Automation advances drive the eco-friendly warehousing and logistics facility of the future
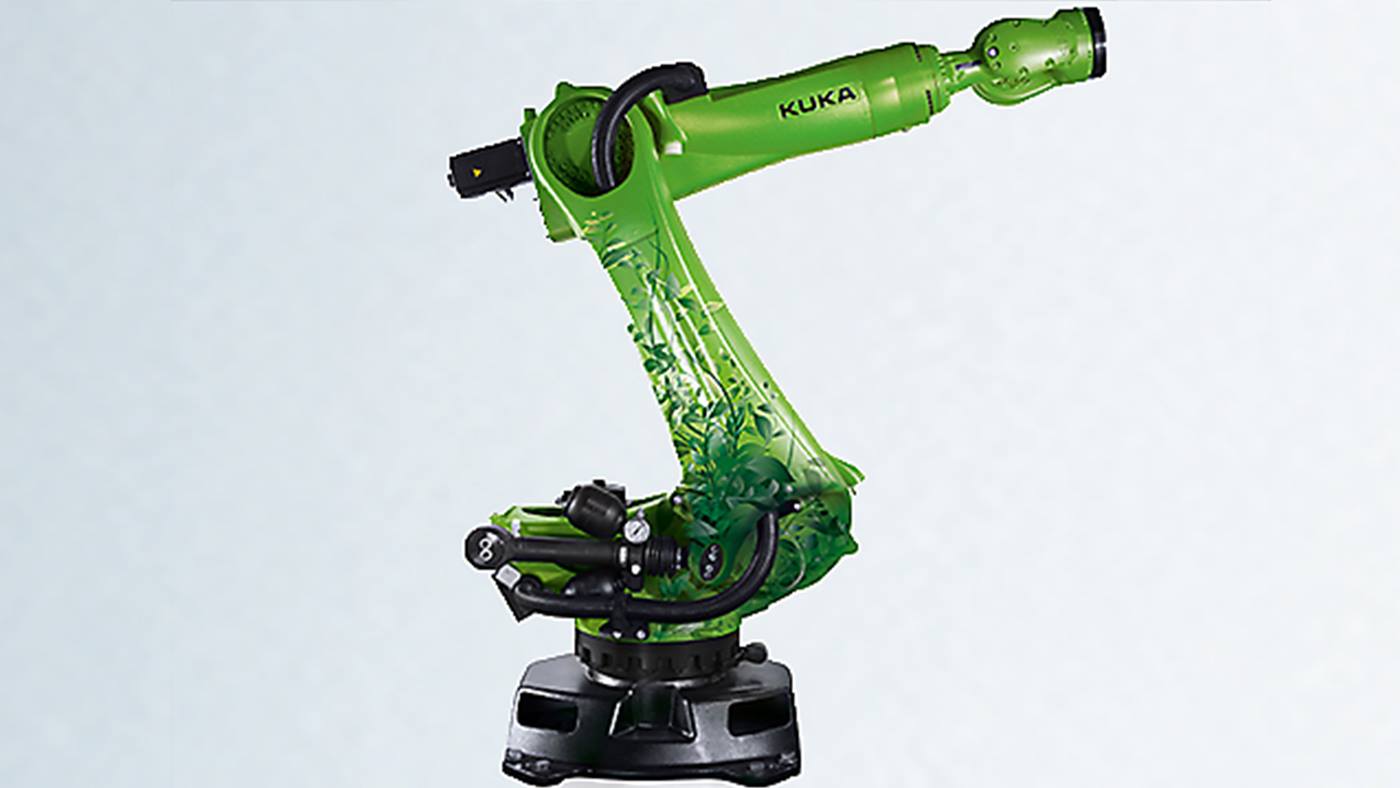
Less space, better hygiene and reduced fossil fuel needs are major assets for distribution facilities located in densely populated areas or near residential areas.
Swisslog’s comprehensive portfolio of data-driven, flexible and robotic material handling solutions enables increased productivity, shorter order cycle times and faster response to change. These qualities, supported by an engineering focus on sustainability, enable a range of environmental benefits. Swisslog technologies with built-in sustainability features include:
Vectura Cranes, which use a unique low-weight mast design and regenerative power and braking modules to deliver industry-leading efficiency while retaining outstanding performance and reliability.
