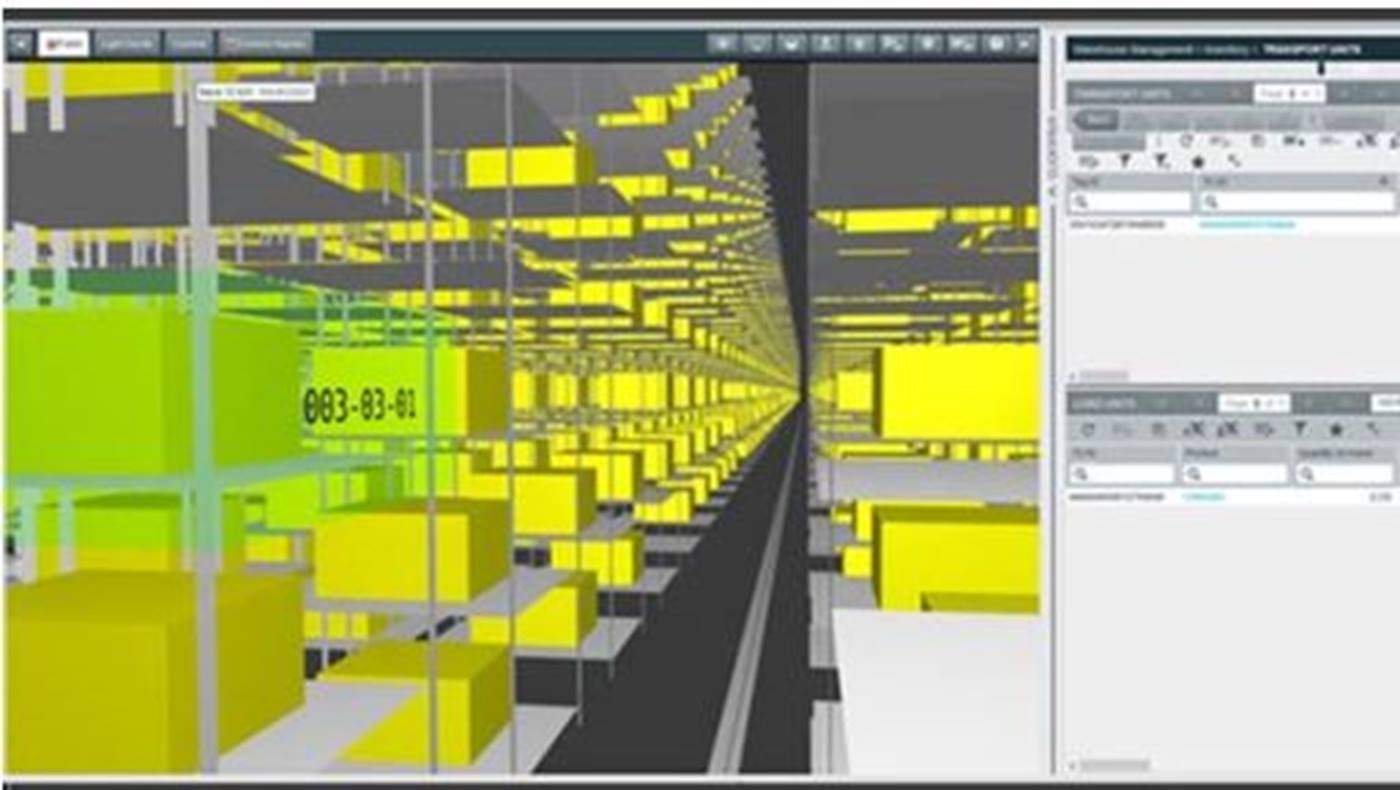
3. Virtual warehouse navigation
The ease of navigation offered by SynQ 3D Automation Visualizer allows operators to move virtually along the production lines and between the shelves of the warehouse itself. At any point in the navigation, they can interact with the warehouse components and ask SynQ for the information they need at that moment.
In the image, you can see how the selection of the shelf location produces, in the right part of the viewer, information on the located pallet in terms of ID, product code, and quantity. The data shown is provided by SynQ starting from the selected location only.
In this way the user can virtually "climb" up to the upper floors of shelves more than 30 meters high and with a single click of the mouse, they can acquire information about those locations. The user can learn if the goods are assigned to an order, if they are waiting to be picked for a customer, if they are available or blocked, and if they are intended for manual or automatic picking.
In cold warehouses (-27 degrees Celsius), it reduces the frequency of operator access to the cold room for checks of this kind, while reducing the risks and time required to extract data from the warehouse.
This reduces risk and improves overall efficiency because it also eliminates delays that would be caused by workers needing to take a break from the cold environment.
