What’s In Your Warehouse?
Royden Edwards
13 March 2022
Reading Time:
3 min.
The Value of an Obsolescence Audit.
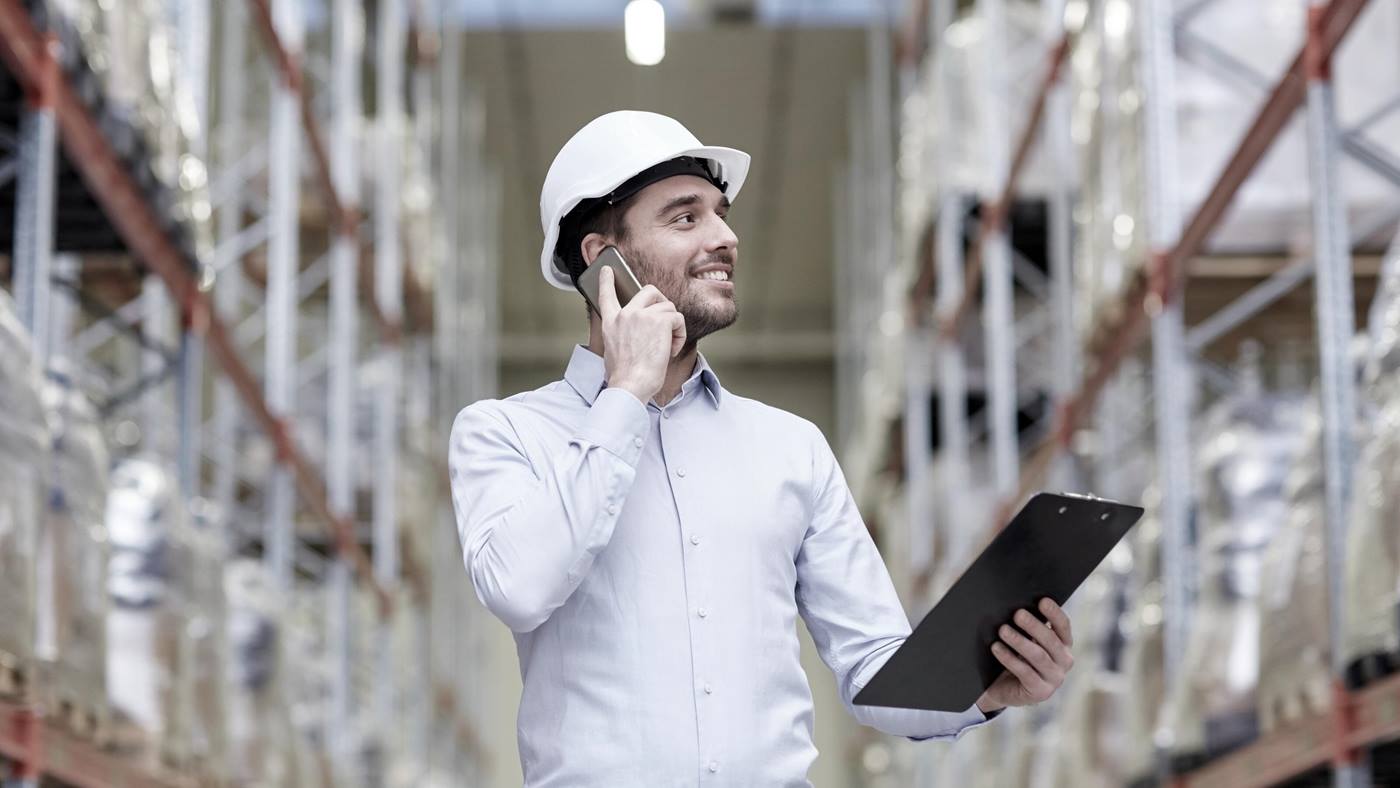
The extreme demands on warehouses over the last several years disrupted many maintenance schedules and, in some cases, forced warehouse personnel to bypass failed components to maintain continuity. These challenges have exacerbated an issue operators must continually guard against: obsolete electrical components in control panels and aging mechanical components such as sheaves, bearings, wheels and motors.
The problem of obsolescence demands particular attention today due to the shortage of replacement parts. Replacements for older or obsolete components could once be found relatively easily on secondary markets, but today material shortages and supply chain disruptions have increased competition for, and reduced the availability of, replacement parts on these markets. If a failed component can’t be sourced in a timely manner, production can be shut down while an entire control panel is modernized, or a motor replaced.
Warehouses can protect themselves from these threats by taking a proactive approach to equipment maintenance and component obsolescence. The foundation of that approach is an Obsolescence Audit.
What is an Obsolescent Audit?
An Obsolescence Audit is a thorough review of electrical and mechanical systems and components in critical material handling equipment by equipment specialists. Typically conducted by the material handling equipment provider, the Obsolescence Audit includes inspection and measurement of values that indicate whether equipment is operating as expected and the degree of mechanical wear the component has experienced.
Through the audit, equipment specialists establish an up-to-date and accurate record of the various components material handling equipment depends on and the current state and future risks to that equipment. The audit can also identify any changes to systems that introduce safety risks.
Using the audit, specialists can then identify components that have been obsoleted or are at risk of obsolescence as well as mechanical systems that are exhibiting signs of wear that reduce performance or increase the risk for failure. Equipment providers such as Swisslog have visibility into the technology roadmap for component providers, enabling plans to be put in place to update equipment to avoid situations where operators are dependent on components that have been end-of-lifed.
The audit is performed by trained field engineers using templates for the equipment installed at the site. The audit team is sized to ensure the process can be conducted within desired timelines and is coordinated to minimize the impact of any downtime required to accommodate measurement and testing on production schedules.
Results of the audit are used to develop recommendations for modernizing at-risk equipment and implementing any safety-related updates. The audit may also include recommendations to upgrade safety systems to bring them in compliance with current standards, such as adding doors to cranes or using light curtains in place of mechanical gates.
These recommendations can then provide the framework for a warehouse modernization strategy and a plan for performing the required modernizations that minimizes the impact on operations, supports throughput objectives and, if necessary, spreads the work over multiple budget cycles. This enables a more proactive approach to warehouse maintenance in which regular checkups can be scheduled every other year to ensure equipment remains in proper working order.
Who Should Consider an Obsolescence Audit?
Audits are valuable in a variety of situations but should especially be considered for warehouses dependent on mechanical conveyors, cranes and shuttle systems that have been installed for three years or more.
They can also reduce risks for warehouses that haven’t maintained a comprehensive list of components or have been forced to delay preventative maintenance practices over the last several years due to limited access to the warehouse by outside personnel or production demands that prevented scheduled downtime. For operators considering bringing in robotic automation technology, the audit can identify the necessary updates required to ensure existing equipment can integrate with new automation solutions.
Operators with the highest availability requirements or a high number of systems should also consider a Total Care relationship in which a field engineer is dedicated to the site to ensure equipment is in good working order and quickly resolve any issues that arise.
For more information on Obsolescence Audits and Swisslog’s approach to warehouse modernization, read the white paper, Modernizing, Upgrading and Expanding Warehouse Automation. To connect with one of our specialists, contact Swisslog.