CarryPick goods-to-person solution, which features energy-efficient robots and a modular design that can extend the life of an existing warehouse, eliminating the environmental impact of new construction.
PowerStore automated storage and retrieval system, which enables storage density 60% better than manual systems, which is particularly important in energy-consuming cold storage facilities.
Swisslog’s GreenLog programme provides a systematic process for continuing to advance the energy efficiency of the company’s solutions as well as optimising the sustainability of industry processes. By analysing the energy consumption of each solution based on scenarios that reflect real-world operating conditions, we will provide our customers with expected energy consumption data for each solution to support their equipment selection decisions.
Profitability and sustainability - a win-win
The efficiency and productivity benefits of automated warehousing or logistics operations have been proven in service worldwide. And these benefits contribute to better profitability over a sustained period, as operations are further tailored to meet customer needs and eliminate inefficiencies.
When you add environmental sustainability benefits into the same equation, it’s truly a win-win for the operator. And while the environmental win might be a desirable, but secondary benefit for now, it’s only a matter of time before the majority of new facilities are constructed to be as eco-friendly as possible – and existing facilities are more widely retrofitted to achieve greater standards of environmental sustainability.
As this global trend towards greater sustainability continues, automation will be a major driver in making it possible.
Shifting away from fossil fuels
The carbon footprint of a warehouse or logistics facility is further reduced when automation technologies perform tasks previously undertaken by fossil-fuel powered materials handling alternatives.
Heavy-duty manually operated machinery emits more CO2 into the environment, compared with its electric counterparts, so automated machines can help reduce total carbon emissions of a facility. Additionally, automated technologies are far quieter than fleets of fossil-fuel powered vehicles.
Electric vehicles provide an alternative to fossil fuels, but they are not cheap, and the technology is constantly evolving. Even fleets of individual electric standard lift vehicles can cost from $20,000 - $50,000 each to purchase, or $200-300 per week to lease, or more – and they need continuous updating.
Not only is less land required for a fully functioning warehouse, but the carbon footprint is further reduced when you consider that a smaller space will need less electricity, water and other resources. Based on Swisslog’s past projects, when comparing a manual warehouse to an automated storage and retrieval system (ASRS), up to 60% less space is required.
So, if a business needs 10,000m2 for a manual warehouse, but an automated solution means you can perform all the company’s delivery needs within a 4,000m2 space, if you take a price of $125 per square metre in Sydney, the leasing costs reduce by 750 thousand dollars per year.
And existing sites that are retrofitted or refurbished with automation technologies can use the space saved for other profit generating activities or optimised processes for changes in business model.
Naturally these figures are only a hypothetical, but there will always be some level of savings by reducing the size of the space needed for the warehouse and logistics operations.