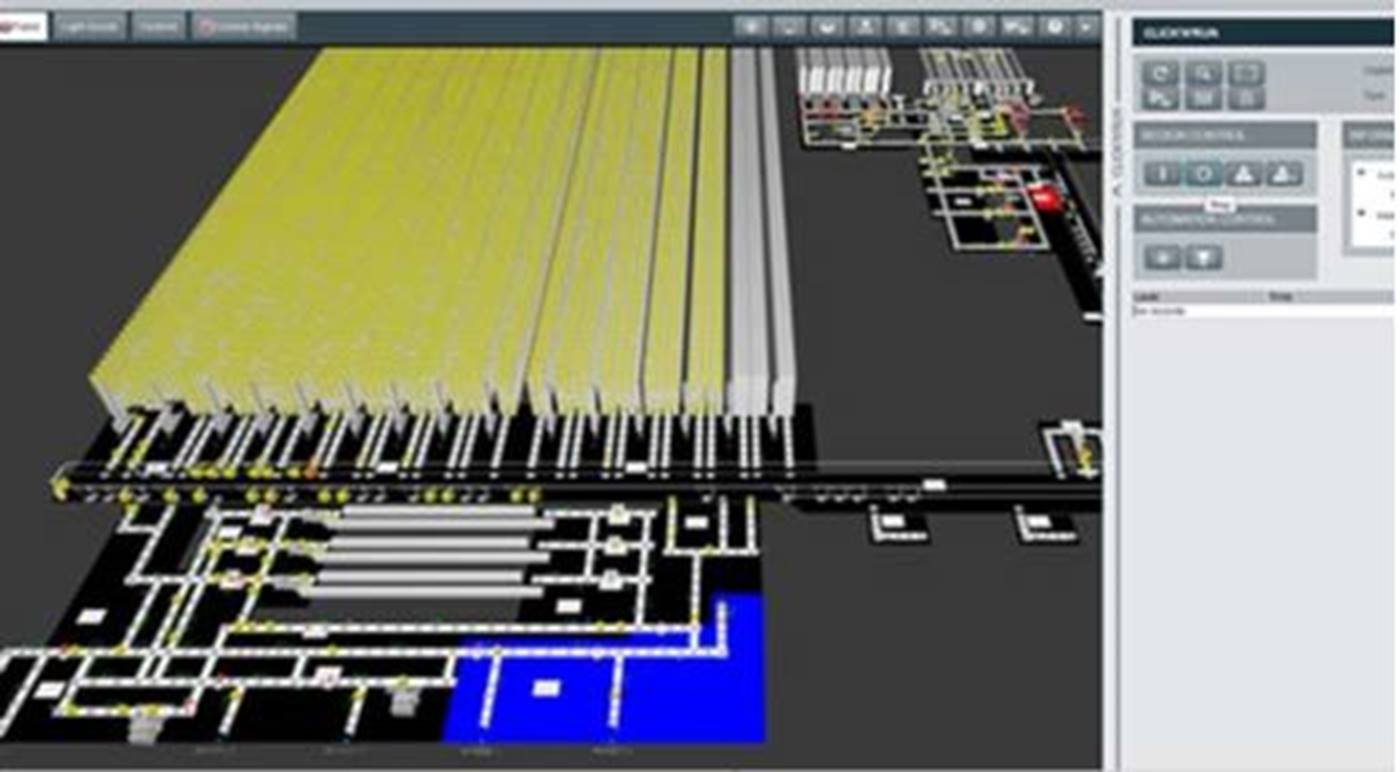
4. Real-time interaction with all warehouse components
In every moment, the visualizer receives and processes events coming from the automated systems, converting data into visual information for the use and consumption of the operator. The blocking of an automatic movement, the display of an alarm event, but also, for example, the parking of frozen goods in the ambient temperature zone (in the case of cold systems) are all examples of information that would be transmitted to the warehouse operator in order to allow a rapid response.
Each mechanical element is selectable, and its selection produces a request for information directly sent to the machine that provides the answer in real time so as to obtain information that is not already obsolete. The information available from the machine includes the general status, the mode of operation and, if present, the goods that are passing through it.
The control panel displayed when the component is selected allows the user to interact with basic automation functions such as switching the system on and off, displaying and resolving faults at the push of a button.
All automation systems produced by Swisslog are integrated with the 3D visualizer via SynQ. The communication protocol for the realization of these interactions is based on international standards and can also be integrated on machines not directly produced by Swisslog. This mode allows SynQ to manage information coming also from external equipment not natively integrated.
