Transitioning from a semi- to fully automated warehouse and beyond
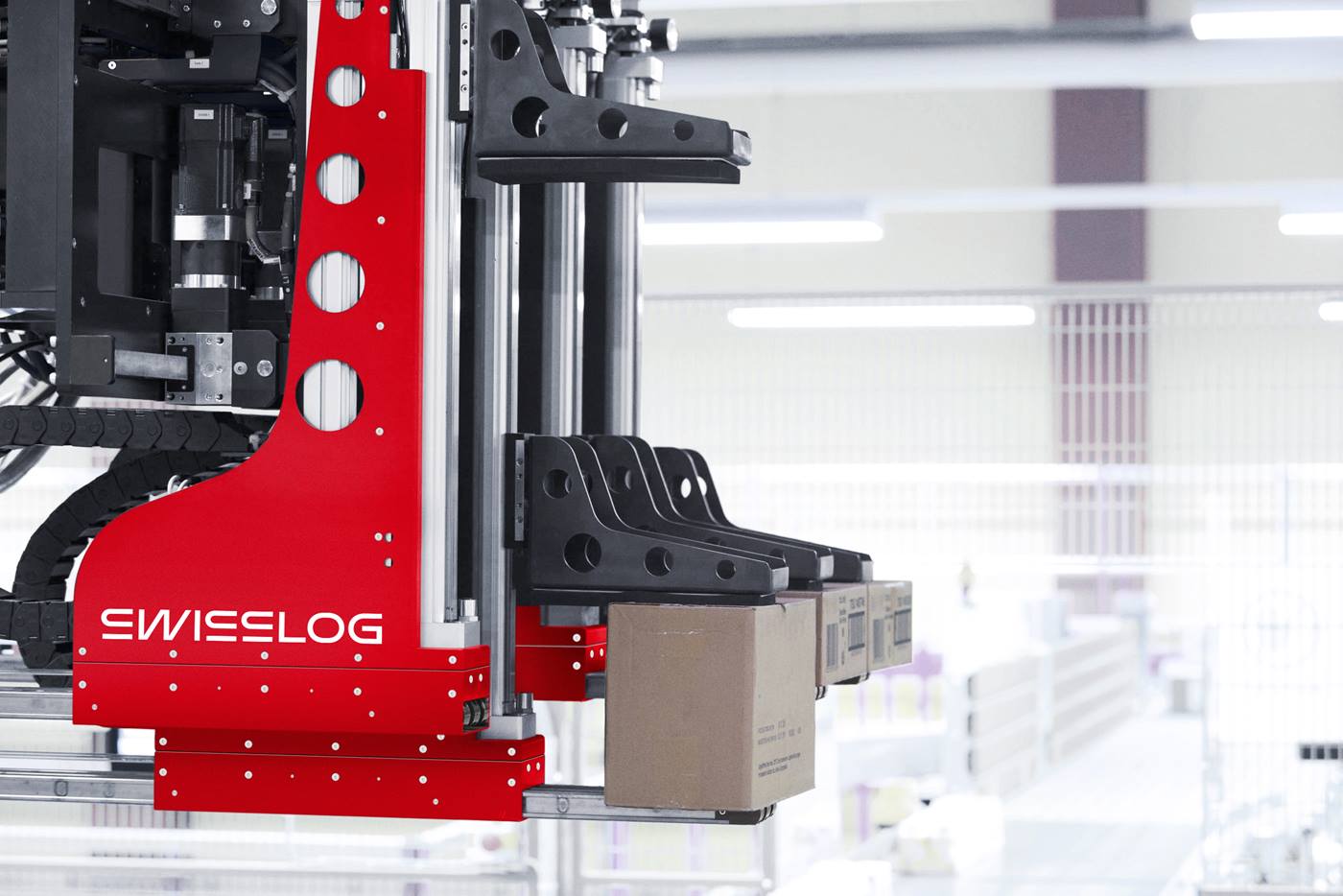
Those who are ready to take the next step and upgrade to a fully automated warehouse stand to benefit significantly in terms of profitability, customer service, and operational efficiency. Selecting the right automation partner and technology for each unique application is crucial for such an important long-term investment.
Swisslog VP Global Business Acceleration & Managing Director UK, James Sharples answers eight key questions about the transition from a semi- to fully automated warehouse, and what lies beyond.