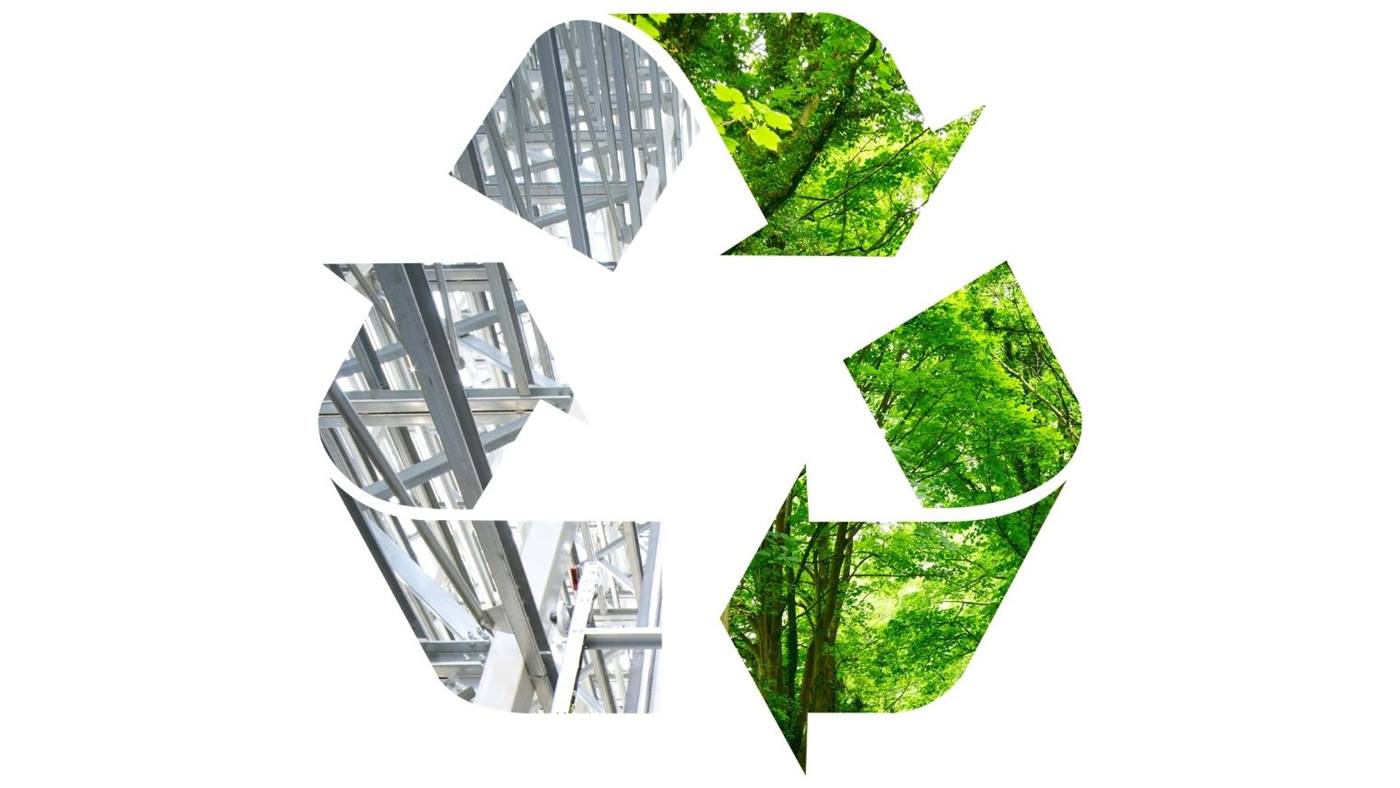
GreenLog supply chain sustainability programme
To optimise sustainability practices and design, and seek continuous improvement, Swisslog has implemented a comprehensive internal programme for improving supply chain sustainability.
Swisslog’s GreenLog programme uses energy-efficient solutions and less wasteful processes to optimise environmental outcomes for companies worldwide that are using its proven automation technologies.
