New report reinforces growing importance of automation software
Colman Roche
23 พฤษภาคม 2568
AutoStore recently released its third annual report on the State of Warehouse Management and Fulfillment. Based on a survey of more than 300 global executives with supply chain responsibility, the report identifies warehouse priorities in 2025 and benchmarks automation use. An analysis of the report data also reinforces the critical role warehouse execution and automation control software can play in the current and future state of warehouse management.
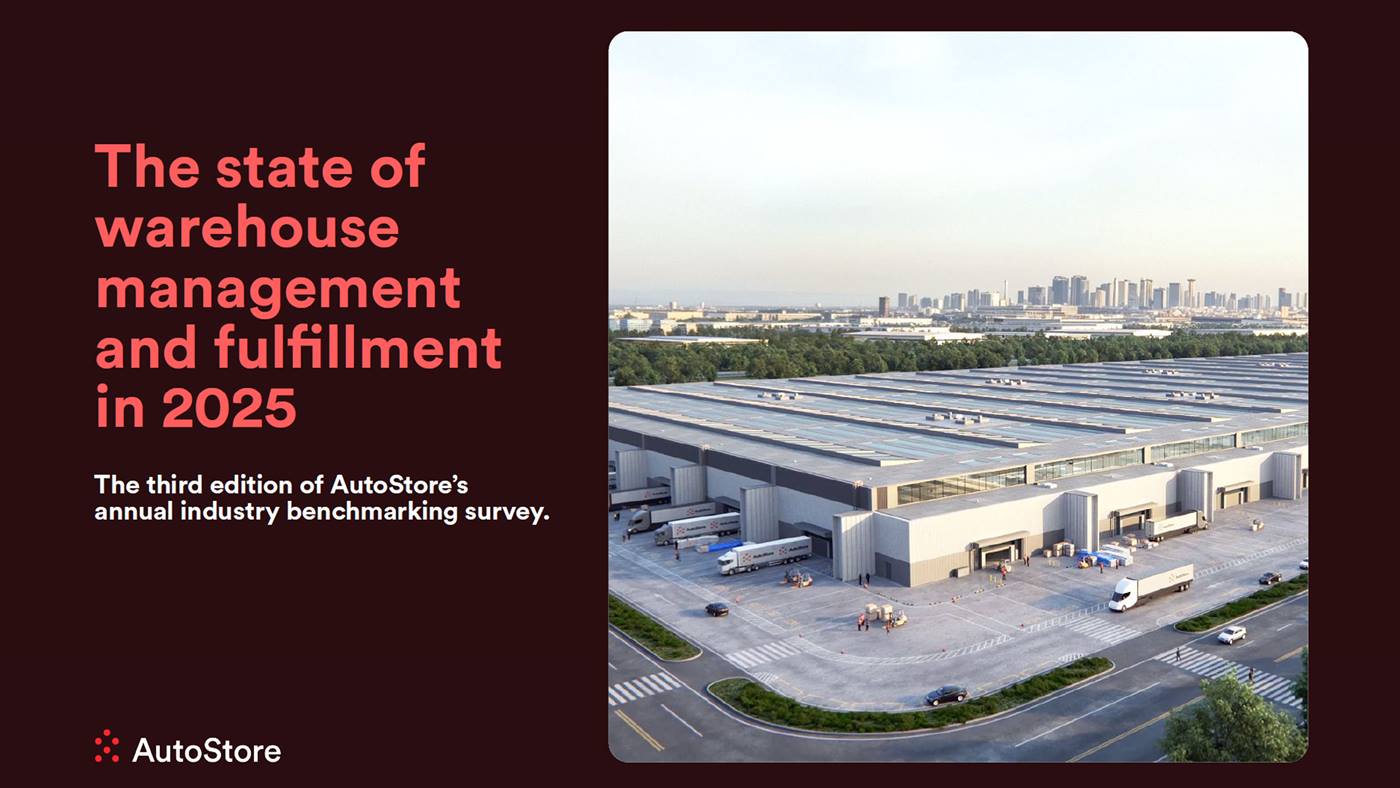
The State of the Warehouse Management and Fulfillment in 2025 report from AutoStore highlights the evolving challenges and opportunities facing today’s supply chain leaders. As a leading AutoStore integrator, Swisslog has analyzed this year’s report with an eye toward the role software can play in unlocking higher levels of performance in areas survey participants prioritized. Here’s what we found.
