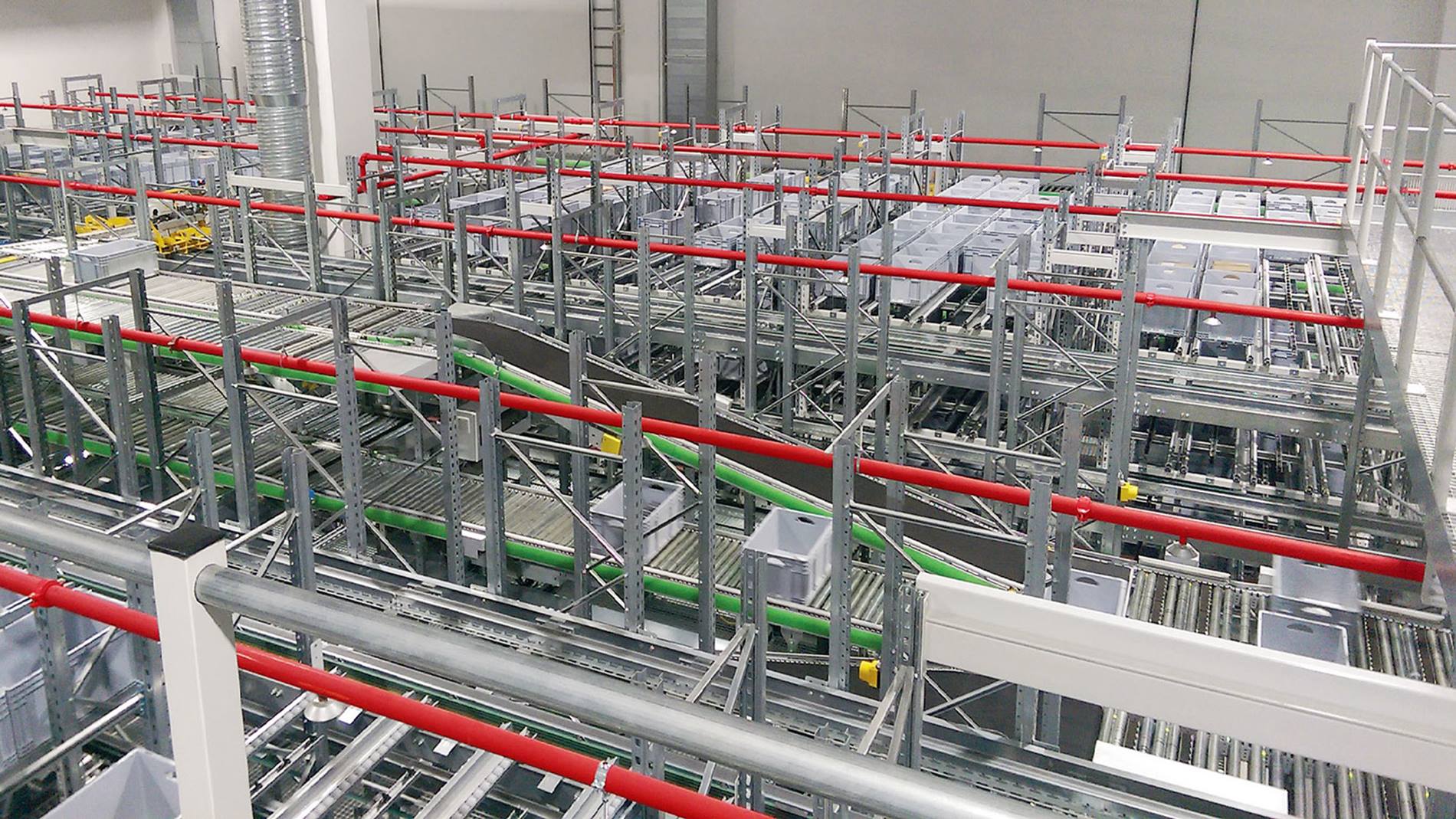
Hama, Germany: Multi-channel logistics with maximum flexibility
Hama supplies approximately 18,000 electronic products globally from cables and cameras to computers and household appliances via bricks-and-mortar and online stores. Challenges include fluctuating SKU count, product breadth and depth, shorter product cycles and higher return rates. Hama’s state-of-the-art automated warehouse picking,and shipping center integrates seamlessly with legacy infrastructure at its Monheim headquarters in Germany to provide the necessary speed, flexibility and efficiency for its intralogistics operation.