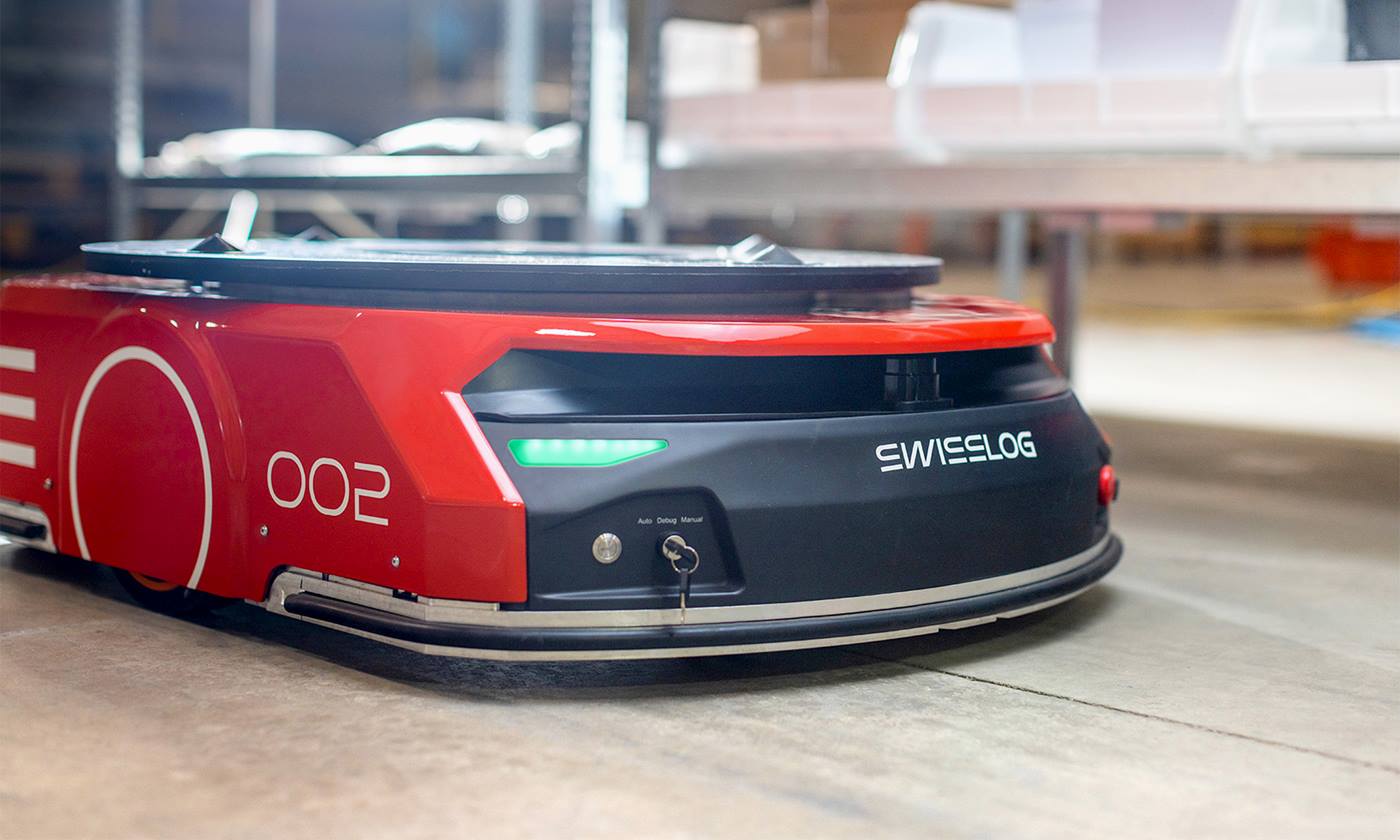
Health, Safety & Hygiene
Reduced manual handling of goods – particularly in food, beverage and pharmaceutical applications – has broader long-term sustainability benefits to society, including lowering the risk of product contamination or product tampering.
The crippling costs or a product recall – including product disposal, business interruption, customer reimbursement as well as damage to brand reputation – are something no business wants to endure.
Naturally, hygiene benefits have never been more apparent than in a post-Covid world, where hygiene is top of mind for all companies and individuals. In a post-Covid world, hygiene is not an option for a sustainable business – it is a necessity.
Long-term sustainability is also further enhanced by a greater level of worker safety. With workers no longer having to go deep (or high) into racking to retrieve products, the risk of injury (both repetitive strain and accidental) is reduced. Workers in an automated warehouse – from technology controllers, to maintenance crews, to warehouse managers – typically have a safer, healthier job than manual labour workers in older warehouses.