Warehouse execution and automation control software not only plays a key role in enabling the collection of these metrics but can also drive improvements in the metrics that matter most to supply chain executives. Here are some examples:
Impacting the metrics that matter
One of the interesting findings in the report is the range of metrics survey participants regularly collect to measure operational performance and efficiency. Twenty different metrics were used by at least 10% of participants, including various forms of throughput measurement. Other popular metrics relate directly to fulfillment efficiency, such as on-time shipping, labor efficiency and picking accuracy.Warehouse execution and automation control software not only plays a key role in enabling the collection of these metrics but can also drive improvements in the metrics that matter most to supply chain executives. Here are some examples:

It’s important to note that not every AutoStore solution includes all of these capabilities. In fact, to our knowledge, Swisslog’s AutoStore solution, empowered by our SynQ platform, is the only solution that provides all of these capabilities in a single platform.
The AutoStore solution is ideal for ultra-high throughput applications—it can be configured to support throughputs of 20,000 or more picks per hour. The solution also provides the flexibility to add more robots or pick stations to achieve higher throughput of already installed systems. But adding hardware isn’t the only path to higher throughput.
Some automation users may assume system performance at startup represents the ceiling for their solution. In our experience, that’s rarely the case. At Swisslog, we regularly work with our customers on optimization strategies that squeeze additional performance out of their solution as they gain more experience with it. If you need more throughput, your first step should be to work with your integration partner to explore opportunities to optimize your solution.
Next, evaluate the potential of newer software capabilities. With SynQ software, for example, AutoStore users can change bin selection criteria to prioritize throughput, density or balance the two. When throughput is optimized, this capability can increase bin retrieval speeds by up to 20%. SynQ can also batch orders to maximize the operator “hit rate” or “batch factor”—the number of SKUs that can be picked from each bin presented.
If you are in an omnichannel warehouse or other environment where you are fulfilling different order types, such as a combination of bulk orders and individual orders, having the flexibility to direct order types to designated pick stations allows those pick stations to be optimized for the order type, improving fulfillment efficiency.
On their own, or working with hardware modifications, these strategies can unlock new levels of AutoStore performance.
Supporting the push for higher throughputs
According to the State of the Warehouse and Fulfillment in 2025 report, improving throughput performance rose from the 8th highest priority in 2024 to 4th in 2025. In addition, 93% of participants considered “improving throughput” to be very important or extremely important. In other words, almost everyone wants to be able to get more out of their automation system.The AutoStore solution is ideal for ultra-high throughput applications—it can be configured to support throughputs of 20,000 or more picks per hour. The solution also provides the flexibility to add more robots or pick stations to achieve higher throughput of already installed systems. But adding hardware isn’t the only path to higher throughput.
Some automation users may assume system performance at startup represents the ceiling for their solution. In our experience, that’s rarely the case. At Swisslog, we regularly work with our customers on optimization strategies that squeeze additional performance out of their solution as they gain more experience with it. If you need more throughput, your first step should be to work with your integration partner to explore opportunities to optimize your solution.
Next, evaluate the potential of newer software capabilities. With SynQ software, for example, AutoStore users can change bin selection criteria to prioritize throughput, density or balance the two. When throughput is optimized, this capability can increase bin retrieval speeds by up to 20%. SynQ can also batch orders to maximize the operator “hit rate” or “batch factor”—the number of SKUs that can be picked from each bin presented.
If you are in an omnichannel warehouse or other environment where you are fulfilling different order types, such as a combination of bulk orders and individual orders, having the flexibility to direct order types to designated pick stations allows those pick stations to be optimized for the order type, improving fulfillment efficiency.
On their own, or working with hardware modifications, these strategies can unlock new levels of AutoStore performance.