1. What are the benefits of upgrading from a semi to fully automated warehouse?
Whether you’re starting from a semi-automated or mechanized warehouse (i.e., automatic storage and automatic replenishment), one of the main benefits of upgrading to a fully automated warehouse is modularity. As demand grows, the modular design can be scaled and continue to drive profitability. With more advanced automation solutions, operating costs are further reduced.
2. For companies looking to upgrade, what must they consider first?
Long-term planning is essential, which is why it’s so important to have an experienced and dedicated automation partner like Swisslog. Solution and site development typically take 2-3 years, and when the upfront costs are considered, ROI is longer than for simpler solutions. However, once that ROI is achieved, the long-term benefits far outweigh semi-automated or manual systems.
In many cases, the site will be a new build with end-to-end automation, so the business must consider how the new automated site will fit into the overall supply chain architecture.
3. How easy is it to upgrade a semi-automated solution to a fully automated one?
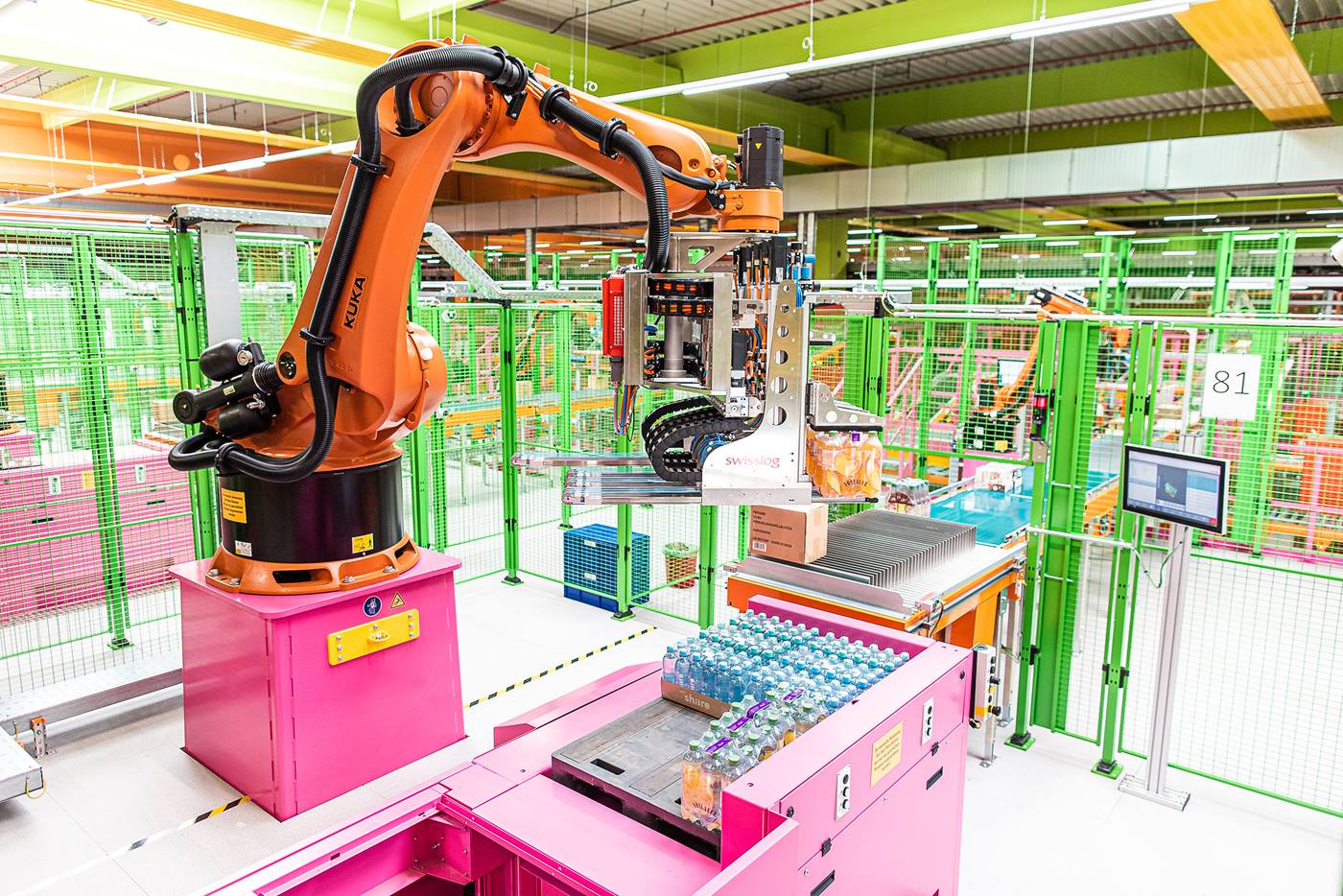
The ACPaQ modules have many interchangeable features, so converting from a set of manual depalletizing stations to a fully automated layer picker with case singulation and tray loading can be done in a similar footprint. The case racking structure can be expanded to include additional aisles, increasing storage and retrieval capability.