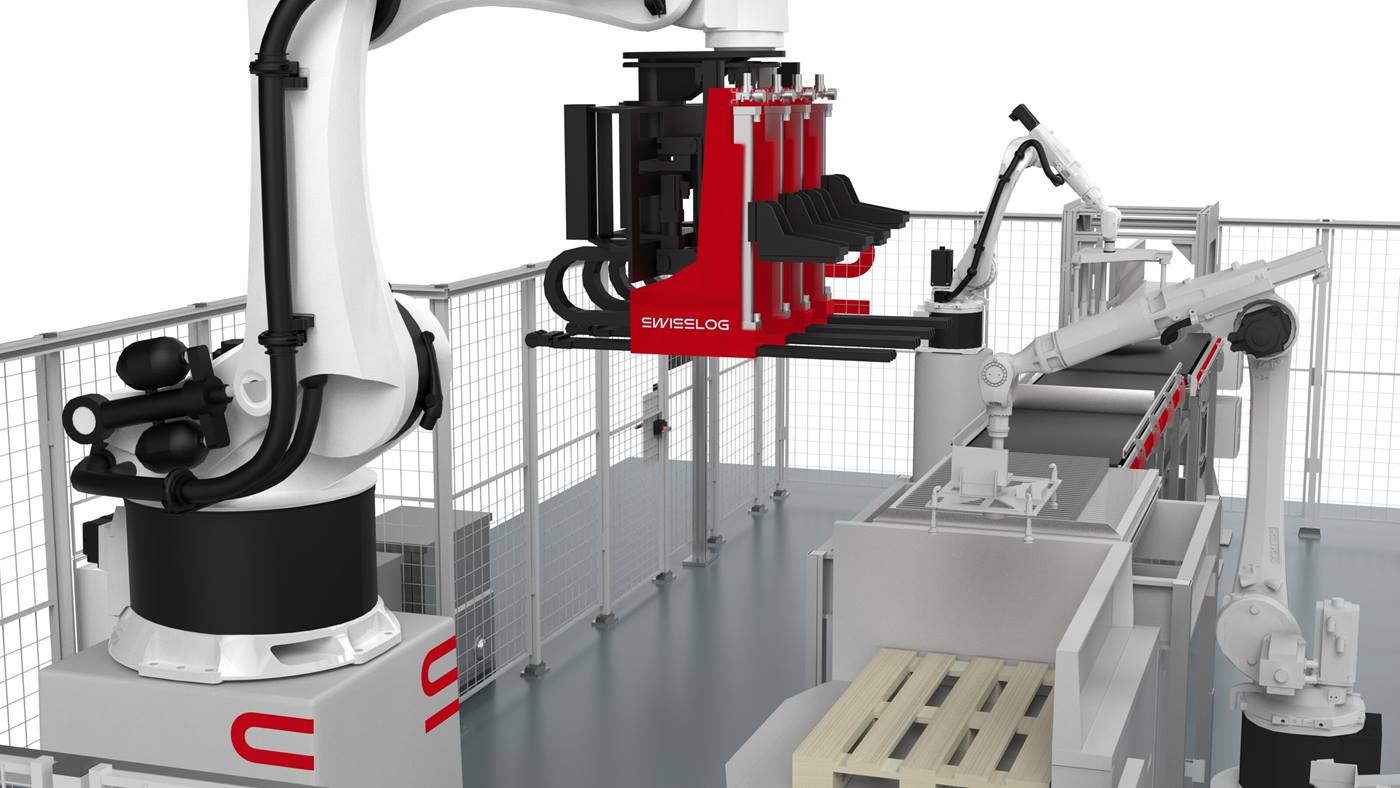
One change many larger companies are adopting globally is the utilisation of more environmentally friendly packaging, including materials that biodegrade more easily over time.
However, a disadvantage of eco-friendly packaging is that it’s often more prone to breakages in the handling process. Automation technology can apply a smooth, gentle touch, which has allowed greener packaging to be employed by more companies. From conveyors to pickers to robots and automated vehicles, automation technologies have allowed for greener packaging to be used without compromising the integrity of the product during the handling process.
