How Frozen Food Can Tackle Climate Change
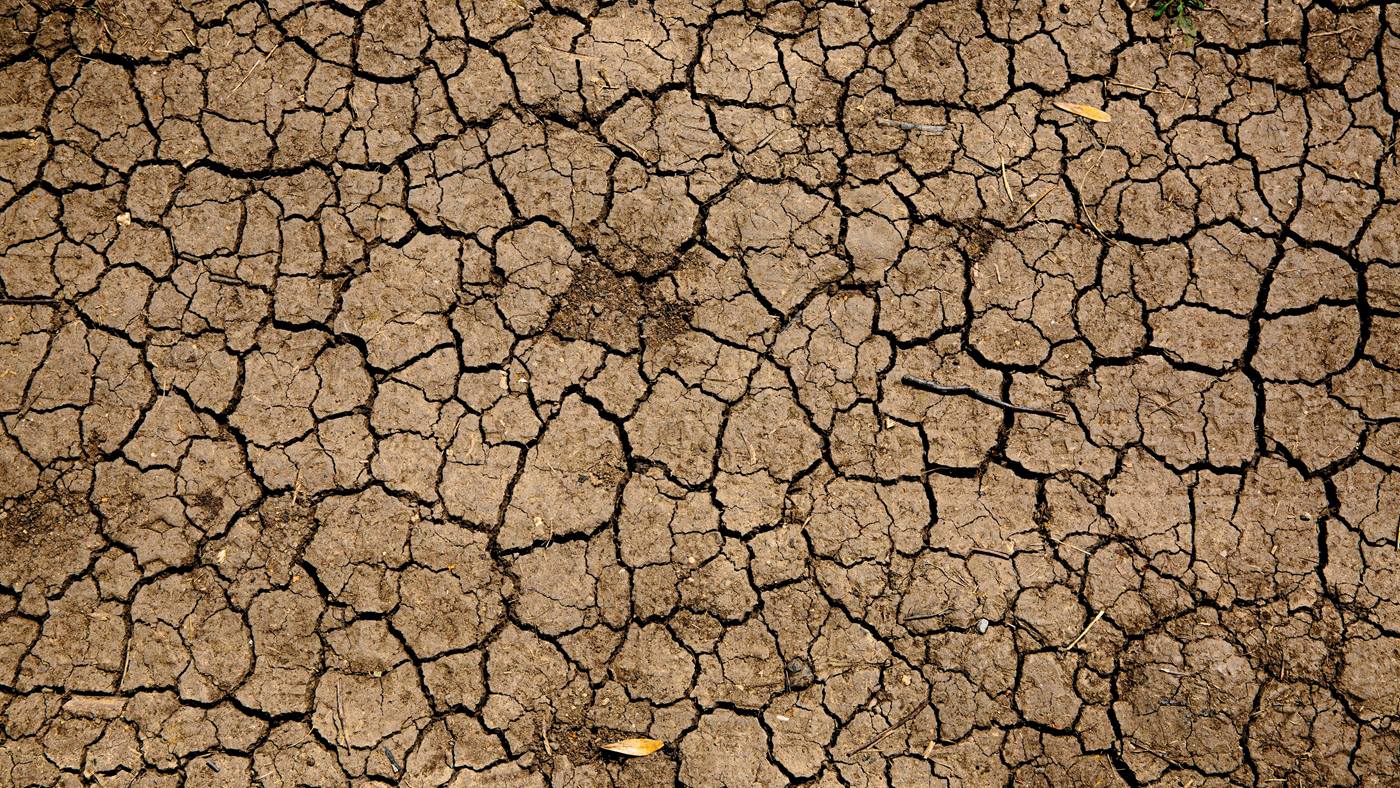
At first it might seem counterintuitive: frozen food can help the world to tackle climate change. We know chilling and freezing are energy intensive, so how can frozen food help to address one of the most important issues facing the world today?
In a year in which we have clearly seen the dramatic effects of climate change in parched earth and ruined crops, there is a growing feeling that we need to take more action before the situation gets worse.
Tackling food waste
An estimated one third of food across the whole supply chain is thrown away at present. For fresh produce such as vegetables or fruit, the figure is as high as 50%. A large part of this is due to our own consumption patterns, but waste also occurs away from home in restaurants and shops, and indeed food loss occurs throughout the entire supply chain.
