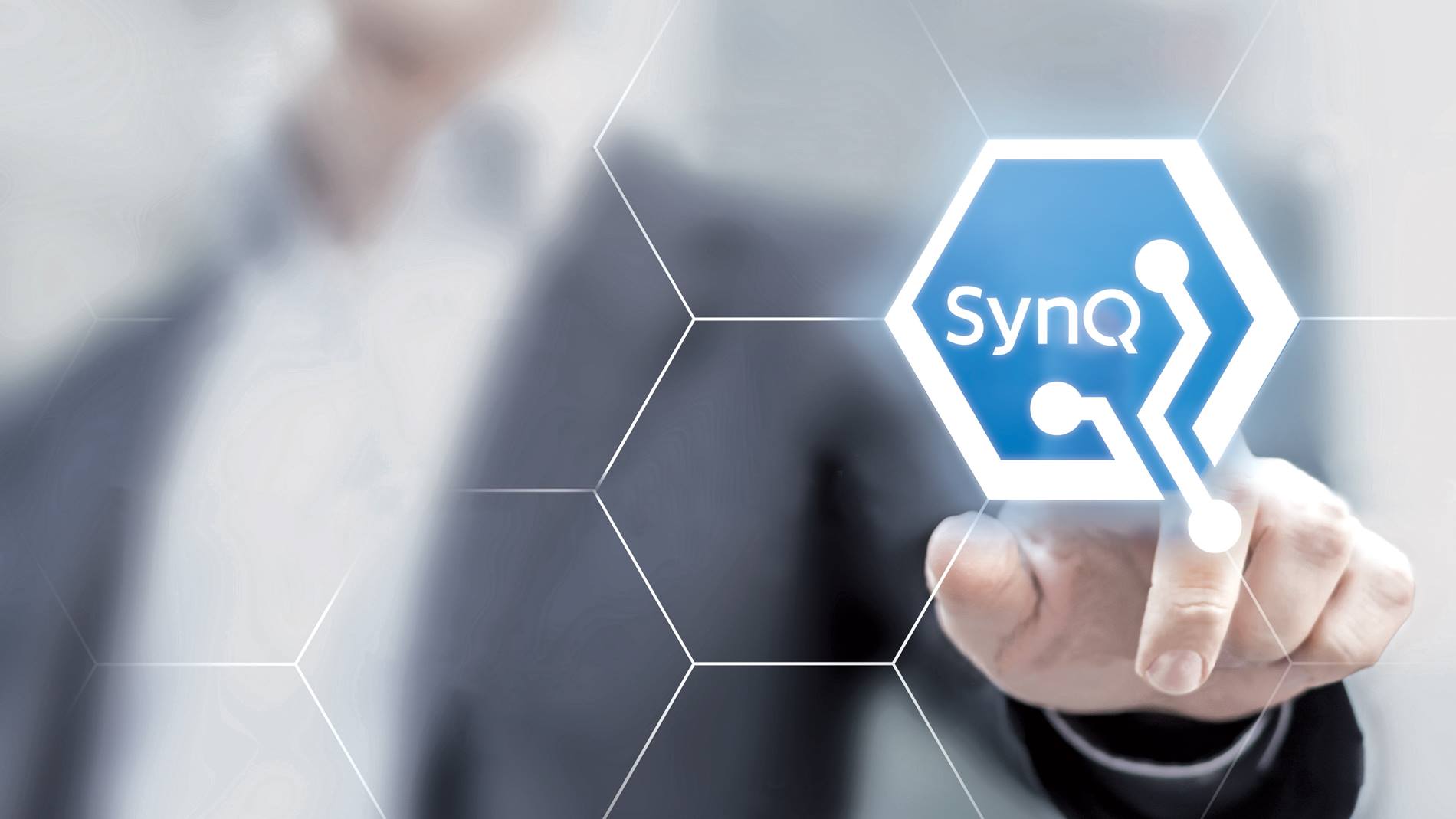
Four Ways to Future-Proof Your Warehouse
24 May 2017
Four attributes warehouse technology must have to protect against obsolescence and help future proof your warehouse.