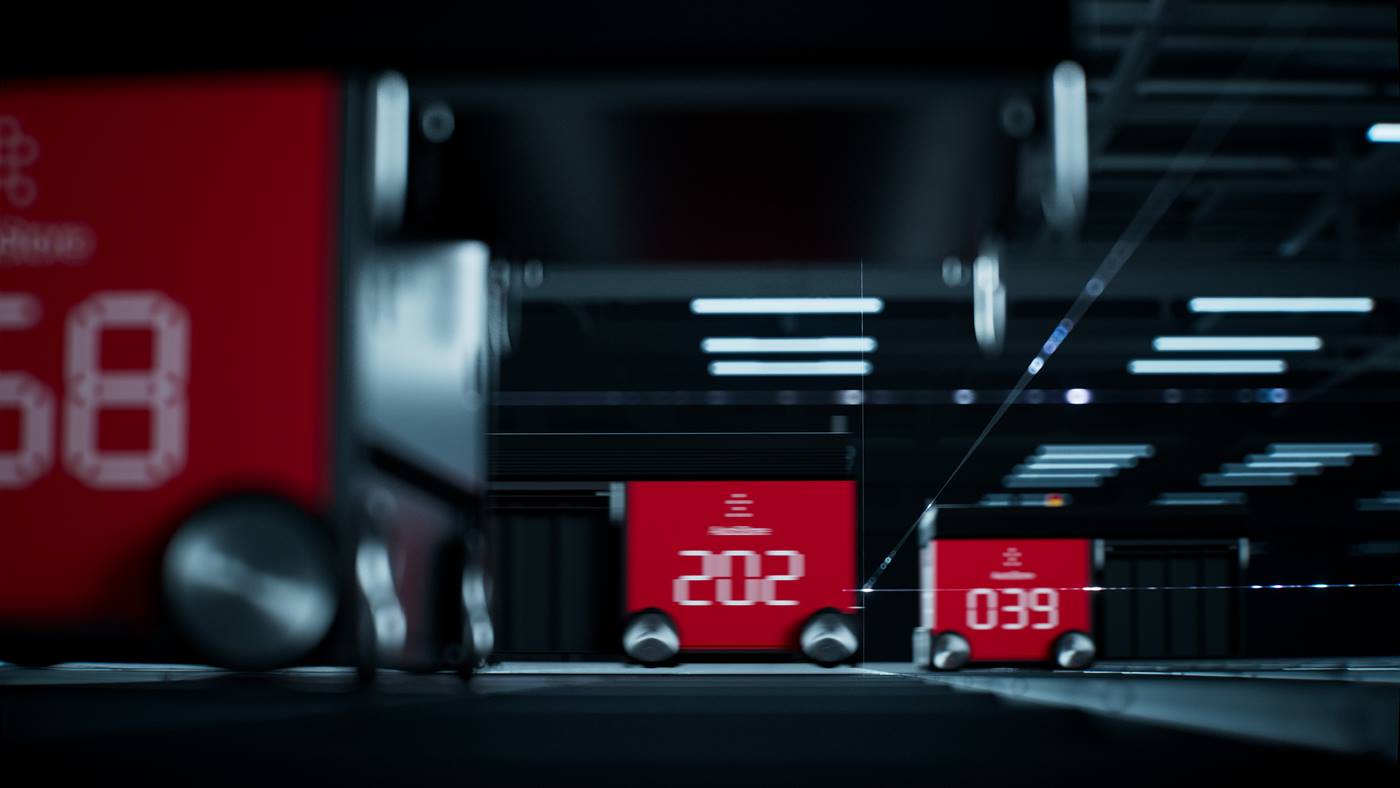
A smaller footprint
Automation has many benefits including the environmental advantage of occupying a smaller physical footprint in a warehouse or logistics facility. Products can be stacked neatly, almost right to the roof, and an automated storage and retrieval system (ASRS) can swiftly select products from anywhere in a compact grid.
Reduced power consumption
An ASRS can operate in the dark, leading to significant savings in electricity and carbon emissions. And, as technology advances, further power-saving features are incorporated into automated warehouses, including functions where robots ‘go to sleep’ to save power when not in use.
Off-peak power can also be utilised, with automated technologies able to work around the clock, and be controlled remotely, which provides a cost-saving as well as environmental benefits.
Typically, an intelligent Warehouse Management Software system will control the entire automated operation, and will automatically calculate the most efficient way to operate all machinery and achieve desired outcomes.
With Industry 4.0 advances – machines talking to machines – operators aren’t required to be on-site 24/7. They can control the technology remotely, saving road traffic to and from the plant.