It’s also worth noting that the ability to upgrade to a fully automated system is determined by the products being stored and retrieved, which is typically beyond the retailer’s control. However, as automated solutions gain traction, packaging formats are expected to evolve and become more automation friendly.
4. How important is having a good WMS software, like SynQ, when operating a fully automated warehouse? And does it help in the transition?
It is vital that software is considered from the outset. This is not an add-on; rather, it is fundamental to the management of inventory and processing of orders through the system from start to finish. Product inventory must be managed in pallet, layer and case formats and the strategy for optimizing this is critical.
Order planning occurs at both the transport vehicle and pallet / rollcage levels and must be tailored to suit not just one generic store format, but many. To achieve this, the warehouse automation software must assume greater responsibility than a traditional WMS or an automation WCS. While the customer can keep their own WMS, many of the decisions about “what is stored where” and “when it will be picked” will now need to be made within the warehouse automation layer to guarantee performance.
5. How does a company make the most of a fully automated warehouse and keep optimizing performance to deliver the best service to its customers?
As an automation partner, Swisslog can perform health checks on the installed solution, focusing on the equipment efficiency and, more importantly, how well the system meets store order expectations. Operational assessments can be made remotely and planned changes to the solution can be tested on a digital twin to determine potential impacts.
6. Once the upgrade to fully automated warehouse is complete, what comes next?
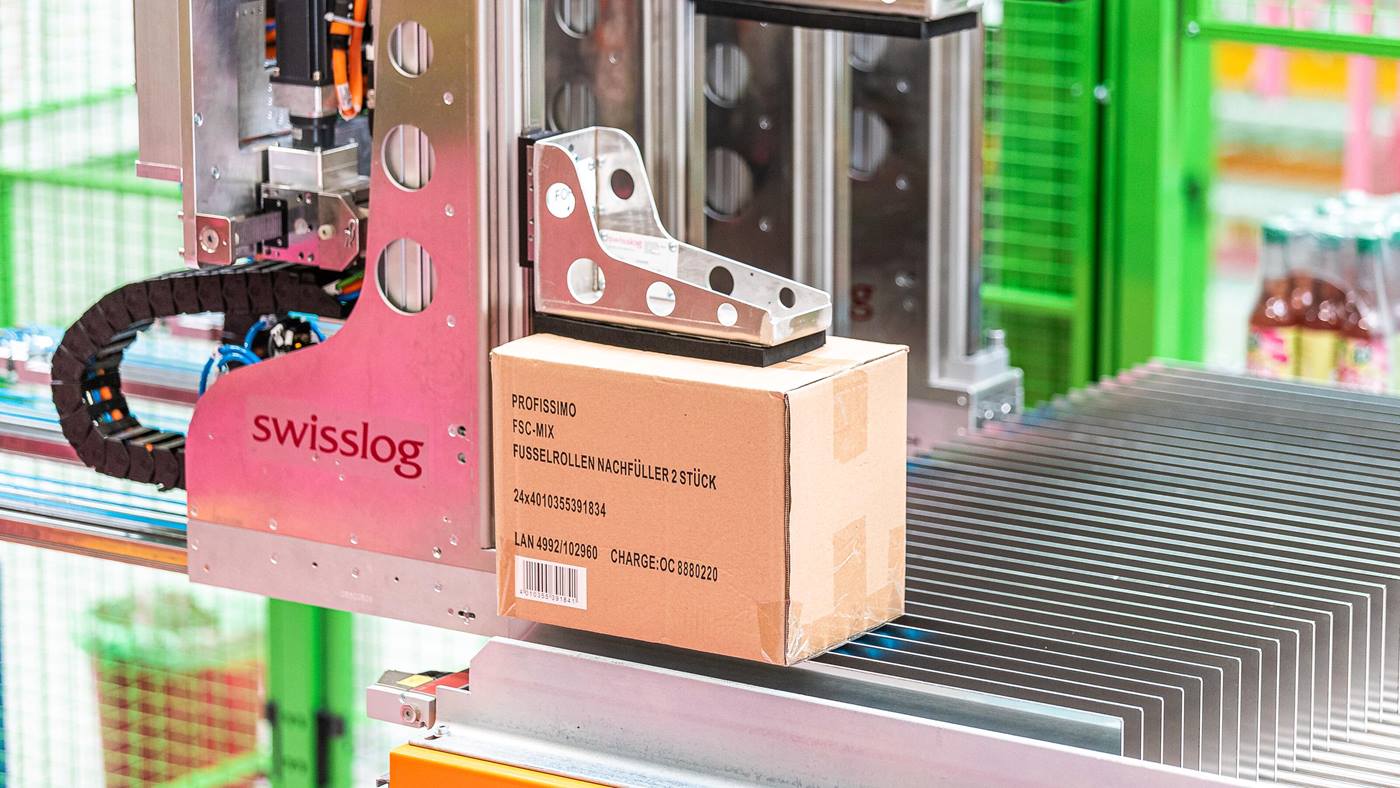
7. What role does an automation partner like Swisslog play in the upgrade and ongoing maintenance and optimization of a fully automated solution?