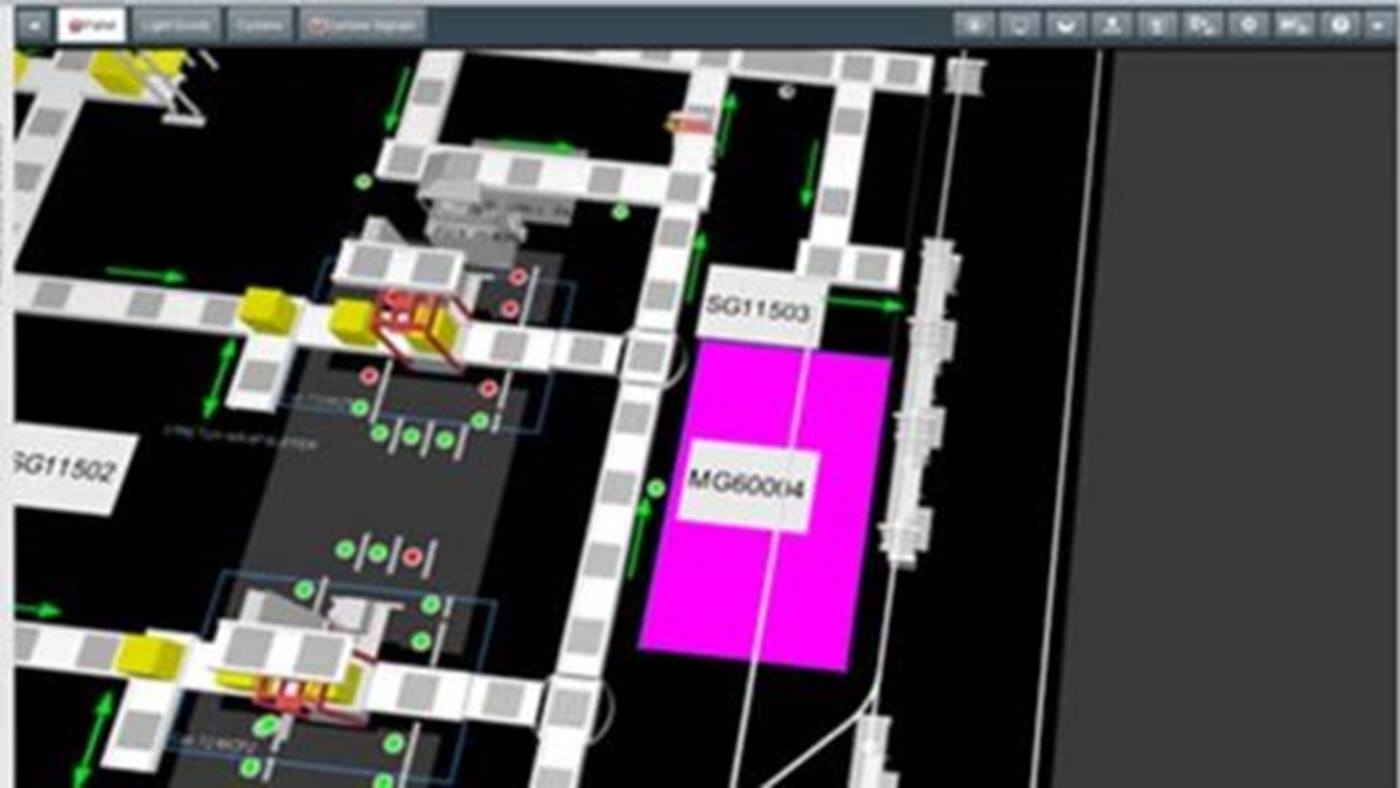
5. Diagnosis and resolution of malfunctions with remote connection
The overview provided by the 3D visualization, combined with web-oriented technologies, allows the operator to identify anomalies and malfunctions reported by the automation remotely, reducing the need for on-site intervention with a consequent reduction in human action and reaction times.
The operator is notified of the magnitude of the malfunction by means of a graphic report and upon selection of the report, a text message containing the cause and the possible resolution procedure is displayed.
The visual management communicates to the operator the position of the machine affected by the malfunction and the message (in the right part of the viewer dedicated to notifications) conveys the extent of the anomaly, as shown in the following image.
This information allows the operator to estimate the entity of the anomaly and to prepare the set of corrective actions that, in the first instance, can be applied to restore the operation of the automation.
If the malfunction is such that it does not allow an immediate resolution, the information is transferred to the Swisslog customer support team, which can remotely access and analyze the information in order to plan emergency or preventive maintenance interventions.
As a leading global automation partner, Swisslog provides a wide range of IT tools to fully visualize and monitor a warehouse and use this data to optimize performance.
Through innovative technologies and experienced software experts, Swisslog supports its warehouse and distribution center customers who have increasingly pressing needs in a rapidly growing and evolving market. To learn more about how Swisslog's SynQ 3D Automation Visualizer can optimize your warehouse operations, get in touch with a Swisslog expert.