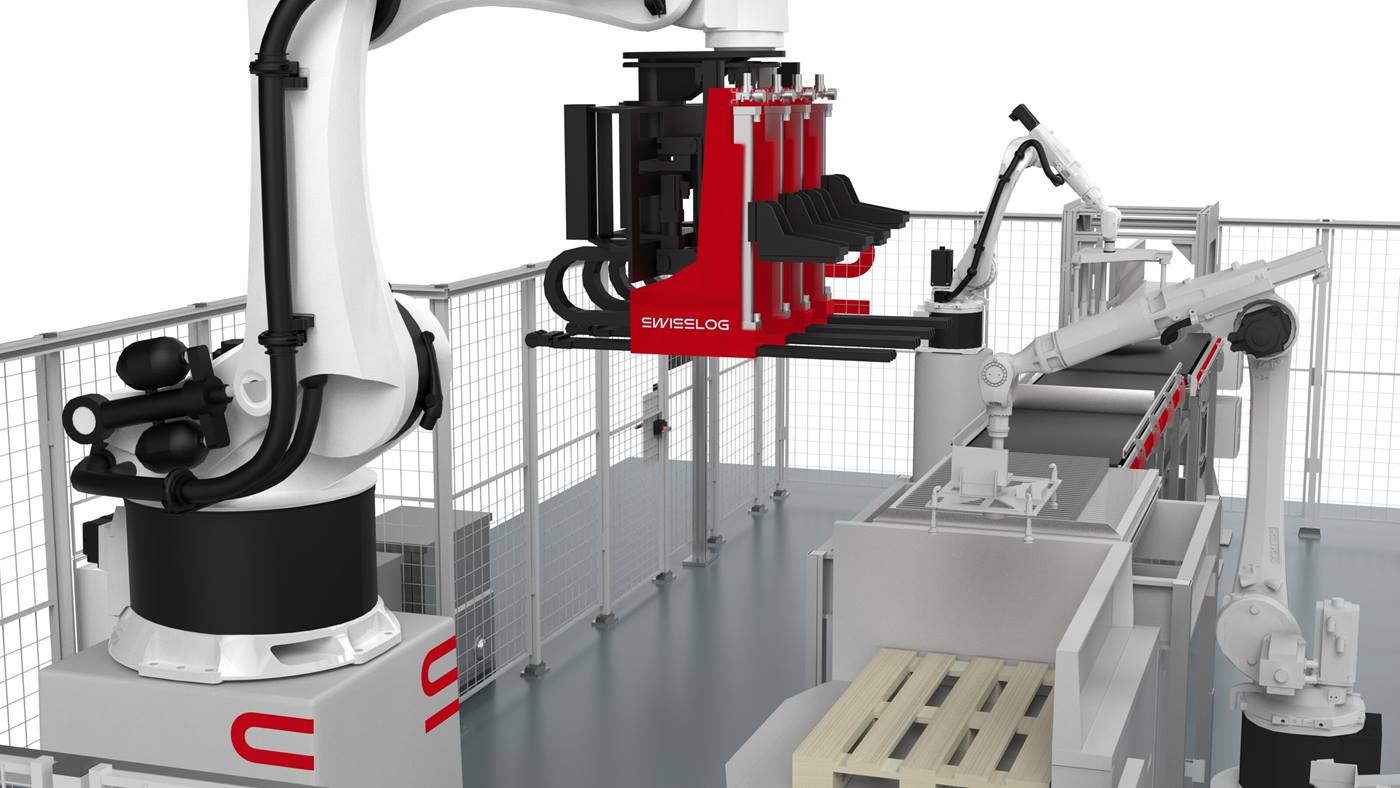
One change many larger companies are adopting globally is the utilisation of more environmentally friendly packaging, including materials that biodegrade more easily over time.
However, a disadvantage of eco-friendly packaging is that it’s often more prone to breakages in the handling process. Automation technology can apply a smooth, gentle touch, which has allowed greener packaging to be employed by more companies. From conveyors to pickers to robots and automated vehicles, automation technologies have allowed for greener packaging to be used without compromising the integrity of the product during the handling process.