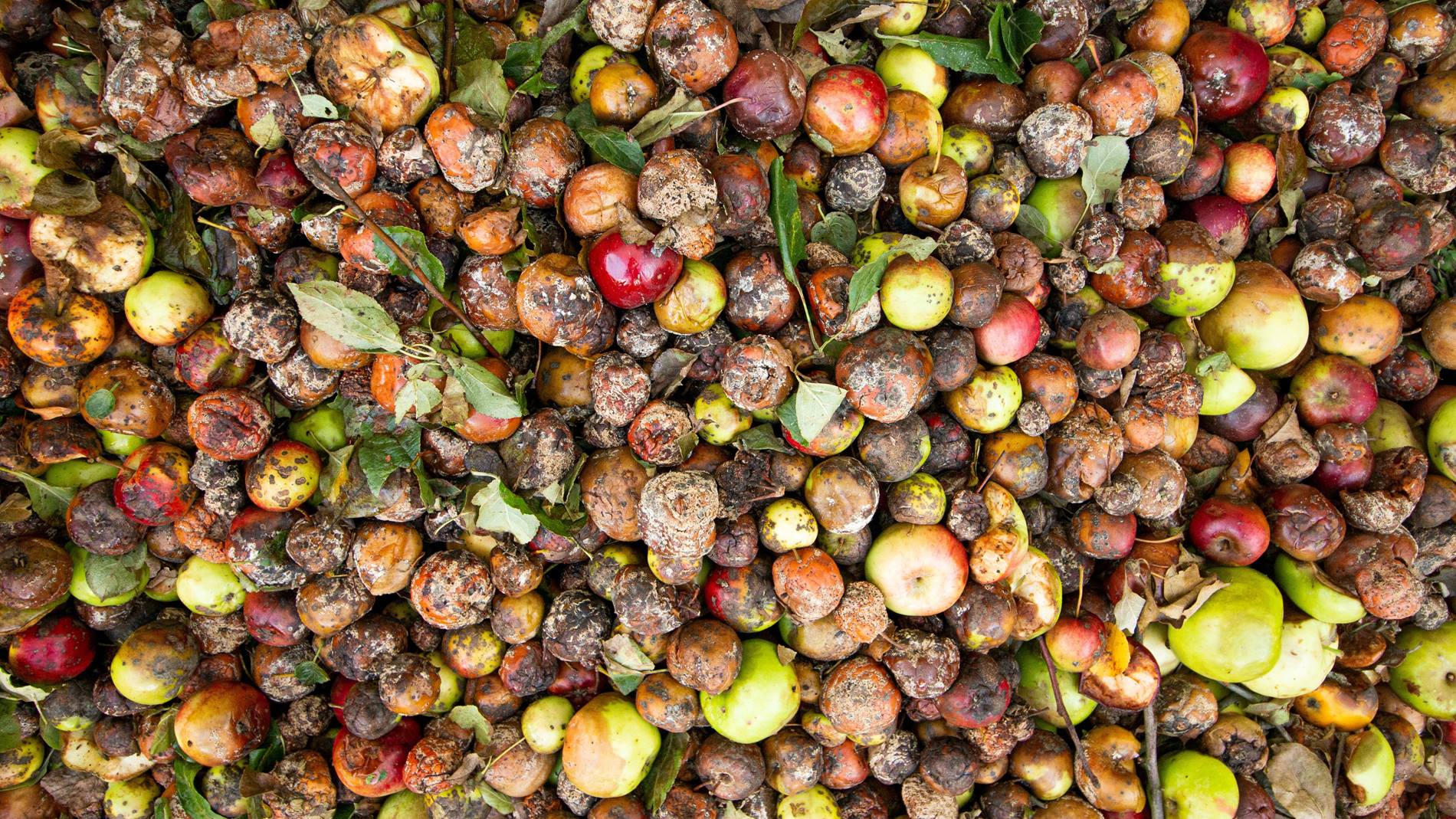
Buying frozen food and household freezing help to reduce food waste, as people throw away much less frozen food than they do fresh.
Generally, by reducing food waste and food loss, it has been estimated that we could reduce global emissions by as much as 8 to 10%. In this context, more frozen food can play a significant role in tandem with other factors such as buying fresh food locally and reducing food waste along the supply chain.
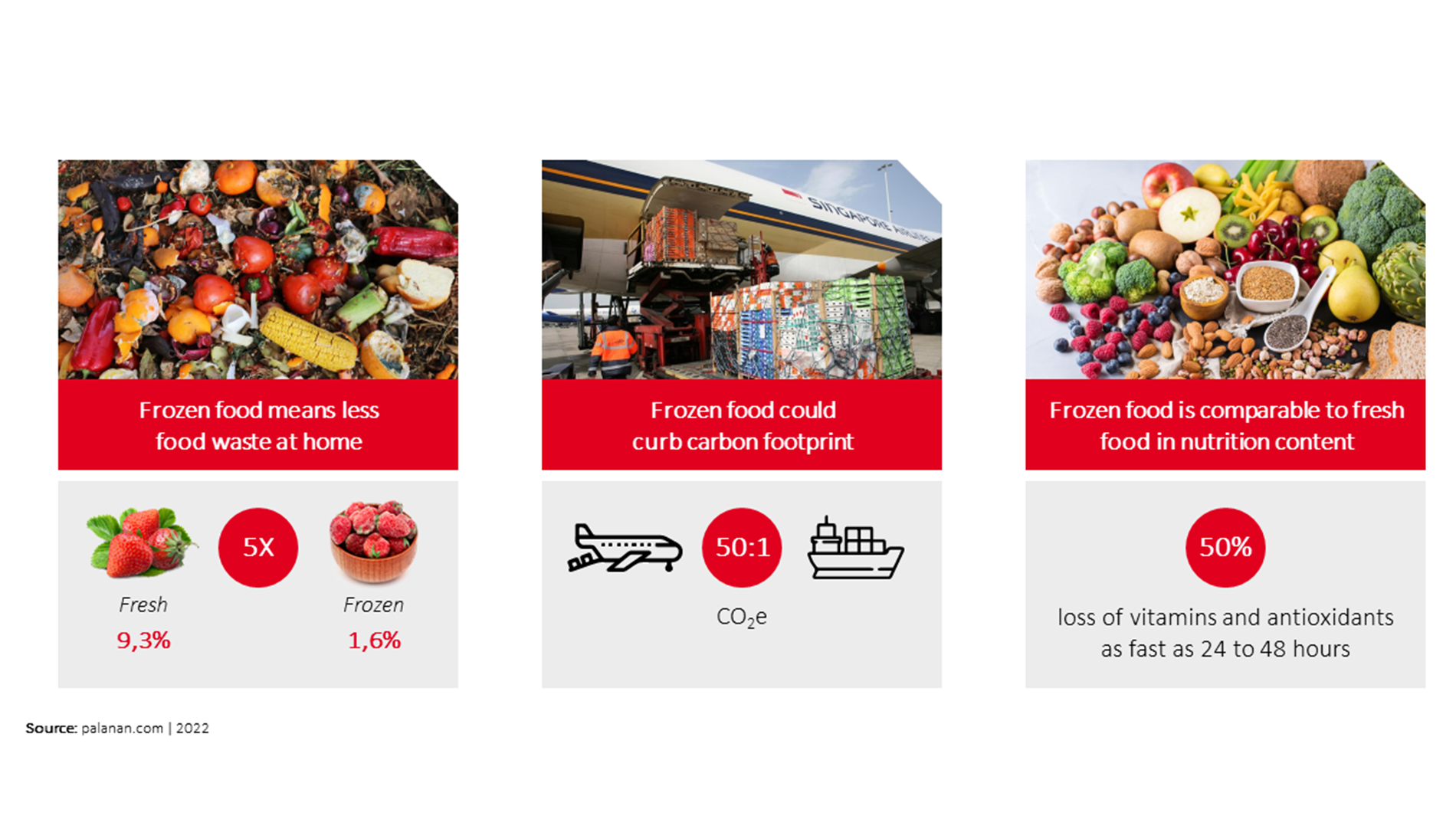
Advantages of frozen food
Even though frozen food uses energy, it can reduce transport and shipping emissions. Some highly perishable and out of season foods are flown (with huge emission costs) halfway round the world to reach their end market while still fresh. Freezing also preserves the nutrient value of fresh foods.
Although the deep freeze market grew substantially due to changing habits during the pandemic, the need to address these fundamental issues means that the sector is expected to grow further in the longer term.
Labor shortages
The frozen food sector has also been suffering considerably from labor shortages, especially since the pandemic. And as it is hard and sometimes unattractive work in the cold environment, the situation is getting even worse.
In refrigerated warehouses, refrigeration alone accounts for 65 to 75% of the total energy use. Add to this the huge increases in energy costs we are experiencing, and the need to optimize energy use in storage and distribution has never been greater.
How warehouse automation helps to tackle these challenges
If we compare the different technologies and solutions that are available for frozen food storage, we see four basic types of warehouse with varying operating performances and storage densities.
Traditional warehouses with manually operated forklifts are the basic solution providing low to medium performance and lower storage density.
To increase storage density, it is possible to use mobile rack storage, but performance remains at the lower end of what achievable.