Managing automation growth
Automation users were well represented in this year’s survey: 97% of participants have implemented some form of warehouse automation with 48% reporting they were less than 50% automated.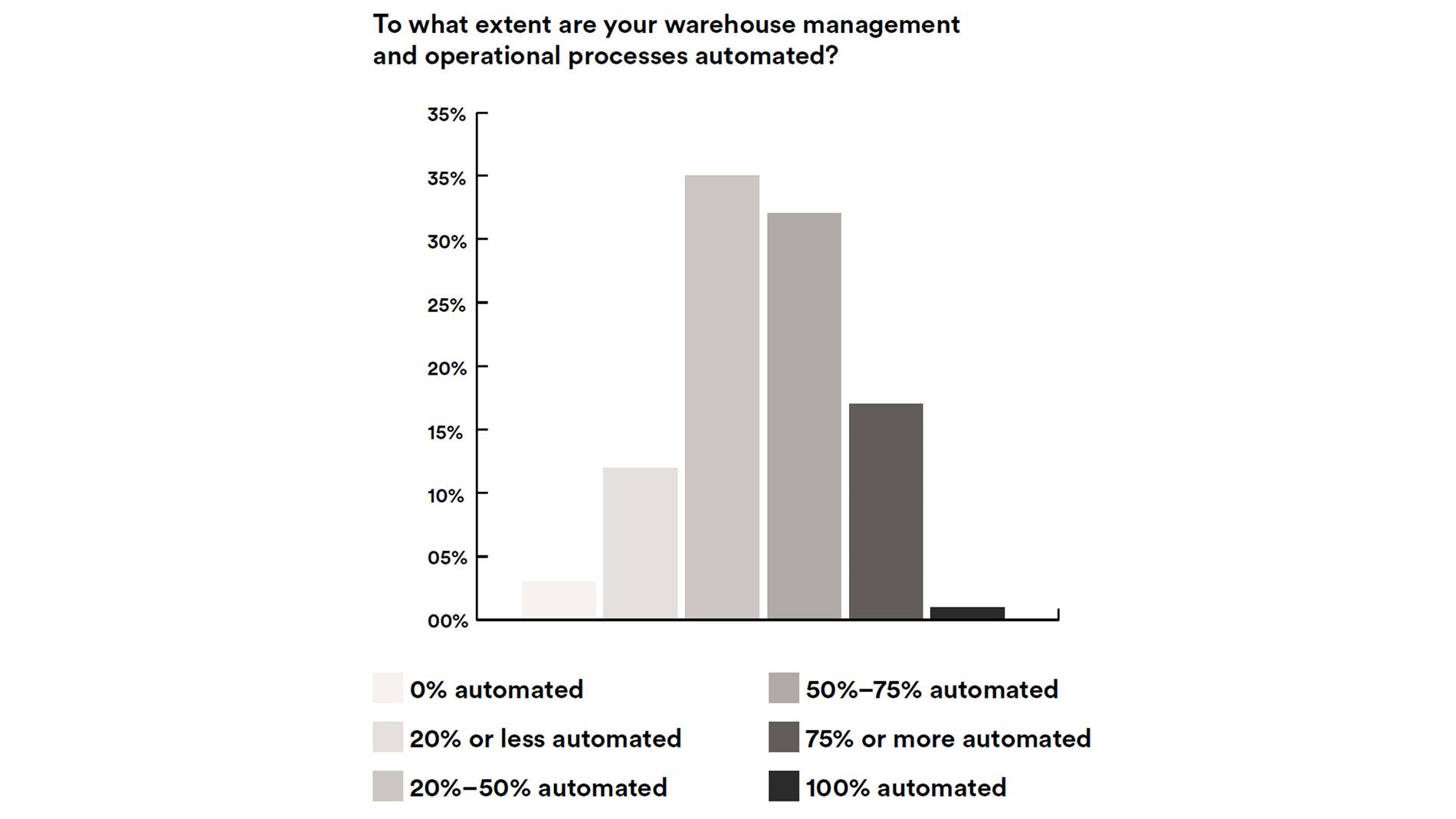
Source: AutoStore State of Warehouse Management andFulfillment in 2025
As organizations expand their level of automation to drive productivity and throughput higher, they risk having to manage multiple software systems that aren’t fully integrated and thus introduce a layer of complexity and reduce the ability to use data and analytics to drive operational improvement.
The alternative is choosing intralogistics software that is capable of seamlessly integrating across various technologies. With our SynQ platform, operators can unify control of multiple automation systems. The result is simpler system management, faster recovery from errors, and easier adaptation to changes in demand or process requirements.
The alternative is choosing intralogistics software that is capable of seamlessly integrating across various technologies. With our SynQ platform, operators can unify control of multiple automation systems. The result is simpler system management, faster recovery from errors, and easier adaptation to changes in demand or process requirements.