With such a large investment, mixed case palletizing solutions tend to operate around the clock. Planned maintenance is essential to the longevity and operational performance of the solution. Operations can continue while specific sub-systems are serviced, with no loss of access to vital stock.
Swisslog provides a comprehensive service, including spares, IT support, visited maintenance, resident site maintenance, and upgrades.
8. What are the unique advantages of ACPaQ?
After researching many different mixed case palletizing solutions, I would list the main benefits of ACPaQ over alternative technologies as follows:
- Best in class flexibility – the ability to get any case from and to any station gives unrivalled flexibility. The ability to add goods-to-person picking technology is simple and easily integrated.
- Robotic handling excellence – Developed within a focused Robotic Technology Center with the strength of KUKA behind us, the solution utilizes industry leading robots, grippers, and vision systems.
- Delivered by a trusted partner with proven technology – A growing number of references in the food & beverage industry demonstrates our expertise.
To learn more about the automated mixed case palletizer ACPaQ, or for assistance in upgrading from a semi- to fully automated warehouse, speak to a Swisslog expert today.
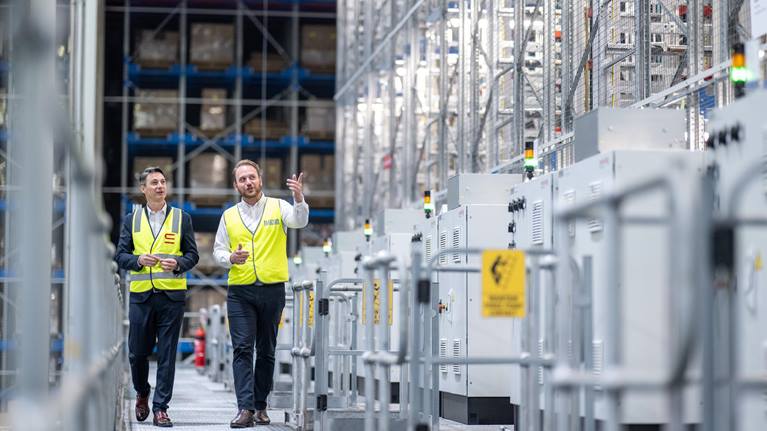
Warehouse automation introduces efficiencies that enable organizations to increase productivity, respond faster to orders, and increase storage density. However, securing the capital required to support these initiatives is a hurdle some organizations struggle to overcome. Part of the challenge may be that these organizations fail to fully consider the hidden costs of maintaining the status quo. From falling behind competitors to rising costs to unpredictable service levels, carefully considering the costs of inaction should always be considered as part of the business case for warehouse automation.