It’s an interesting time for those making decisions about warehouse technology. Automated systems have emerged that can dramatically improve productivity, efficiency and space utilization. But, you’re likely also seeing a lot of news about how Industry 4.0 and the Internet of Things will enable smarter, more adaptive warehouses in the future.
Will today’s investments be made obsolete by future developments?
The reality is there’s always something new coming and it’s necessary for each organization to weigh the risks of waiting against the risk of adopting technology too early.
In the case of warehouse automation, the technology has matured significantly in the last three years and there are solid examples of successful deployments in almost every industry. In some industries, such as e-commerce, waiting simply isn’t an option. Customers are demanding faster delivery while the number of SKUs is making fulfillment more complex and the pressure on costs is increasing. Plus, automation providers have largely moved away from closed, proprietary systems that increase the risk of obsolescence.
Those developments have shifted the risk/reward assessment solidly in favor of reward—if you deploy technologies capable of adapting to future change. Here are four things to look for in warehouse automation technology to ensure the systems you deploy today can continue to deliver returns well into the future.
1. Software Integration
When warehouse operators first began to adopt automation, they found their existing warehouse management systems were not well suited to support it. They had to be supplemented with warehouse control and warehouse execution systems, which provided the necessary functionality but also limited the ability to collect and use data.
Monolithic WMS software that takes a top-down approach to warehouse management lacks the flexibility to easily adapt to changing conditions. The new approach, as represented by Swisslog’s SynQ platform, takes a bottom-up approach to software design to integrate all of the functionality required to support an automated warehouse in a single, modular platform. This decentralized architecture allows the software to easily adapt to changing equipment and requirements and will become the standard in the future.
2. Modular design
With demand rapidly shifting from traditional retail to e-commerce and omni-channel sales, few businesses can accurately forecast future warehousing requirements. This has caused inflexible, bolted-down automation systems to fall out of favor. They are being replaced by modular goods-to-person systems that can easily be scaled and even re-purposed in a new environment. Mobile robots, such as CarryPick, adapt quickly to changes in demand and enable a pay-as-you-grow approach in which additional robots and pick stations are added as needed.
The architecture of the SynQ platform also provides future flexibility. Through its decentralized, modular design, it enables users to deploy only the functionality they need while maintaining the ability to add functionality and business intelligence tools as needed.
3. Business intelligence
While the future is difficult to predict, one thing is fairly certain: the most efficient warehouses will be those that can effectively use data to optimize processes, enhance availability and anticipate changes in demand. The problem isn’t necessarily collecting data, it’s being able to integrate it across systems and visualize it in ways that allow it to be easily used by warehouse personnel. A growing family of business intelligence tools is emerging that provides unparalleled visibility into equipment operation, material flow and process efficiency. The warehouse management system of the present—and the future—must allow for easy integration of business intelligence tools and consistent visualization of the insights they provide.
4. Support for virtualization
Virtualized warehouse management isn’t coming; it’s already here. The SynQ software platform, for example, combines sensor data with warehouse models and simulations to create a digital “copy” of the warehouse. Today that enables real-time condition monitoring, material flow monitoring and process modeling—all powerful tools in improving availability and productivity.
Virtualization also establishes a foundation for future developments that will shape warehouse management, including:
- Virtual Reality. At ProMat 2017, we demonstrated the capability to combine SynQ’s virtualization capabilities with a VR headset to provide a detailed, 3D view of what automated materials handling systems will look like and how they will perform under specific order profiles.
- Augmented Reality. Check out this video showing how Swisslog is combining the virtualization technologies of SynQ, with the augmented reality capabilities of the Microsoft HoloLens, to improve how we deliver services. Another interesting application for augmented reality is gamification. As products like HoloLens become industrialized, workers will be able compare their performance with others in real time to normalized task time across the workforce and optimize productivity.
No one knows exactly what the future will bring, but with systems that are integrated, modular, intelligent and enable virtualization you can future proof your warehouse to adapt to change and take advantage of new technologies as they emerge.