Automated multi-channel with maximized flexibility
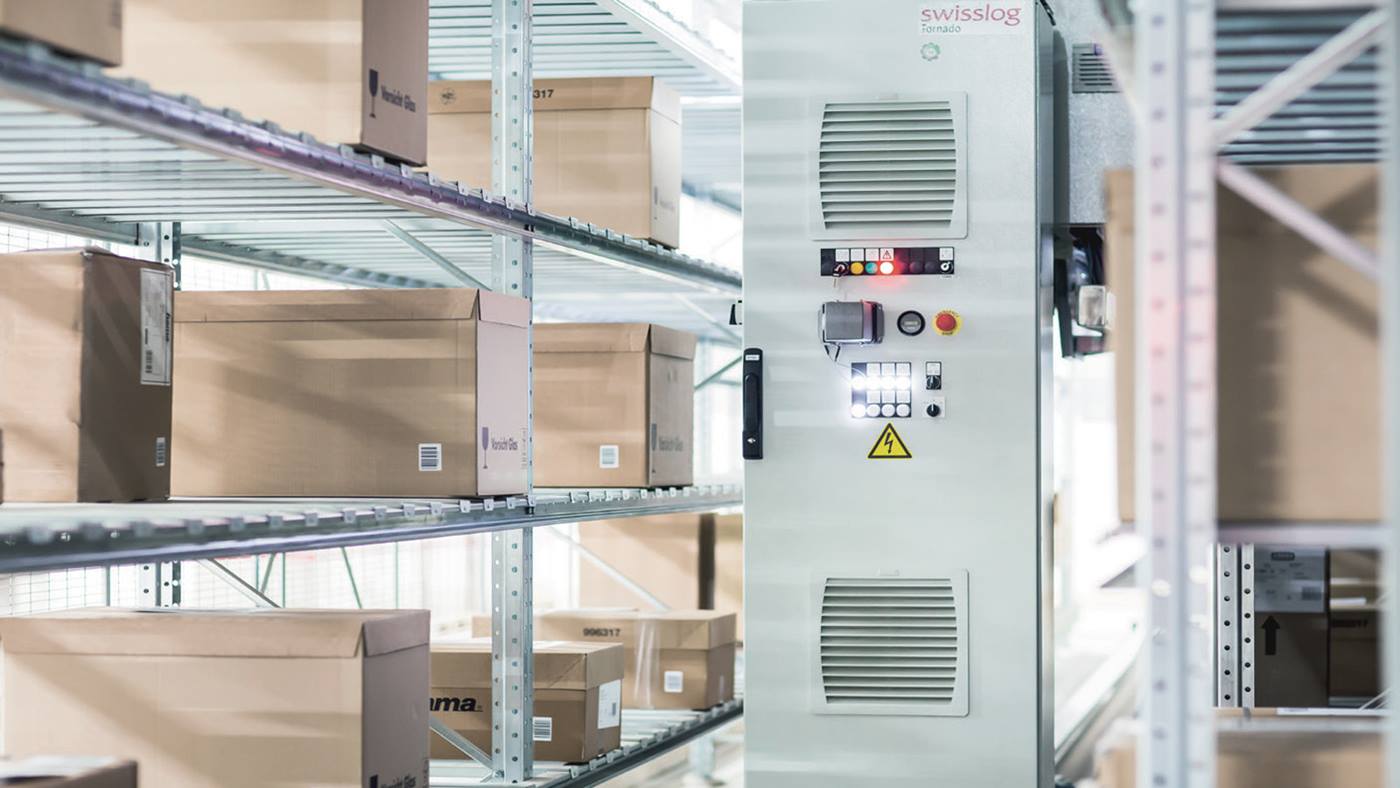
Automated and legacy systems
Hama’s integrated multi-channel facility includes two fully automated high-bay pallet warehouses, an automated carton and bin warehouse, a highly dynamic shuttle warehouse, an integrated order line buffer (OLB),and a shipping buffer.
This allows Hama to ship over 7,000 packages per day and up to 10,000 packages at peak times.
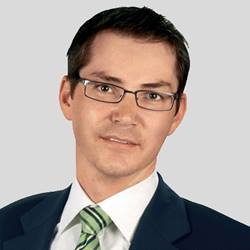
People and technology work in perfect harmony to ensure a smooth material flow. On average, there are half a million Hama items en route to our customers on any given day.