Crane-based automation, such as using Swisslog Vectura cranes, has a wide range of applications offering a mix of performance and density. It is possible to adjust on the storage depth to increase density while maintaining the same operating performance.
Shuttle-based systems like Swisslog’s PowerStore are the best solution for highest storage capacity and storage density requirements, and offer highest performance and throughput.
Upgrading to these frozen food warehouse automation solutions allows you to reduce the air inside the building. This is because of the machinery needs less space to do the same job. Chilled high-bay storage warehouses can reduce refrigeration load by as much as 20% compared to low-bay facilities. The higher density of storage reduces the building footprint to as little as 25% the size otherwise needed as well as the total building volume that needs to be cooled.
Regenerative energy systems, lightweight design and the cycle optimization of Swisslog’s Vectura stacker cranes can also reduce energy consumption by as much as 25% compared to other alternatives. Vectura features multiple energy efficient components, a very lightweight design and a lower energy consumption to move goods.
A further benefit of automation is that there is no need to design human access within the storage building, so that the building design can be further optimized to reduce air space and energy draw. Heat dispersion through automated doors is also reduced, as they are kept open just long enough to allow a pallet to pass through.
Swisslog’s software also has several features, such as cycle optimization, that allow our solutions to reduce the overall energy consumption inside a complex plant.
The typical savings that automation can provide for frozen food storage are:
- Building footprint reduced to as little as a quarter (25%) that of an unautomated warehouse
- Roof and wall areas can be reduced by 30%
- The total building volume can be reduced by 25%
- Labor requirements can be reduced to a fifth (20%) of that required for an unautomated facility
These factors combine to offer a potential 40% saving in energy, at a time when energy costs are spiraling at an alarming rate.
> Discover more about Swisslog solutions for the frozen food warehouse.